Automated Guided Vehicles come in a variety of transportation and navigation types, from low-floor models to tracking versions. Despite the general term AGVs encompassing all these models, each has its unique features, benefits, and limitations.
Understanding the adoption of Automated Guided Vehicles requires an understanding of your own factory’s specific needs and the industry you operate in. This goes beyond mere comparisons with other technologies like Autonomous Mobile Robots (AMRs) to truly grasp how AGVs can optimize your operations.
In this article, we will try to help enhance transportation efficiency and safety across logistics and manufacturing environments in your business by guiding you in selecting the best Automated Guided Vehicles. We will also compare and showcase leading AGV manufacturers to inform your decision-making process.
目次
What is AGV? Explaining the 5 types
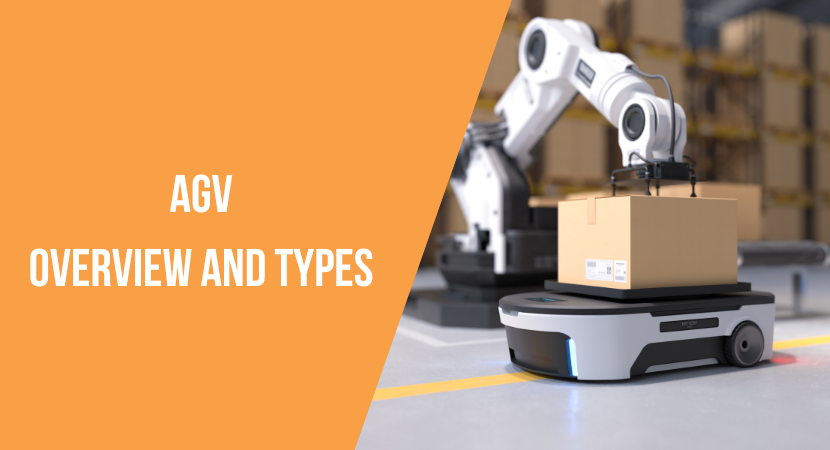
An Automated Guided Vehicle (AGV) is a self-operating, unmanned vehicle designed for quick and easy material transportation within industrial settings such as factories and warehouses.
These vehicles are great at moving products and materials swiftly and precisely from one point to another, enhancing operational workflows.
AGVs operate on a range of principles, ranging from systems guided by magnetic tape or RFID tags embedded in the floor to advanced technologies that enable these vehicles to autonomously navigate by recognizing their surroundings.
There are five types of AGV:
- Loading type AGV: Loading cargo on top
[When transporting cargo of various sizes and shapes] - Low-floor AGV: Very low height
[For manufacturing parts of machinery and electronic equipment, medicines, etc.] - Towing type AGV: Pulling other carts or trailers
[If there is enough aisle space] - Flat body/heavyweight AGV: Capable of weighing over 800kg
[When transporting products that are too heavy for other AGVs] li> - Special type AGV: Specialized for specific work such as forklift type or conveyor type
[When a special order is required that cannot be handled by other AGVs]
Loading type AGV
As the name suggests, a loadable AGV is a type of AGV that has the feature of being able to load goods on top.Due to its flexibility, this type of AGV can transport goods of various shapes and sizes, and can be used in a wide range of situations, including inside factories, warehouses, and even research facilities and hospitals.
Its biggest appeal is its flexibility. It can carry items of various shapes and sizes, and has a large loading space that allows it to carry many items at once. This feature is a huge advantage in modern production sites where efficient logistics operations are required.
The sizes of the mainstream AGVs are as follows.
- Length approximately 1,000mm to 2,500mm
- Width is approximately 600mm to 1,200mm
- Height is about 300mm to 700mm
AGVs in this range can transport objects of the following sizes and weights:
- Size: Approximately 600mm x 600mm x 600mm to 1,500mm x 1,200mm x 1,200mm
- Weight: 100kg~1,500kg
Additionally, a margin of around 300mm to 500mm is required to run the AGV safely.
Automated Guided Vehicles, or AGVs for short, are real game-changers when it comes to moving stuff around in places like factories, warehouses, and even hospitals. Imagine having a smart helper that can carry products and parts from one spot to another in a factory, or help out with the heavy lifting and sorting in warehouses and distribution centers.
Not just in manufacturing, these versatile vehicles are also making life easier in hospitals by transporting medicines and medical equipment right where they’re needed.
Low floor AGV
As the name suggests, low-floor AGVs are a type of AGV with a much lower height than other AGVs.The biggest feature of low-floor AGVs is their low height. This allows it to pass through spaces with limited height or under other machinery or equipment. Additionally, some low-floor AGVs have load lifting capabilities, making loading and unloading operations even easier.
Generally, the sizes of low-floor AGVs are as follows:
- Length: 800mm~2,000mm
- Width: 500mm~1,000mm
- Height: 100mm~200mm
This size can be very advantageous in certain environments and tasks.
For safe operation, it is necessary to have a margin of 200 mm to 400 mm in addition to the width of the AGV.
The size of objects that a low-floor AGV can transport depends on the loading space, but generally falls within the following range.
- Size: 500mm x 500mm x 500mm to 1,200mm x 1,000mm x 1,000mm
- Weight: 50kg~700kg
The following are situations in which low-floor AGVs are especially useful.
- Inside the factory: Transporting products and parts, especially in areas with tight spaces or height restrictions
- Car manufacturing: Parts transport on car assembly line
- Electronic assembly: transporting parts in tight spaces
- Pharmaceutical factories: Transportation of raw materials and products in limited space
- Automated warehouse: loading and unloading products in areas with height restrictions
Towed AGV
A towable AGV is a type of AGV that has the ability to pull other carts or trailers.The biggest advantage of towed Automated Guided Vehicles (AGVs) is in their capacity to move large volumes of goods and products simultaneously. Their adaptability especially shines through with the ability to modify the number and type of trailers and carts attached, providing an immediate response to constantly changing transport requirements.
This capability not only allows for the transportation of substantial cargo loads in one go but also significantly enhances transport efficiency, streamlining operations across the board.
Generally, the sizes of towed AGVs are as follows:
- Length: 1,500mm~3,000mm
- Width: 800mm~1,500mm
- Height: 300mm~700mm
The size and weight of objects that can be carried by a towed AGV depends on the size and design of the trailer or cart to which it is connected. Generally, the range is as follows.
- Size: 2,000mm x 1,500mm x 1,500mm to 5,000mm x 2,500mm x 2,500mm
- Weight: 500kg to 2,000kg
In particular, it is particularly suitable for use in the following situations:
- Large factories: Transportation of parts and products between production lines
- Logistics center: Input/output and movement of large quantities of products
- Airport: transporting baggage and airplane parts
- Hospitals: transporting large quantities of medicines and patient meals
- Manufacturing industry: Supplying parts and transporting products on production lines
Flat body/heavyweight AGV
A flat body/heavyweight AGV is a type of AGV specifically designed for transporting heavy loads and products.This kind of AGV stands out for its remarkable carrying capacity, outperforming other AGVs when it comes to handling hefty goods.
Its flat body design not only ensures enhanced stability during transport but also offers the flexibility to accommodate items of different shapes and sizes, making it a very good solution for various industrial needs.
Following are the mainstream sizes of flat-body, heavy-duty AGVs.
- Length: 2,500mm~4,000mm
- Width: 1,500mm~2,500m
- Height: 300mm~600mm
It is suggested to have a margin of 500mm to 1,000mm in addition to the width of the AGV.
Flat-body, heavy-duty AGVs are especially suitable for use in the following situations:
- Steel industry: Transporting heavy steel materials
- Automobile manufacturing: Transportation of heavy parts such as car frames and engines
- Aircraft manufacturing: moving large parts and materials
- Port facilities: movement of containers and large cargo
- Energy industry: Transporting heavy equipment and components
Special type AGV (conveyor type, forklift type, etc.)
Special type AGVs (conveyor type, forklift type, etc.) are a type of AGVs that have specialized functions for specific tasks and tasks.The most important feature of this type of AGV is its purpose-built design and functionality. For example, a conveyor-type AGV has a conveyor function that allows automatic loading and unloading of goods.
On the other hand, forklift-type AGVs are equipped with forks for lifting and moving goods. Its advanced automation capabilities provide increased efficiency and minimal human resources.
Examples of specialized AGVs include those used for the following purposes:
- Production line: Conveyor type AGV is used for automatic supply and transportation of parts on the production line
- Warehouse: Forklift-type AGVs are ideal for retrieving items from high shelves and transporting heavy items
- Automotive assembly: Effective for transporting and installing parts
- Electronic component manufacturing: Ideal for transporting and placing delicate parts
- Logistics center: Transportation and sorting of large amounts of cargo and products
So far, we have explained the types of AGVs based on their transport methods. AGV is a guided vehicle that moves automatically, and there are three types of movement methods.
In the following sections, we will specifically explain three movement methods for moving AGVs.
Three guidance methods of AGV
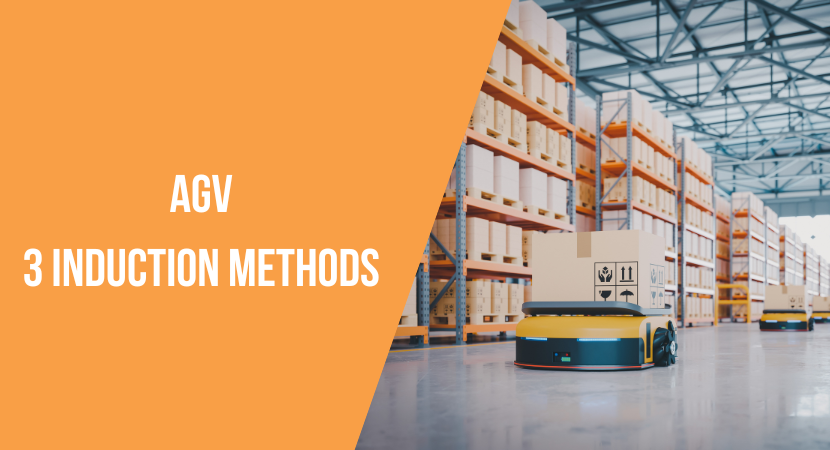
There are various types of AGVs, and it is necessary to choose the best one according to each business and situation.
Below, we will explain in detail the characteristics and usage scenarios of the three main types of AGV.
- Route Guidance Type
[When stable movement with a constant flow line is required] - Autonomous Mobile Type
[When there are many obstacles and flexible movement in real time is required] - Following Type
[When assuming work that involves moving with people]
Route Guidance Type
Path-guided AGVs use physical guidelines, such as magnetic tape or wires on the floor, to navigate a precise path. As a result, while maintaining a high degree of stability, it is possible to reliably transport work over a fixed route over and over again.The biggest attractiveness is its stability and simplicity. Path-guided AGVs are extremely reliable for continuous transport operations due to the low risk of signal loss and errors.
Additionally, new routes can be added or changed simply by changing the guidelines.
However, on the other hand, there are also constraints in terms of flexibility. Changing the guidelines will require new installations or changes to existing guidelines, and any associated floor refurbishment work must be taken into account.
Route-guided AGVs are increasingly being introduced in situations where vehicles need to regularly travel on a fixed route, such as the following:
- Mass production factories and distribution centers
- Pharmaceutical factories, etc.
Autonomous Mobile
An autonomous mobile AGV is an advanced automated transportation system that uses proprietary sensing technology to select and move on the optimal route based on its own judgment.This type of AGV uses advanced sensing technologies such as laser radar, cameras, and ultrasonic sensors to provide real-time situational awareness. This makes it possible to drive while flexibly responding to changes in the environment without physical guidelines.
The biggest attractiveness is its high flexibility and obstacle avoidance ability. Because it does not rely on physical guidelines, it can quickly respond to sudden route changes and environmental changes. It is also possible to detect dynamic obstacles, such as people or other vehicles, in real time and avoid them appropriately.
However, on the other hand, it also requires advanced technology and cost. Since advanced sensing and control technologies are required, a certain amount of initial investment and technical knowledge are essential for introduction.
Autonomous mobile AGVs are being introduced in a wide variety of situations where flexible and quick transportation is required, such as the following.
- Large distribution center
- Intermediate transportation in the manufacturing process
- Transportation within hospitals and facilities
Following Type
Tracking AGVs use sensor technology to track the operator’s movements in real time and quickly move with them. This way, when the operator moves to the destination, the AGV will follow the same route accordingly.Its biggest appeal is its simplicity and flexibility. A major advantage is that it automatically responds to operator movements and requires no special operations or programming.
Additionally, it does not require a fixed route and responds immediately to the operator’s movements, allowing for extremely flexible operations.
However, on the other hand, it also comes with certain constraints as it needs to move according to the speed and movement of the operator. Especially in situations where multiple operators or AGVs are present, it can be difficult to identify what to follow and take appropriate action.
Tracking type AGVs are being introduced in situations where it is required to quickly respond to operator movements, such as the following.
- Picking work in the warehouse
- Transportation of patients and medicines within the hospital
- Parts supply on production line
So far, we have explained the AGV guidance method. There are similar AGV devices, but do you know the differences?
The next section explains these differences. If you are looking for the best transport vehicle for your company, read on to the next section.
What is the difference between AMR and RGV?
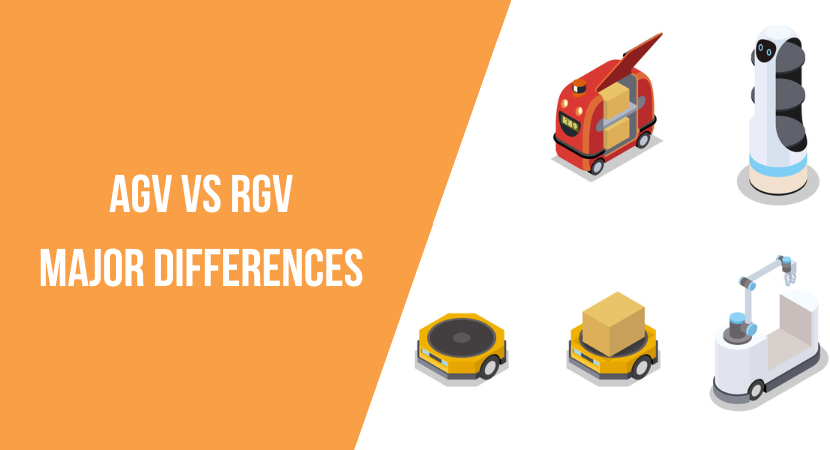
AGV (Automated Guided Vehicle) has been attracting attention as a technology that is central to the promotion of automation in the logistics and manufacturing industries in recent years.
In this section, we will focus on the differences between AGVs and other mobility systems, especially AMRs and RGVs, and explore their characteristics, advantages, and application scenarios in detail.
Differences from AMR
AMR is an abbreviation for Autonomous Mobile Robot, which is a robot designed and developed to automatically avoid people and obstacles.Unlike AGVs, AMRs have a high degree of autonomy. It recognizes the environment in real time and autonomously calculates and navigates the optimal route.
This allows it to automatically avoid obstacles and quickly adapt to changes in the environment. AMR is not bound by physical guidelines and can flexibly respond to changes in the environment.
The biggest difference between AMR and AGV is how the travel route is determined. While AMR is able to autonomously determine the optimal travel route, AGV’s travel route is determined by physical guidelines such as magnetic tape and wires laid out in advance.
On the other hand, AGVs have the advantage of low initial investment and are suitable for automating simple tasks. AMR requires advanced technology and sensors, so higher costs must also be taken into consideration.
Differences from RGV
RGV is an abbreviation for Rail Guided Vehicle, which refers to a shuttle-type robot or transport vehicle that runs on rails or tracks. (Source: Wikipedia)RGV is characterized by movement along a fixed route. RGV moves at high speed on installed rails. This provides highly reproducible and predictable behavior.
Its simple design makes it suitable for use in mass production lines that repeat certain movements or distribution centers that repeatedly move along a specific route.
AGV does not require rails and can freely set routes using tape, magnetism, and sensors. Therefore, it is extremely suitable for use in environments with frequent changes, such as production line layouts that change frequently or transportation work for short-term projects.
Industry Applications
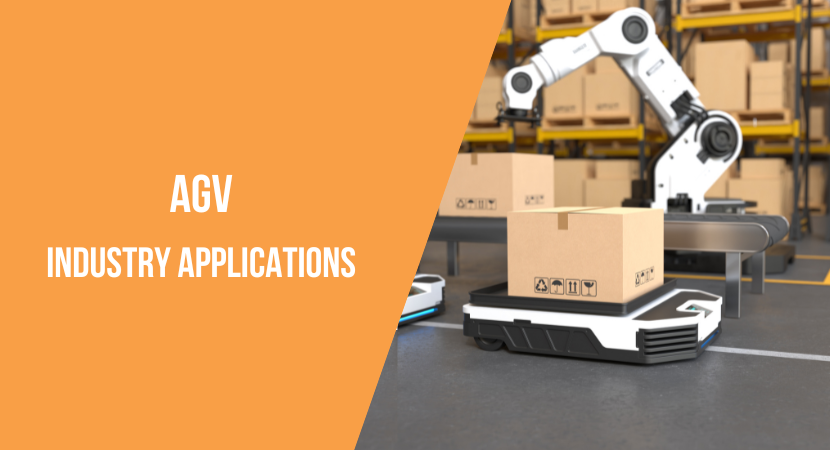
AGVs (Automated Guided Vehicle) are capable of meeting these rapidly evolving demands. Its influence is particuarly visible in the following industries.
- Logistics Industry (Warehouse)
- Manufacturing Industry (Factories/Warehouses)
- Hospitals
Logistics Industry
In the logistics industry, especially in warehousing operations, the demand for AGVs has increased with the spread of online shopping and expansion of e-commerce in recent years.Forklift-type AGVs are ideal for loading, unloading, and moving cargo, and load-bearing, flat-body, and heavy-duty AGVs each efficiently transport everything from small loads to large products.
Additionally, the movement of AGVs is controlled by various transport methods such as magnetic tape, lasers, and vision guides.
By introducing AGV, it is possible to improve efficiency, improve productivity, ensure worker safety, and reduce operating costs. Therefore, it is necessary to select the most suitable AGV according to the layout and size of the warehouse and the amount of cargo handled.
Manufacturing Industry
Various types of AGVs are used in the manufacturing industry.Forklift-type AGVs are suitable for handling parts and products, efficiently loading and unloading products and parts and moving them between production lines.
On the other hand, towed AGVs have the ability to transport large quantities of parts and materials at once, supporting the smooth progress of the manufacturing process. Conveyor-type AGVs can automatically supply parts to production lines and transport finished products.
Introducing AGV in the manufacturing industry can not only reduce production costs, but also shorten lead times, improve manufacturing quality, and ensure production line flexibility.
Hospitals
AGVs are also used in hospitals. Meal cart-type AGVs support the efficient provision of meals to patients and the appropriate disposal of medical waste and general waste.Furthermore, AGVs for transporting pharmaceuticals and samples, which are responsible for transporting pharmaceuticals and specimen samples, can be transported quickly and safely within hospitals.
Introducing AGVs in hospitals will improve work efficiency, ensure worker safety, and reduce the risk of infectious diseases.
It greatly contributes to improving the quality of medical services by improving patient satisfaction and reducing the burden on staff.
Up to this point, we have explained specific situations in which AGVs are used. In the next chapter, we will explain the benefits of introducing AGV and the points to keep in mind.
If you want to minimize the risks of your deployment, read on to the next section.
Advantages and disadvantages of Automated Guided Vehicles AGV
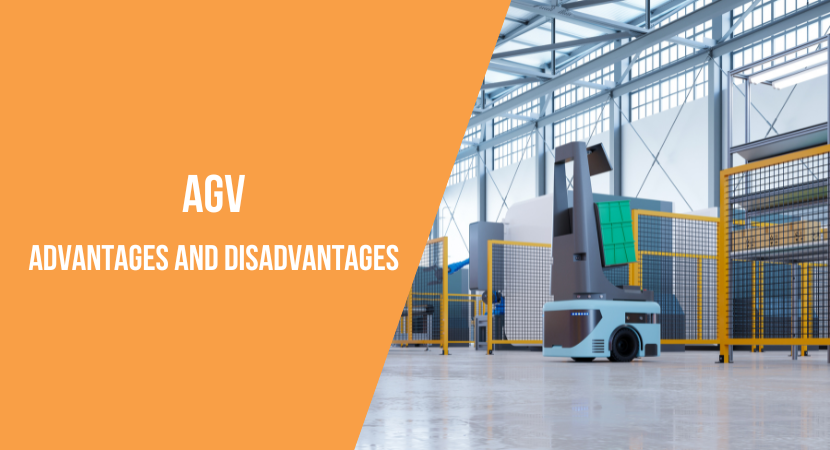
AGVs (automated guided vehicles) are convenient, but each has its advantages and disadvantages depending on the usage situation and purpose.
Advantages
There are three benefits of introducing AGVs (automated guided vehicles):- 24-hour Operation
- Improves Safety
- Efficiency
24-hour Operation
A major feature of AGVs is that they can automatically transport objects all day long without any breaks. This is expected to dramatically improve productivity and alleviate the labor shortage problem that has become increasingly serious in recent years.As long as the power supply continues, the AGV can perform its tasks continuously. AGVs can work with the same efficiency, especially during times when there is little human activity, such as at night or early in the morning.
For example, at e-commerce distribution centers, there are times when the number of orders increases rapidly, such as during sale periods and the year-end and New Year holidays. By effectively utilizing AGVs during busy periods like this, you can quickly pick and ship products.
Additionally, by using AGVs to organize and move products at night, it is possible to improve the efficiency of daytime work.
Improves Safety
AGVs are equipped with sensors and camera systems that make full use of cutting-edge technology, which significantly improves the safety of work sites.Traditionally, manual transportation work has always been associated with the risk of accidents due to human fatigue and errors in judgment.
However, technological advances in AGVs have made it possible to perform advanced transportation tasks such as real-time obstacle detection and automatic route changes. This significantly reduces the possibility of accidents due to human error.
For example, imagine a large factory or warehouse. With large numbers of workers and machines working in tight spaces, AGVs constantly monitor their surroundings using sensors and cameras. This prevents collisions with other equipment or workers and ensures safe transport.
The introduction of AGVs not only dramatically improves workplace safety, but also brings significant benefits in reducing costs and downtime due to accidents and breakdowns.
Efficiency
A key feature of AGVs is their ability to perform repetitive tasks with consistency and accuracy. This makes it possible to improve work efficiency and reduce errors caused by human error.In the past, when work was done by humans, there were times when mistakes were unavoidable due to fatigue or temporary inattention. This risk is especially high during busy periods and when working at night.
However, computer control allows AGVs to continue working with consistent quality. This makes it possible to improve work efficiency while maintaining uniform quality.
At major e-commerce distribution centers, during peak order periods, there may be work to pick and ship products that cannot be handled manually.
Even under these conditions, AGVs accurately pick up goods and transport them to the appropriate shipping destination. Shipping errors and delays can be significantly reduced, contributing to improved customer satisfaction.
By introducing AGV, it is possible to significantly reduce the problems of labor shortages and human errors while simultaneously maintaining smooth operation and high quality.
Disadvantages
The following disadvantages can be considered by introducing AGV (automated guided vehicle), so please be careful.- High initial investment
- Requires specialized technician
- Difficulties in coordinating with people
High initial investment
While AGVs certainly contribute to improved productivity and efficiency, they require a high initial investment.The initial investment involves a wide range of costs, including not only the cost of the machine, but also the surrounding environment, system maintenance, and employee training.
Such initial costs can be a major business risk, especially for small and medium-sized businesses with tight cash flow.
Unlike large companies, small and medium-sized companies are required to operate with limited funds, and the high cost of introducing AGVs is a serious decision.
If trouble or unexpected costs occur after implementation, the impact is likely to affect the entire business.
When considering the introduction of AGV, it is necessary to carefully evaluate the initial investment, future returns, and associated risks, and to develop a plan that balances management stability and efficiency.
Requires specialized technician
When implementing Automated Guided Vehicles (AGVs), it’s crucial to prepare a team capable of maintaining and operating these systems, which might initially seem like a challenge for businesses.AGVs offer the advantage of round-the-clock operation and precision in tasks, yet their sophisticated technology demands specific expertise for regular upkeep and to address any issues that may arise.
Without readily available engineers to provide support, leveraging the full capabilities of AGVs can become challenging.
Especially in scenarios like e-commerce distribution centers, where AGVs play a vital role during peak periods with surges in orders, ensuring their uninterrupted operation is essential.
Should an AGV encounter an issue, having an in-house specialist engineer ready to swiftly troubleshoot is invaluable, as relying on external assistance may not be the most practical solution.
As such, when considering the integration of AGVs into your operations, it’s important to recognize the necessity of not just investing in the technology but also in training personnel who are skilled in managing and operating AGVs effectively.
Challenges in human-machine co-operation
Adopting Automated Guided Vehicles (AGVs) in warehouses and factories signifies a shift in operations, which may initially lead to adjustment challenges among employees as they attempt to adjust to the new workforce support.In high-demand environments like e-commerce distribution centers, AGVs play a pivotal role in moving products efficiently. Meanwhile, employees tasked with different responsibilities must develop a thorough understanding of both their roles and the AGVs’ operational parameters.
To bridge this gap, ongoing training and education are crucial. Familiarizing staff with AGV movements and sensor responses is key to gorwing a productive relationship between humans and machines.
As teams become more accustomed to working alongside AGVs, the true potential of these automated helpers can be unleashed. Remember to continuously refine and optimize your company’s workflow to support automated transport effectively, ensuring that AGVs integrate smoothly into your operation.
We’ve discussed the pros and cons of integrating AGVs into your business. Next, we’ll explore seven critical considerations to help you select the ideal AGV for your company’s needs.
If you want to implement the most suitable AGV for your company and achieve maximum operational efficiency, read on.
Choosing the best Automated Guided Vehicle (AGV)
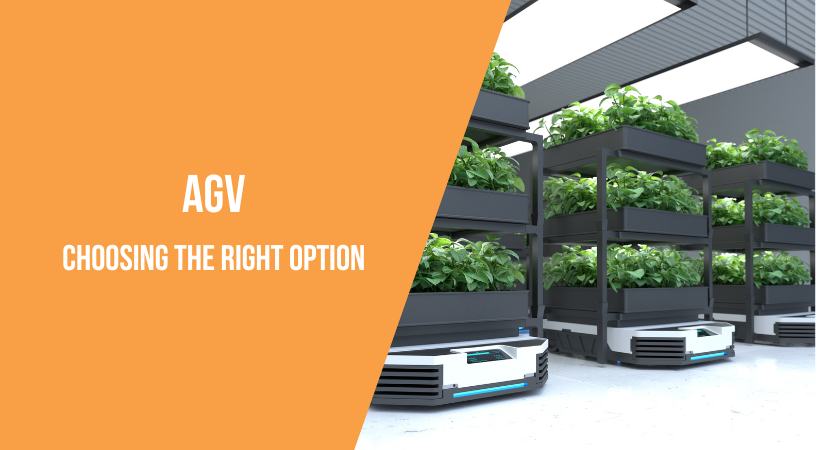
AGVs come in various types and guidance methods. As an investor, it is important for you to make your decision after thoroughly considering all the necessary ceiteria to ensure you have the best AGV for your business and its specific needs.
Consider the following seven points and choose the AGV that is most suitable for your company.
- Size and weight of the product to be transported
- Layout and size of the place of use (factory, warehouse, etc.)
- Operating time and charging time
- Software ease of use and customizability
- Safety
- After-sales service/maintenance support
- Implementation cost
Size and weight of the product to be transported
When considering the introduction of AGVs (automated guided vehicles), important points are not only their performance and functions, but also the size and weight of the products being transported. Whether a particular AGV can properly carry a product depends on the type and design of the AGV.First, select the type of AGV according to the size of the product/cargo you are trying to transport.
Size of object | Available weight | Required aisle width | |
---|---|---|---|
Loading type AGV | 600mm×600mm×600mm From 1,500mm×1,200mm×1,200mm Approx. |
100kg to 1,500kg | AGV width + Approximately 300mm to 500mm |
Low floor AGV | 500mm×500mm×500mm From 1,200mm×1,000mm×1,000mm Approx. |
50kg to 700kg | AGV width + Approximately 200mm to 400mm |
Towed AGV | 2,000mm×1,500mm×1,500mm From 5,000mm×2,500mm×2,500mm Approx. |
500kg to 2,000kg | AGV width + Approximately 300mm to 500mm |
Factory layout and size
When selecting an AGV, it is necessary to select it according to the size and layout of the factory itself.For example, even if a large AGV is introduced into a small factory, the necessary maneuverability will not be effective, and depending on the layout, the operational burden will increase.
As a guide, we recommend selecting an AGV based on the following.
AGV type selection based on factory area
- If the factory area is 10,000 m2 or more: The appropriate AGV type is a flat body/heavyweight type or a special type.
- If the factory area is 2,000m2 to 10,000m2: Loading type or towed type is best
- If the factory area is less than 2,000 m2: Low-floor type is best
AGV type selection based on factory area
- Linear layout: Mainly suitable for loading type and low-floor type, route guidance type is best
- U-shaped layout: Trailed type or low-floor type is suitable, follow-up type is recommended
- Cellular layout: flat body/heavyweight type is best, autonomous mobile type is better
- Modular layout: Special types (conveyor type, forklift type, etc.) are suitable, route guidance type is recommended
Operating time and charging time
When selecting an AGV, it is necessary to deeply consider not only transport capacity and speed, but also battery-related factors such as operating time and charging time. The reasons for this can be broadly summarized into the following three reasons.- Possibility of continuous operation: No need to worry about charging due to AGV battery performance assuming peak times
- Charging failures and downtime: Stay productive with short charging times
- Power cost optimization: efficient and cost-effective operation
In order to operate AGVs efficiently, it is necessary to clarify whether 24-hour operation is required or whether operations need to be done in shifts.
For example, load-bearing, flat-body, and heavy-duty AGVs are characterized by their long duration. Therefore, it is recommended to consider it as an option when considering long-term operation.
Software ease of use and customizability
AGVs that are equipped with easy-to-use software or that can be customized are often easy to use for users in any industry and have high operational efficiency.When the software is easy to use, the operation of the AGV itself is intuitive, minimizing training time and reducing operational errors.
As a result, in the manufacturing industry, it is possible to reduce production line stoppages and quality control errors due to software defects and operational errors.
For example, the negative effects of low flexibility can be avoided, such as delays in introducing new products to production lines in the manufacturing industry, difficulties in introducing new delivery routes in the logistics industry, and delays in introducing new treatments in hospitals. Masu.
Installing software is expensive, so it is necessary to select the AGV that best provides the flexibility your company requires after satisfying both the purpose and budget.
Safety
Safety when selecting AGVs has a great deal to do with prevention of accidents and reducing work risk in factories in a wide variety of fields, from manufacturing to logistics to medical care.AGVs are highly safe and can coexist smoothly with other machines and people, preventing accidents in a variety of situations.
Safety features associated with AGVs include:
- Highly sensitive sensor
- Emergency stop button
- Speed control function
- Warning sounds and lights
Such AGVs can cause collisions with workers and halt production lines in the manufacturing industry, damage to packages and delivery delays in the logistics industry, and accidents involving patients and This increases the risk of collisions with medical staff and damage to medical equipment.
In this way, the safety of AGVs is a factor that supports the expansion of their use in various fields due to their high functionality and safety. Appropriate AGV selection is essential to perform work efficiently and safely.
After-sales service/maintenance support
When choosing an AGV, after-sales service and maintenance support are necessary perspectives as a long-term investment.AGV is an expensive piece of equipment, so to minimize the risk of trouble or failure, regular maintenance and quick troubleshooting is essential.
AGV provides extensive after-sales service and maintenance support, and can efficiently and safely carry out a wide variety of tasks, including regular inspections and maintenance, 24-hour support, prompt parts supply, software updates, and on-site training.
On the other hand, While AGVs with minimal support have cost benefits, they also come with risks such as limited support time, delay in replacement parts, and lack of software updates.
Care must be taken as this can have a significant impact on business efficiency and quality, such as production stoppages in the manufacturing industry, delivery delays in the logistics industry, and delays in the supply of medical equipment in hospitals.
In this way, AGV after-sales service and maintenance support is an important element for realizing operational efficiency and quality improvement, as it combines high functionality and safety. By receiving appropriate support, you can expect stable operation over the long term.
Implementation cost
When introducing AGV, it is necessary to consider not only the immediate implementation cost but also the long-term ROI (return on investment).This is because not only the introduction of machines that exceed the budget, but also the introduction of AGVs that cannot achieve the purpose as a result of cost cutting, will end up being a waste of money.
For example, if a factory in the manufacturing industry could automatically transport things, there would be no problem, but adding an unnecessary lifting device would result in unnecessary expenses.
Additionally, in the logistics industry, as a result of introducing cheap AGVs, due to their low performance, they are unable to handle the volume of cargo at peak times, which can actually increase labor costs.
The important thing is to introduce AGVs by considering the balance between high functionality and cost performance
So far, we have introduced how to choose the most suitable AGV. In the next chapter, we will introduce some recommended manufacturers and compare them.
If you want to choose the best AGV for your factory or warehouse, read on to the next section.
Manufacturer Comparison Automated Guided Vehicle (AGV) [2023 Data]
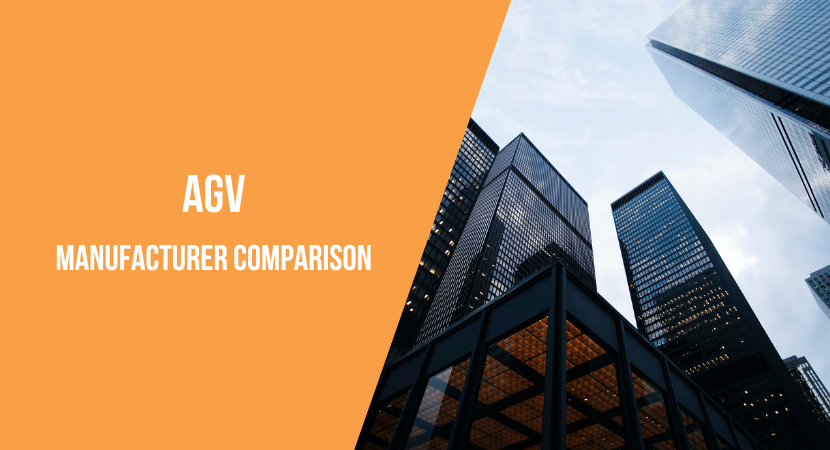
The following five companies are major manufacturers of AGVs. Compare them and find the manufacturer that produces the best machine for your company.
- Daifuku
- Elemex
- Sugiyasu
- Meidensha
- Ricoh
Daifuku | Elemex | Sugiyasu | Meidensha | Ricoh | |
---|---|---|---|---|---|
Loading type | – | ✓ | – | ✓ | ✓ |
Low floor type | – | ✓ | – | ✓ | – |
Traction type | – | ✓ | – | – | – |
Flat body/heavyweight type | – | ✓ | – | – | – |
Special types Forklift type, Conveyor type, etc. |
✓ | ✓ | ✓ | ✓ | – |
Route guidance type | – | ✓ | ✓ | ✓ | – |
Autonomous mobile | ✓ | ✓ | – | ✓ | – |
Following type | – | ✓ | ✓ | ✓ | – |
If you would like to learn more about each company’s products and technologies, please contact us using the button below.
Contact JET Global
Daifuku
Founded in 1937 and headquartered in Osaka, Daifuku has evolved into a global leader in providing cutting-edge technology and services.Their journey with Automated Guided Vehicles began in 1972, culminating in the launch of the industry’s pioneering AGV in 1975.
Daifuku’s expertise is built on three foundational technologies: adaptable control systems for various environments, precise transportation technology, and designs that ensure easy maintenance. Consequently, Daifuku’s AGVs have achieved the highest market share, making a significant impact across numerous industries.
Daifuku’s AGVis an innovative omnidirectional Automated Guided Vehicle capable of navigating complex paths, designed to meet the versatile needs and environments of our clients.
Their Automated Guided Vehicles find applications in a broad spectrum of industries, from manufacturing and logistics to healthcare.
Elemex
Established in 1980, Elemex has earned recognition as an expert in electrical equipment construction, operating from Ota City, Gunma Prefecture. Their specialty lies in designing, manufacturing, and constructing automation systems, including space-efficient Automated Guided Vehicles suitable for smaller facilities.Their focus on AGV innovation began in 1993, aiming to make them accessible for not only large but also small to medium-sized enterprises.
In 1997, Elemex introduced a compact, laser-guided Automated Guided Vehicle, expanding our portfolio to include various AGV models guided by magnetic tape and wire markers.
Elemex is known for its diverse range of AGVs, from load carriers to aerial platforms and specialized transport vehicles, catering to a multitude of logistics needs.
Sugiyasu
Since 1937, Sugiyasu has been a prominent name in logistics equipment, based in Takahama City, Aichi Prefecture. Their advanced technology and services, including Automated Guided Vehicles, have significantly contributed to logistics efficiency and labor savings globally.Their venture into AGV development began in 1985, with their first product hitting the market in 1991.
Sugiyasu’s forklift-type AGVs are designed to meet diverse logistics requirements, enhancing operations such as material handling and load management.
Meidensha
Meidensha, founded in 1924, has established itself in the electrical equipment industry, with headquarters in Shinagawa-ku, Tokyo. Their portfolio, centered on Automated Guided Vehicles, plays a vital role in the logistics sector by improving efficiency and reducing labor costs.Meidensha embarked on AGV development in 1985, launching their inaugural product in 1990.
Meidensha offers a versatile range of AGV models, including trolley, forklift, and custom-designed types, to fit various applications and environments.
Ricoh
Ricoh, since its launch in 1936, has been a pioneer in the information and industrial equipment sectors, with a global network based in Ota-ku, Tokyo. Their contributions to logistics, through the development and sale of Automated Guided Vehicles and other electrical equipment, have set new standards in efficiency and labor savings.Entering the AGV market in 1995, Ricoh quickly launched its first model in 1998.
Ricoh’s Automated Guided Vehicles include innovative models like bogie and forklift types, as well as specialized AGVs, all designed to simplify adoption and enhance operational efficiency.
Looking to invest in your own AGV? Reach out to us!
Are you wondering which company would be best suited for your own unqiue needs? Are you choosing the right model? Please feel free to contact us if you have any concerns.We will consult on each product and company with you and suggest the machine that best suits your purpose.
Contact JET Global