- Degradation of quality: Burrs affect product appearance and function, diminishing overall quality.
- Safety Issues: Sharp burrs pose injury risks to handlers.
- Difficulties in assembly: Parts with burrs can be challenging to assemble, increasing assembly time.
- Motion problems: Burrs on machine moving parts can hinder smoothness and precision of motion.
To address these issues, it would be beneficial to use a deburring machine.
In today’s article, we will be introducing you to various types of deburring machines. We will also help you learn how to choose the best one for your company, and look over some of the prominent deburring machine manufacturers.
目次
What is a Deburring Machine?
A deburring machine removes burrs and dross from sheet metal product edges.These tools are used across multiple industries to smooth out burrs from machined material.Deburring machines use a variety of brushes, belt heads, discs and more attachments for grinding burrs out of workpieces.(Source: Nikkan Kogyo Shimbun/)
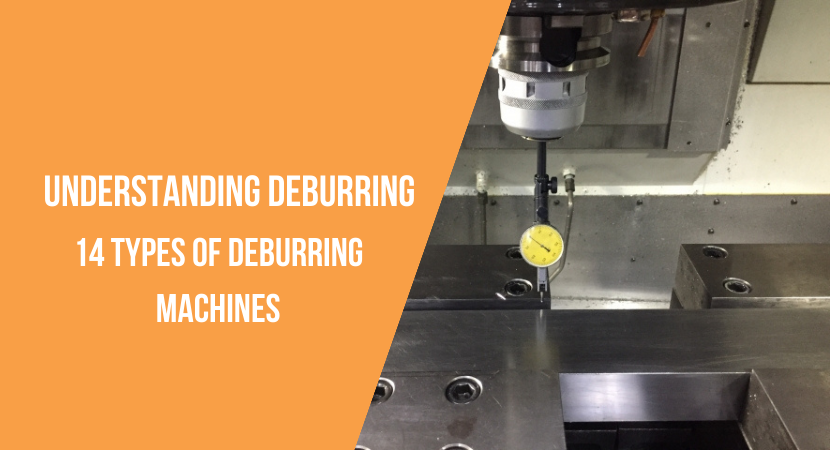
Here are 14 types of deburring machines:
- Brush type deburring machine
- Roller type deburring machine
- Multi-axis robotic deburring machine
- Belt sander type deburring machine
- Disc sander type deburring machine
- Tumbler type deburring machine
- Vibration type deburring machine
- Air blast deburring machine
- Laser deburring machine
- Wet blast machine
- Water jet deburring machine
- Chemical deburring machine
- Electrolytic deburring machine
- Small tabletop deburring machine
Brush Type Deburring Machine
A brush deburring machine uses rotating brushes to remove burrs from metal and other materials, offering flexibility on irregular shapes and complex surfaces.Features include:
- Flexible processing: Effective deburring on irregular shapes and complex surfaces.
- Surface protection: Low risk of damaging workpiece surfaces.
- Material compatibility: Suitable for a wide range of materials, including metal and plastic.
These machines excel at deburring metals (aluminum, steel, etc.) and plastics, making them ideal for small to medium burrs.
They are commonly used for:
- Deburring precision parts: Delicate surface treatment of electronic and precision mechanical parts.
- Pre-treatment for surface treatment: Deburring and smoothing surfaces before applying treatments like painting or plating.
- General metal processing: Deburring metal processing parts in industries such as automobiles and construction machinery.
Brush deburring machines are particularly valuable when surface quality and appearance are crucial, showcasing flexibility across various materials and shapes.
Roller Type Deburring Machine
A roller deburring machine utilizes rotating rollers to effectively remove burrs from metal and other materials, making surfaces uniform.Key features include:
- Uniform processing: Rollers apply constant pressure, ensuring consistent quality deburring.
- Surface protection: Low risk of damaging the workpiece surface.
- Applicable to a variety of materials: Suitable for metals (steel, aluminum, etc.), plastics, and wood.
- Not suitable for very large or ultra-fine burrs.
Common uses for roller deburring machines:
- Deburring large metal panels: Ideal for automobile body parts and building materials.
- Deburring flat parts: Effective for parts with large flat surfaces.
- Efficient deburring of mass-produced parts: Suitable for high-volume production.
Roller deburring machines are highly sought after in large-scale manufacturing, automotive, and the production of large mechanical parts due to their consistent quality and efficiency.
Multi-Axis Robotic Deburring Machine
A multi-axis robotic deburring machine, featuring a robotic arm with multiple movable axes, automates precision deburring operations.Key features include:
- High flexibility: Capable of complex operations in 3D space for irregular shapes and difficult angles.
- Precision and Consistency: Programmed movements ensure high precision and consistent quality.
- Improved work efficiency: Automation enables faster and continuous deburring, enhancing production efficiency.
Multi-axis robotic deburring machines handle various materials and excel in deburring large workpieces, parts with complex shapes, and products requiring precise deburring.
Common use cases include:
- Automotive industry: Precision deburring of car engine and body parts.
- Aerospace industry: Deburring complex shapes in aircraft structural and engine parts.
- Precision machinery industry: Deburring small precision parts like medical equipment and electronics.
Due to its high flexibility and precision, multi-axis robotic deburring machines meet the needs of diverse industries, particularly those requiring high-quality standards.
NC Deburring Machine
The NC deburring machine, using precise computer control, automatically removes burrs with high accuracy and uniformity.Key features include:
- Precise control: Achieves high precision through fine adjustments using a computer program.
- Adaptability for complex machining: Efficiently removes complex shapes and fine burrs.
- Applicable to a variety of materials: Suitable for metals, plastics, and composite materials.
NC deburring machines, effective for small and medium-sized parts, find applications in various fields:
- Precision parts processing for electronic equipment: High-precision burr removal for a smooth finish.
- Aerospace industry: Handling complex-shaped parts with high-precision finishes.
- Automotive parts manufacturing: Ensuring consistent quality and efficient production.
Widely used in the manufacturing industry, NC deburring machines are valued for their accuracy, efficiency, and versatility in handling different materials and shapes.
Belt Sander Type Deburring Machine
A belt sander deburring machine utilizes a rotating abrasive belt to efficiently remove burrs from metal and other materials, especially suitable for flat processing.Key features include:
- Efficient flat processing: Ideal for deburring large flat parts.
- Ease of operation: Basic operations are relatively simple, making it accessible to many workers.
- Cost efficiency: Relatively low implementation cost, suitable for small factories and workshops.
Belt sander type deburring machines are effective for flat deburring across various materials such as metal, wood, and plastic. They are particularly useful for deburring parts with large flat surfaces and relatively simple shapes.
Common applications include:
- Metal processing industry: Deburring and surface treatment of metal parts and structures.
- Woodworking: Surface finishing and corner cutting of wooden products.
- Plastic product manufacturing: Deburring and smoothing the surface of plastic parts.
Belt sander deburring machines are valued for their efficiency and flexibility, especially when processing large areas, and their ability to work with a wide range of materials is a major advantage of this machine.
Disc Sander Type Deburring Machine
A disc sander deburring machine employs a rotating disc-shaped abrasive material to remove burrs from metal and other surfaces, particularly effective for deburring and polishing on flat and curved surfaces.Key features include:
- Wide range of surface treatment capacity: Large abrasive surface allows rapid treatment of various surfaces.
- Flexible processing of flat and curved surfaces: Suitable for deburring and polishing on both flat and curved surfaces.
- Easy operability and maintenance: Relatively easy to operate and maintain.
Disc sander type deburring machines can handle various materials and are mainly suitable for removing small to medium burrs.
They find applications in:
- General industry: Deburring and polishing of metal products and plastic parts.
- Woodworking: Surface treatment and polishing of wooden furniture and crafts.
- Maintenance/Repair: Repair and refinishing of various materials.
- Prototyping: Deburring and polishing for small-scale manufacturing and custom parts.
These machines are useful in various industrial fields due to their wide range of surface treatment capabilities and ease of operation. The flexible processing capacity of flat and curved surfaces is a special feature of this machine.
Tumbler Type Deburring Machine
A tumbler type deburring machine processes multiple parts simultaneously, removing burrs through collisions and friction within a rotating drum.Features include:
- Efficiency in mass processing: Suitable for mass production with a large number of parts processed at once.
- Uniform finish: Ensures uniform deburring results and consistent part quality.
- Easy to operate: Simply place parts into the drum and start the machine without detailed settings or operations.
Tumbler type deburring machines can handle various materials like metal, plastic, and rubber, ideal for small to medium-sized parts.
They are widely used in industries such as:
- General industry: Mass deburring and polishing of metal and plastic parts.
- Automotive parts manufacturing: Deburring small parts like screws, bolts, and small metal components.
- Jewelry production: Finishing of small ornaments and accessories.
- Electronic components: Deburring small electronic components and connecting parts.
Tumbler-type deburring machines are highly valued for their high-volume throughput, uniform finish, and ease of operation. They provide efficient and consistent quality results when deburring and polishing small to medium-sized parts.
Vibration Type Deburring Machine
A vibration deburring machine utilizes vibration and impact to remove burrs from metal and other materials. This machine uses vibration to cause media containing deburring abrasives and water to collide with the workpiece, effectively removing burrs.Key features include:
- Uniform processing: Vibration applies equal force to the entire surface of the workpiece, allowing for uniform deburring.
- Delicate processing: Creates a very delicate and smooth finish using abrasive materials.
- Compatible with a wide variety of workpieces: Flexible support for workpieces of different shapes and sizes.
Vibration type deburring machines are suitable for various materials such as small to medium-sized metals, plastics, and ceramics. They are especially effective for removing complex shapes and fine burrs.
Common applications include:
- Finishing of small metal parts: Surface finishing and deburring of precision metal parts.
- Manufacture of ornaments: Finishing of delicate ornaments such as jewelry and accessories.
- Deburring of plastic products: Deburring and surface treatment of small plastic parts and molded products.
Vibration deburring machines are highly valued for their delicate processing ability and flexibility, especially for fine deburring and workpieces with complex shapes. Their ability to work with a wide range of materials is a major advantage of this machine.
Air Blast Deburring Machine
An air blast deburring machine uses high-pressure air to remove burrs and unwanted material from metal and other surfaces.Features include:
- Fast and efficient: High-pressure air blasting effectively removes burrs in a short amount of time.
- Selectable abrasives: Different types of abrasives allow adaptation to various materials and conditions.
- Delicate surface treatment: Delicate surface treatment is possible by adjusting the air blast pressure and type of abrasive.
Air blast deburring machines are suitable for various materials such as metal, plastic, and wood. They are especially effective for small and medium-sized workpieces, and are efficient for removing complex shapes and fine burrs.
Common applications include:
- Deburring metal parts: Deburring auto parts and mechanical parts.
- Surface cleaning: Removal of burrs and scale from the surfaces of castings and forgings.
- Finishing: Finishing work to improve the surface condition of the product.
Airblast deburring machines are highly praised for their high speed, efficient processing ability, and flexibility for delicate processing. They are especially useful for workpieces with precise surface treatments and complex shapes, and their ability to handle a wide range of materials is a significant advantage.
Laser Deburring Machine
A laser deburring machine utilizes a high-precision laser beam to remove burrs from the surface of parts, offering non-contact and highly precise work.Key features include:
- High precision and fine processing ability: Removes fine burrs with exceptional precision.
- Non-contact machining: No physical contact reduces the risk of component damage, making it advantageous for delicate or precision parts.
- Processing speed and efficiency: Fast and efficient, especially for small burrs and complex shapes.
Laser deburring machines handle a wide range of materials compatible with lasers, such as metals, plastics, and composite materials. They are especially suitable for removing very small burrs.
Common applications include:
- Precision parts manufacturing: Deburring precision parts for aerospace, medical equipment, electronic equipment, etc.
- Prototyping: Deburring prototype parts with complex shapes and delicate materials.
- Custom parts manufacturing: Deburring custom parts for special orders and small batch production.
- Research and development: Experimental deburring of new materials and specially processed parts.
Laser deburring machines are highly valued for their high precision and non-contact processing advantages, especially in applications requiring precision work and machining delicate parts. Another great feature is their flexibility in adapting to various materials.
Wet Blast Machine
A wet blast machine sprays a slurry of water and abrasive material at high pressure onto parts to remove burrs and perform surface treatment. This method is effective in smoothing the part surface and removing burrs simultaneously.Key features include:
- Comprehensive surface treatment: Can deburr, clean, smooth, and polish the surface simultaneously, surpassing other dedicated deburring machines.
- Low-temperature processing and environmental friendliness: Uses water to reduce temperature rise and is considered an environmentally friendly processing method.
- High safety: Generates less dust than dry blasting, creating a safer working environment.
Wet blasting machines handle various materials, including metal, plastic, glass, and ceramics. They are suitable for medium to large parts and can process small parts as well. The machine is effective for removing medium to large burrs and performing rough surface treatment.
Common applications include:
- Automotive parts manufacturing: Deburring and surface treatment of auto parts.
- Aerospace industry: Precision deburring and surface finishing of aircraft parts.
- Mold making: Deburring and surface finishing of molds.
- General industrial products: Deburring, cleaning, and smoothing of various industrial products.
Wet blasting machines are particularly useful in applications requiring comprehensive surface treatment and environmental friendliness. Their flexibility in handling a variety of materials and shapes is another major appeal.
Water Jet Deburring Machine
A water jet deburring machine uses a high-pressure water stream, sometimes mixed with an abrasive material, to remove burrs from a workpiece. This technique is also used for cutting, cleaning, or finishing materials using the power of water flow.Key features include:
- Non-contact machining: No physical cutting tools are used, reducing stress and thermal effects on the workpiece.
- Applicability to various materials: Compatible with metals, plastic, ceramics, glass, etc.
- Eco-friendly: Environmentally friendly processing method without chemicals or harmful dust production.
Water jet deburring machines are suitable for various thicknesses, from thin to thick plates, and are especially effective when hard materials, complex shapes, or precision machining are required.
Common applications include:
- Deburring precision parts: Precision deburring of aerospace parts, medical equipment, precision mechanical parts, etc.
- Processing parts with complex shapes: Cutting and processing of parts with complex shapes and fine details.
- Environmentally friendly manufacturing process: Suitable for manufacturing in a clean environment and producing environmentally friendly products.
Waterjet deburring machines are particularly useful in applications requiring environmentally friendly processing methods and flexibility to work with various materials. Their ability to allow precision work through non-contact processing is another major advantage.
Chemical Deburring Machine
A chemical deburring machine uses chemicals to remove burrs by immersing the workpiece in a specific chemical solution. This process dissolves or softens the burrs through a chemical reaction.Key features include:
- Non-contact machining: No physical cutting or polishing, minimizing stress on the workpiece.
- Applicable to complex shapes: Chemical reactions can remove burrs in complex shapes and narrow areas.
- Applicability to delicate materials: Suitable for delicate materials and thin parts that are challenging to mechanically process.
Chemical deburring machines are particularly suitable for materials that react with chemicals, such as metals and plastics. They are effective for machining parts with small burrs and complex shapes.
Common applications include:
- Electronic component manufacturing: Deburring and surface treatment of precision electronic components.
- Manufacturing of medical devices: Manufacturing of medical devices where fine burrs are not tolerated.
- Products with complex shapes: Processing of products that require removal of burrs inside or in narrow areas.
Chemical deburring machines are effective for processing delicate materials and deburring parts with complex shapes. The contactless machining minimizes stress on the workpiece, providing another major advantage.
Electrolytic Deburring Machine
An electrolytic deburring machine uses electrolytic action to remove burrs from metal parts. In this process, the part with the burr acts as an anode, and an electric current is applied in an electrolyte to chemically dissolve the burr. This allows very precise deburring.Key features include:
- High precision and ability to remove fine burrs: Very effective in removing fine burrs that are difficult to address with other physical methods, improving the quality of precision parts.
- Non-contact machining: No physical contact, low risk of damage to the part, suitable for delicate parts and parts with complex shapes.
- Improved surface quality: The electrolytic deburring process can also smooth the surface simultaneously, improving overall surface quality.
Electrolytic deburring machines are particularly suitable for metal parts (particularly conductive materials) and can perform precise deburring regardless of their size, as long as the size fits within the electrolyte container. They are especially effective for removing minute burrs and burrs in challenging positions.
Common applications include:
- Medical equipment: Deburring precision parts such as hypodermic needles and surgical instruments.
- Aerospace industry: Deburring aircraft parts and engine components.
- Automotive parts: Deburring precision engine parts and electronic parts.
- Electronic components: Deburring minute electronic components and connectors.
Electrolytic deburring machines are particularly effective for applications that require high precision and parts with complex shapes. Another major advantage is that they use non-contact processing to minimize damage to parts.
Compact Tabletop Deburring Machine
The compact tabletop deburring machine is a small, tabletop-sized machine optimized for small parts and limited space.Key features include:
- Compact size: Small size and can be installed in limited space.
- Easy to operate: Simple operations, suitable for small work environments and personal use.
- Suitable for precision work: Ideal for small parts and delicate deburring work.
Compact, tabletop deburring machines are generally used for the following purposes and applications:
- Deburring precision parts: Deburring small precision parts such as watches, jewelry, small electronic devices, etc.
- Hobbies and craft processing: Model making, crafts, small DIY projects, etc.
- Laboratory and educational use: Suitable for small-scale prototyping and experimental production in schools and research institutes.
These machines are specialized for use in limited spaces and small-scale work, especially suitable for situations requiring precision deburring or in hobbyist areas.
Advantages and Disadvantages of Deburring Machines
Advantages
Deburring machines offer several advantages:- Specializing in Deburring: Deburring machines are specialized machines for deburring, capable of removing minute burrs and deburring complex shapes.
- Handling a Wide Range of Workpieces: These machines are versatile and can adapt to various applications due to their precision and flexibility.
- Realizing Multiple Deburring Techniques: One machine can perform multiple deburring techniques, providing efficiency and versatility.
Specialized in Deburring
Deburring machines are specialized for deburring, making them very efficient for high-volume production and projects with tight schedules. They reduce the burden on workers, making the working environment safer. Additionally, they can handle special deburring tasks that general-purpose machines cannot.Examples include:
- Deburring extremely small and complex parts such as medical devices and electronic components.
- Deburring parts with curved surfaces and complex internal structures.
- Deburring special materials like high hardness materials, special alloys, and composite materials.
Handling a Wide Range of Workpieces
Deburring machines are sophisticated and adaptable, making them ideal for various applications. They contribute to an efficient production process, an improved working environment, and the ability to support a variety of deburring tasks.Examples include:
- Deburring precision parts like small electronic devices and medical equipment.
- Deburring parts with complex internal structures and curved surfaces.
- Deburring materials that are difficult to handle with regular machines, such as high hardness materials, special alloys, and composite materials.
Industries that benefit from deburring machines include aerospace, medical device manufacturing, precision engineering, electronic component manufacturing, and the automotive industry. In this way, deburring machines contribute significantly to improving production efficiency and quality across various industries.
Ability to Realize Multiple Deburring Techniques with One Machine
There are significant benefits to having a deburring machine that combines multiple deburring methods, including mechanical, chemical, and electrochemical.This results in the following benefits:
- Meet diverse deburring needs: It has the ability to remove various types of burrs efficiently, making the production process more flexible and efficient.
- Improved production efficiency: One machine can handle a wide variety of products and materials, making production lines faster and more efficient.
- Adaptation to special requirements: Can handle special deburring work that is difficult to achieve with general-purpose machines.
The advantages of this type of deburring machine are particularly evident in the following products:
- Composite material products: Products that use different materials, such as a combination of metal and plastic, require deburring methods tailored to each material.
- High-precision medical devices: For medical devices that require precision finishes, not only mechanical methods but also chemical or electrochemical methods are important.
- Aerospace parts: Mechanical methods alone are not sufficient for deburring complex shapes and narrow areas; chemical methods must be used.
In this way, machines that combine multiple deburring methods can greatly contribute to the flexibility of the manufacturing process and increase production efficiency. The effectiveness of these combined methods is particularly evident when dealing with diverse materials and complex products.
Disadvantages
Deburring machines are especially useful for precision parts and processing, but the only disadvantage is that they can only perform deburring operations.Although it has a single function, it requires a large amount of space, so it is necessary to consider introducing it while looking at the situation of the factory. If you don’t have enough space, we recommend considering using a general-purpose machine such as a machining center.
On the other hand, the following are the main cases in which it is recommended to install a deburring machine even if you invest in space and cost.
- Improving the quality of deburring: When manufacturing machine parts that require a high level of safety, such as engines and structural parts for the space industry, aircraft, and automobiles, and medical equipment.
- Improved efficiency of manual deburring: Work speed and efficiency are greatly improved, reducing the burden on workers.
- Achieving high reproducibility: Easier quality control and improved product reliability.
Okay, so now that we are up to speed on the advantages and disadvantages of deburring machines, in the next section, we will explain how to choose a deburring machine.
How to Choose a Deburring Machine
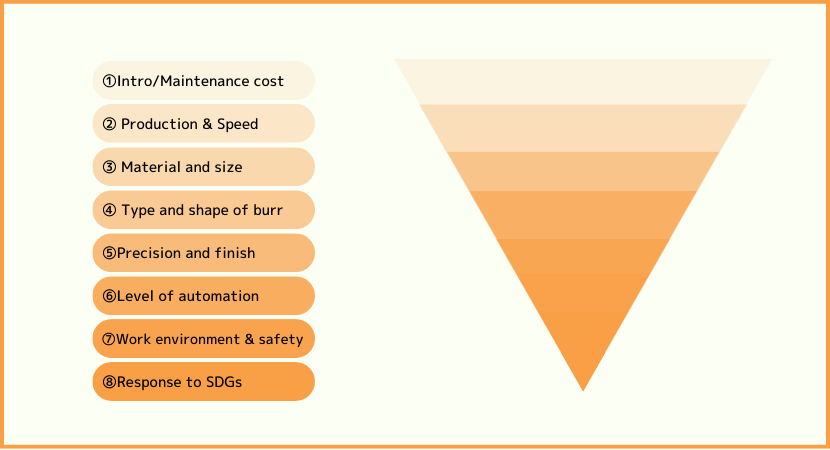
When selecting a deburring machine, you can choose the most suitable one for your company by following the steps below.
- Considering installation costs, maintenance costs, and running costs
- Check production volume and processing speed requirements
- Determine the material and size of the workpiece to be handled
- Identify the type and shape of the burr
- Considering the required deburring precision and finish quality
- Assess the degree of automation and ease of operation
- Consider work environment and safety
- It is possible to deburr in consideration of SDGs.
Consider Installation Cost, Maintenance Cost, and Running Cost
First, you need to check the installation cost, maintenance cost, and running cost that your company can secure.The premise is that the machine must be able to meet the necessary conditions for the purpose. It’s not that it’s better to spend more money, but there’s no point in choosing a cheap machine if you can’t achieve your goals.
First, implementation costs are generally considered in three stages:
- Can you secure a budget exceeding 60 thousand USD?
- Can you secure a budget exceeding 100 thousand USD?
- Can you secure a budget exceeding 130 thousand USD?
Based on these steps, the size and efficiency of the deburring machine that can be secured will be narrowed down.
The next thing to check is maintenance costs and running costs. Maintenance and running costs include the following factors:
- Cost of consumables: Cost required to replace abrasives, blades, brushes, etc.
- Energy consumption: The cost of electricity and other energy sources required to operate the machine.
- Maintenance costs: Costs associated with periodic inspections, parts replacement, and repairs.
- Machine service life: Machine lifespan and associated renewal costs.
- Operator training and labor costs: Operator training and ongoing labor costs.
Maintenance costs vary depending on the machine. Machines that require high upkeep and maintenance costs generally have the following characteristics:
- Advanced technology: Machines that use advanced technology are complex to maintain and require specialized knowledge.
- Complex structures: many moving parts and precise structures
- High energy consumption: low efficiency or large-scale processing requires more energy
For example, the following deburring machines fall under this category:
- Multi-axis robotic deburring machine: advanced technology and complex structure
- Laser deburring machine: requires professional maintenance
- Waterjet deburring machine: high energy consumption and professional maintenance
On the other hand, machines with relatively low upkeep and maintenance costs have the following characteristics:
- Simple structure: Few moving parts, simple structure
- Low energy consumption: Efficient operation and requires less energy
- Standard technology: Uses widely available technology, making it easy to maintain and repair
For example, the following deburring machines fall under this category:
- Belt sander type deburring machine: Simple structure and easy maintenance
- Disc sander type deburring machine: low energy consumption and simple operation
- Tumbler type deburring machine: relatively simple structure and can be operated at low cost
Check Production Volume and Processing Speed Requirements
By understanding the production volumes and processing speeds your company needs, you can get the most benefits at the lowest cost.Deburring machines with high production volume and high processing speed and deburring machines with slow processing speed each have their own advantages and disadvantages.
Let’s compare their advantages and disadvantages in the table below.
High Production, Fast Processing | Low Production, Slow Processing | |
---|---|---|
Advantages |
High efficiency: suitable for mass production, high product volume per hour Cost reduction: Lower manufacturing costs per unit |
Low investment: Machines suitable for small-scale production generally have low costs Flexibility: Easily adaptable to small scale and special production needs |
Disadvantages |
High investment: machines with high production volumes and high processing speeds are expensive Low flexibility: Difficult to change production lines due to specialization of specific tasks |
Low efficiency: Due to low production volume and slow processing speed, it is not suitable for mass production Increased cost per unit: Lower efficiency can increase cost per unit |
Device |
Multi-axis robotic deburring machine General-purpose machines (machining centers, CNC lathes, etc.) Air blast deburring machine |
Tumbler type deburring machine Vibration type deburring machine Chemical deburring machine |
To check the speed of the deburring machine, check the “Maximum Speed” section of the catalog or specifications.
Choose the type and efficiency of the deburring machine after calculating whether each machine meets the necessary conditions for your company’s required production and processing speeds.
Decide the Material and Size of the Workpiece to be Handled
The deburring machine you choose will also depend on the material and size of the workpiece you are handling.First, examples of materials we handle include:
- Metals: Steel, aluminum, copper, brass, stainless steel, etc.
- Plastic: ABS, polycarbonate, PVC, nylon, etc.
- Composite Materials: Carbon fiber, glass fiber reinforced plastic, etc.
- Wood: Various types of wood
- Ceramics: Industrial ceramics, ceramics, etc.
Next, the size of materials is broadly classified into the following three types.
- Small parts: from a few millimeters to a few centimeters. Precise deburring required
- Medium-sized parts: from a few centimeters to tens of centimeters. Various deburring methods can be applied
- Large parts: tens of centimeters or more. Requires large-scale deburring equipment and special equipment
In addition to the weight of the workpiece changing depending on the size, it is also necessary to check the required processing accuracy.
Examples of deburring machine selection based on material and size include:
- Metal (small to medium-sized parts): Multi-axis robot type, general-purpose machine, water jet deburring machine
- Plastic (small to medium-sized parts): Chemical deburring machine, air blast deburring machine
- Composite materials (medium-sized parts): Laser deburring machine, wet blasting machine
- Wood (medium to large parts): Belt sander type, disc sander type deburring machine
- Ceramics (small to medium-sized parts): Electrolytic deburring machine, laser deburring machine
Identify the Type and Shape of Burrs
There are various types of burrs, and it is necessary to select a deburring machine that is compatible with each type.There are the following types of burrs:
- Forming burr: The burr along the seam of the formwork that is generated during the casting or forming process.
- Cutting burr: Fine burr generated on the edge part during cutting process.
- Drilling burr: Burr that occurs at the entrance and exit of a hole during drilling.
- Weld burr: The burr around the weld that remains after the welding process.
- Heat treatment burr: Fine burr generated on the material surface during the heat treatment process.
If you choose an unsuitable deburring machine, the following problems are likely to occur.
- Flash may not be completely removed and product quality may deteriorate
- The product itself may be damaged due to excessive force or inappropriate processing methods.
- The time required for deburring may be longer, reducing overall production efficiency.
- Possibility that rework or additional work is required due to insufficient deburring
- Possibility of increased frequency of breakdowns and maintenance
In order to eliminate these risks, we recommend selecting a deburring machine based on the following examples.
- Forming deburring: Multi-axis robotic deburring machine, chemical deburring machine.
- Cutting burr: Belt sander type deburring machine, disc sander type deburring machine.
- Drilling deburring: General-purpose machines (machining centers, CNC lathes), air blast deburring machines.
- Welding burr: Wet blasting machine, laser deburring machine.
- Heat treatment deburring: Tumbler type deburring machine, vibration type deburring machine.
Consider the Required Deburring Precision and Finish Quality
The deburring machine you choose will depend on the precision of deburring your company requires.High accuracy doesn’t necessarily mean the product will be the best for your needs. In general, when purchasing a machine with high deburring accuracy, you should pay attention to the following points:
- The required production rate may not be achieved (because there is a trade-off between accuracy and speed)
- Advanced technology and highly specialized technology are required, and equipment becomes complex.
You can determine the accuracy of a deburring machine by checking the processing time, pressure, processing time, and consumables used.
Evaluate the Degree of Automation and Ease of Operation
The type of deburring machine you should select and the peripheral equipment you need to purchase will change depending on the stage of automation of the deburring process that your company requires.Automating the deburring process can generally be divided into the following stages:
- Manual operation: Completely manual deburring.
- Semi-automated: Some processes are automated, but human intervention is required for operation and monitoring.
- Full automation: The deburring process is fully automated and operates with minimal human intervention.
While automation reduces the amount of manpower and effort required, you should keep the following points in mind:
- Automated equipment is expensive and requires a large initial investment.
- Maintenance is complex and requires specialized skills.
- It may be difficult to accommodate changes in production lines or different types of products.
When deburring automation is divided into the three levels above, the following machines are suitable for each level of deburring automation.
- Manual operation: Machines that are easy to operate and suitable for direct manual work, such as belt sander type deburring machines and disc sander type deburring machines.
- Semi-automated: Machines with partially automated processes, such as tumbler-type deburring machines and vibration-type deburring machines.
- Full automation: multi-axis robotic deburring machine, laser deburring machine, automated general-purpose machine (machining center, CNC lathe, etc.)
Consider Working Environment and Safety
Deburring machines have two types of working environments: wet and dry.Wet deburring involves immersing the material in chemicals or electrolytes.
For example, a wet deburring machine is effective when processing the following workpieces.
- If metal dust is a problem: Metal dust is explosive, so use a wet deburring machine to suppress dust.
- Heat-sensitive materials: If the material is easily deformed or damaged by the heat during processing, it may be more suitable to use a wet deburring machine with a cooling effect.
There are the following types of wet deburring machines:
- Wet blast machine
- Water jet deburring machine
- Chemical deburring machine
- Electrolytic deburring machine
On the other hand, a dry deburring machine refers to a type of deburring machine that directly processes the workpiece with a tool, without immersing the workpiece in liquid.
The following workpieces can be processed using a dry deburring machine.
- Materials that generate less dust or are easier to manage: non-metallic materials such as plastic and wood
- If a clean work environment is required: Processing precision products such as electronic parts is delicate, so it is best not to expose them to liquids.
If you process a workpiece using a deburring machine that is not suitable for the working environment, the following problems will occur, so be careful.
- When using a wet deburring machine (e.g. wet blasting machine) on water-sensitive materials such as wood or plastic, the material may absorb moisture and become deformed or damaged.
- Processing metal using dry deburring machines (e.g. belt sander type, disc sander type) may affect quality due to heat and dust generation.
We recommend selecting a deburring machine with an appropriate working environment for the material being handled.
It is Possible to Deburr in Consideration of SDGs
Deburring methods that generate waste or methods that threaten safety, such as explosions, can hinder the ability to receive orders from major companies. Therefore, it is necessary to select processing methods and tools that do not generate waste.For example, if you choose a metal tool that does not produce waste, it can be resharpened and used for a long time, and the tool that is no longer usable will be taken over and reused by the metal manufacturer.
Additionally, in the pursuit of sustainability, methods that could be harmful to humans or the environment in which they are used, such as explosions, are also avoided.
If you want to win a project from a major company, we recommend using a highly safe processing method using a mill.
Up to this point, we have explained how to choose a deburring machine. In the next section, we will finally introduce specific manufacturers. If you are looking for a manufacturer that manufactures the best deburring machine for your company, read on to the next section.
Recommended Manufacturers of Deburring Machines
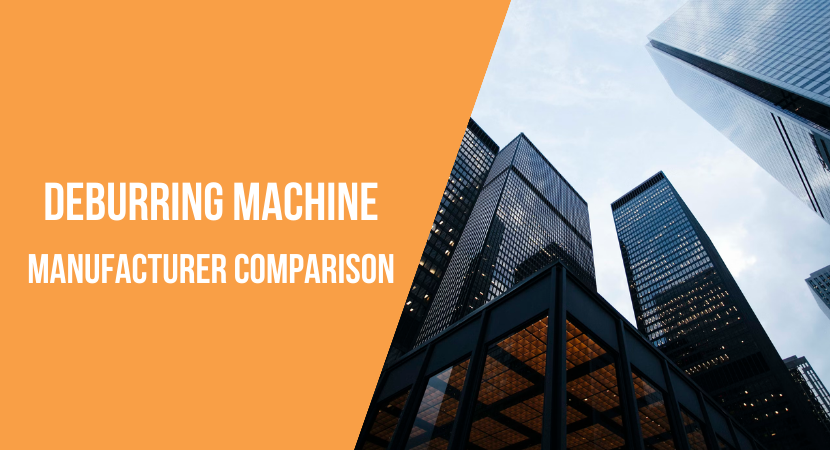
There are several companies that manufacture deburring machines.
The following 12 companies are highly recommended by us.
Kreuz | Authentic | Amada | ST Link | Nitto Kohki | Resonac Gas Products | Shinto Kogyo | Iwatani Sangyo | One box | Sugino Machine | Acritec | Nakajima Seiko | |
---|---|---|---|---|---|---|---|---|---|---|---|---|
Brush Type Deburring Machine |
– | ✓ | ✓ | ✓ | – | – | – | – | – | – | – | – |
Roller type Deburring machine |
– | ✓ | ✓ | ✓ | – | – | – | – | – | – | – | – |
Multi-axis Robotic Deburring Machine |
✓ | – | – | – | ✓ | – | – | – | – | – | – | – |
NC Deburring Machine |
✓ | – | ✓ | – | – | – | – | – | – | – | – | – |
Belt Sander Type Deburring Machine |
– | – | – | – | ✓ | – | – | – | – | – | – | – |
Disc Sander Type Deburring Machine |
– | – | – | ✓ | – | – | – | – | – | – | – | – |
Tumbler Type Deburring Machine |
– | – | – | – | – | ✓ | – | – | – | – | – | – |
Air Blast Deburring Machine |
– | – | – | – | – | – | ✓ | – | – | – | – | – |
Laser Deburring Machine |
– | – | – | – | – | – | – | ✓ | – | – | – | – |
Wet Blast Machine |
– | – | – | – | – | – | – | – | ✓ | – | – | – |
Water Jet Deburring Machine |
– | – | – | – | – | – | – | – | – | ✓ | – | – |
Electrolysis Deburring Machine |
– | – | – | – | – | – | – | – | – | – | ✓ | – |
Small/Desktop Deburring Machine |
– | – | – | – | – | – | – | – | – | – | – | ✓ |
If you have any questions or require help choosing a company, please contact us. Our team of specialists would be happy to help you!
Contact Us Today
Kreuz
Kreuz is a company that has continued to specialize in research into the core technology of deburring. Founded in 1989, Kreuz has developed a variety of deburring products, and in 2019 celebrated their 30th anniversary. Since their founding, they have continued to take on the challenge of solving deburring problems, which are inevitable in manufacturing.
Kreuz provides hardware technologies such as the deburring robot “Robo Router”, deburring tools, floating devices that absorb variations, and high-performance spindle motors.
In addition to their fantastic machinery, they also develop software technologies such as simulation and offline teaching.
Kreuz has the following types of deburring machines
- 5-axis CNC controlled gate type deburring machine “BARISTA”: Offering multiple machines including high-rigidity robots
- Articulated robots: including the original 5-axis robot “Robo Router” that can move freely in three dimensions
Kreuz has specialized technology in deburring and contributes to solving problems in the manufacturing field by developing a wide variety of products and innovative robot technology. Its product range combines versatility and technical expertise to meet the various needs of the manufacturing industry.
Authentic
Authentic focuses on automation to improve productivity and address labor shortages. They manufacture brush-type deburring machines, including models like AuDeBuCX, AuDeBu 1000, and AuDeBu BlackLine1100. These machines cater to different workpiece sizes and offer ideal deburring without putting excessive load on the product, showcasing Authentic’s technological diversity.
Amada
Amada Corporation, with its origins dating back to a machine repair shop, has evolved into a global comprehensive manufacturer of metal processing machinery. They handle various types of deburring machines, including roller-type, brush-type, and laser processing machines, delivering high-performance solutions with a rich history of innovation.
ST Link
ST-Link, headquartered in Niigata, specializes in brush-type deburring machines under the “Metal Esthe” brand. Recognized for driving the future of the region, ST-Link provides solutions not only in deburring machines but also in laser processing, bending machines, and welding machines.
Nitto Kohki
Nitto Kohki, established in 1950, is known for its precision processing technology and automation capabilities. They excel in manufacturing air tools, power tools, vacuum equipment, hydraulic equipment, and various deburring machines. Their strengths lie in disc sander type, tumbler type, and vibration type deburring machines suitable for precision work on a wide range of materials.
Resonac Gas Products
Resonac Gas Products, a comprehensive industrial gas manufacturer, is involved in the production and sale of tumbler deburring machines. Their machines enable precise processing without damaging the product or roughening the surface, making them suitable for applications in rubber products, die-casting, and plastic products.
Shinto Kogyo
Shinto Kogyo, headquartered in Nagoya, specializes in air blast (sandblast) deburring machines. Their air blast deburring machines come in various types, offering flexibility in processing and responding to the layout and size requirements of different factories. Shinto Kogyo provides technology to diverse industries, showcasing highly versatile capabilities.
Iwatani Sangyo
Iwatani Sangyo, a comprehensive energy business, manufactures and sells wet blast deburring machines and laser deburring machines. Their wet blast deburring machines, especially those with patented wet blast wide guns, are effective for removing burrs from various materials, including resins and ceramics.
One Box
One Box Co., Ltd., located in Toyonaka City, Osaka Prefecture, specializes in wet blast deburring machines. Despite its size, the company focuses on manufacturing welding and deburring machines. With a track record in providing wet blast deburring machines to automobile sales and maintenance businesses, One Box offers specialized solutions.
Sugino Machine
Sugino Machine, known for precision processing technology, manufactures water jet deburring machines. These machines can deburr with high-pressure water, providing not only high-precision deburring but also energy-saving solutions. Sugino Machine is committed to offering innovative deburring options aligned with SDGs.
Acrytech
Acrytech, a machine manufacturer in Kanagawa Prefecture, specializes in chemical and electrolytic deburring equipment. Their electrolytic deburring machine stands out for its high operability regardless of the material. It offers the advantage of removing burrs from multiple locations and workpieces simultaneously without concerns about secondary burrs.
Nakajima Seiko
Nakajima Seiko, a smaller-scale company in Aichi Prefecture, manufactures tabletop deburring machines. The SAMMELEON model is a compact deburring machine designed for automation, providing a cost-effective solution for companies and factories looking to automate the deburring process. It is especially recommended for test cases due to its affordability.
We hope our comprehensive guide on picking the best deburring machine has helped you in your search. Please do feel free to browse our website to see other related machinery and feel free to engage with us on any questions you may have. We would be happy to help!
Interested in Deburring Machines? Contact us today!
If you have any questions or concerns regarding any of the topics mentioned here or require help choosing a company, please contact us. Our team of specialists would be happy to help you!Contact Us Today