Evolving from the resin-based 3D printers developed in the 1980s, Metal 3D Printers can process various metals, producing components known for their durability and thermal resistance.
Industries including automotive, healthcare, aerospace, and scientific research extensively utilize Metal 3D Printing technology.
This guide will explore different Metal 3D Printer models, offer insights on how to choose the best one for your needs, and highlight leading manufacturers in the field.
目次
Explaining 7 types of metal 3D printers
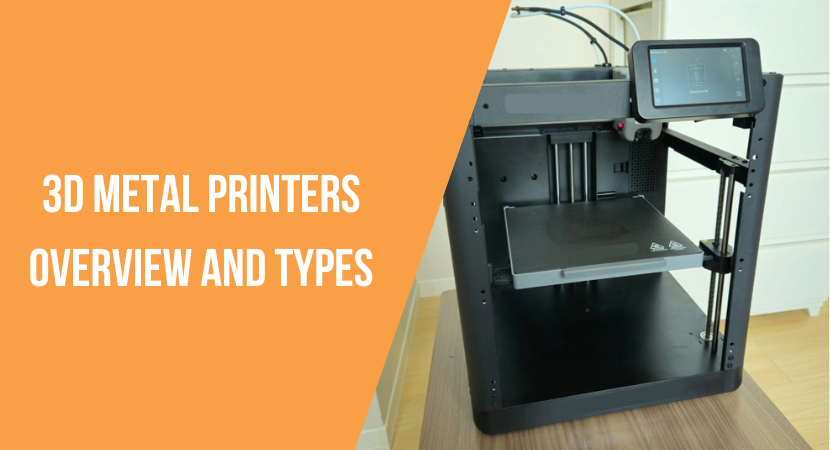
The structure of a metal 3D printer generally has the following components:
- Building room: A space where metal materials are layered and built, and is filled with inert gas because it uses high energy such as lasers and electron beams
- Base plate: A metal plate that serves as the base of the model. It is installed at the bottom of the modeling chamber and controls the temperature and position
- Head: The part that sprays metal materials or binder agents, or irradiates laser or electron beams
- Hopper: A container for supplying metal materials. Contains powder, filament, or rod-shaped metal materials
- Controller: The part that reads 3D data and slice data and controls the movement of the head and base plate. Computers, tablets, etc. are used
Metal 3D Printers primarily fall into two categories: Powder Bed Fusion (PBF) and Directed Energy Deposition (DED).
Powder Bed Fusion involves layering metal powder and employing a laser or electron beam to melt and fuse layers together, creating a three-dimensional object. Techniques such as Selective Laser Melting (SLM) and Electron Beam Melting (EBM) fall under this category.
This method achieves high precision and complexity by meticulously melting metal powder layer by layer.
Directed Energy Deposition, alternatively, utilizes concentrated thermal energy to melt material as it’s deposited, crafting 3D objects layer by layer.
Also known as Laser Engineered Net Shaping (LENS), this method excels in fabricating intricate and bespoke components.
DED’s continuous melting and solidification process allows for the creation of detailed and precise structures, perfect for complex designs and tailored parts.
Metal 3D printers have a total of seven output methods.
Method | Features | Appropriate installation location |
---|---|---|
Laser sintering method (SLS) |
High precision modeling possible | Factory suitable for prototypes and small quantity production |
Laser melting method (SLM) |
High-density modeling possible | Factory suitable for prototypes and small quantity production |
Binder jet method (BJ) |
Enables speedy modeling | Factory suitable for medium volume production |
Direct metal laser sintering method (DMLS) |
No need for post-processing | Factory suitable for manufacturing large parts |
Electron beam melting method (EBM) |
High-density modeling possible at high temperatures | Factories suitable for fields such as aerospace and medical care |
Laser direct deposition method (LENS) |
Possible to repair worn parts and add additional parts | A factory suitable for repairs and improvements |
Liquid metal Inkjet 3D printing |
Flexible modeling possible at low temperatures | Factory suitable for manufacturing electronic parts and sensors |
Laser sintering method (SLS)
Laser sintering (SLS) is a method of creating three-dimensional objects by irradiating powdered metal or resin with a laser and sintering it.This technology has the advantage of not requiring processes such as molds or cutting, and can create complex shapes and internal structures.
The strengths of SLS include the following points.
- Wide choice of materials: SLS can be used with a variety of materials, including nylon, ceramics, and metals such as copper and titanium
- No need for support material: In SLS, the powder in the area not hit by the laser acts as a support material
- Recyclable: With SLS, powder other than the object to be built can be reused
Although the surface of the modeled object is rough and the accuracy is low, it is suitable for large-scale objects and is mainly used in fields such as aerospace, medicine, and advanced research.
Laser melting method (SLM)
Selective Laser Melting (SLM) is a process for fabricating three-dimensional metal objects by directing a laser beam to melt powdered metal.Originating in Germany during the 1990s, SLM is an evolution of Selective Laser Sintering (SLS), offering the ability to create models with higher density through complete melting of the powder.
The strengths of this technology are as follows.
- Capable of high-density modeling: Capable of modeling with high strength and heat resistance
- Wide choice of materials: Compatible with metals and their alloys such as iron, aluminum, titanium, and nickel
- Visualization of the melt pool: Measures the temperature and shape of the melt pool at the laser irradiation area and records data of the modeling process
On the other hand, SLM also has the following weaknesses.
- High equipment costs: Requires special equipment such as high-power lasers, inert gas supply/exhaust equipment, and high-temperature sintering furnaces
- Solidification cracking and internal stress may occur: Solidification cracking due to melting and solidification due to laser irradiation and internal stress due to thermal cycles during modeling may occur
- Slow printing speed: There are limits to laser scanning speed and power
By using this technology, processes such as molds and cutting are not required, and complex shapes and internal structures can be created.
Therefore, it is used in fields such as aerospace, medicine, and energy.
Binder jetting method
The Binder Jetting technique involves constructing three-dimensional objects by ejecting a liquid binder onto metal powder through a nozzle, leading to solidification.This approach eliminates the need for molds or machining, enabling rapid prototyping and manufacturing.
Binder Jetting is widely applied across multiple sectors, including automotive, architecture, and industrial design.
The strengths of the binder jetting method are as follows.
- Fast printing speed: No processes such as laser irradiation or melting and solidification are required; printing is possible just by spraying the binder
- Large build volume: No need for high energy sources such as lasers or electron beams, allowing for large build chambers
- Wide choice of materials: Compatible with metals and their alloys such as iron, aluminum, titanium, and nickel
However, the binder jetting method also has the following weaknesses.
- Requires post-processing: The built object has low strength and needs to be strengthened by sintering or impregnation treatment
- Printed object shrinks: Possibility of shrinkage of about 20% after sintering
- Rough surface: Powder particles may remain and the surface may become rough
Although the surface of the printed object may not be smooth and the precision may not be high, it is possible to print complex shapes including cavities.
Direct metal laser sintering (DMLS)
Direct Metal Laser Sintering (DMLS) is a technique for producing three-dimensional objects by using a laser to partially melt metal powder.This technology is similar to selective laser sintering (SLS), but melts the powder at higher temperatures to create denser features.
Eliminating the need for traditional molds or machining, DMLS excels in fabricating intricate designs and internal geometries.
This method is especially useful in the aerospace, medical, and energy industries.
The strengths of DMLS are as follows.
- High-density modeling: Partial melting using a laser reduces pores and achieves high strength and heat resistance
- Wide choice of materials: Compatible with a variety of metals and alloys, including iron, aluminum, titanium, and nickel
- Melt pool visualization: Measure the melt pool in the laser irradiation area and collect data on the printing process
On the other hand, DMLS also has some weaknesses.
- High equipment costs: Requires special equipment such as high-power laser, inert gas supply/exhaust equipment, and high-temperature sintering furnace
- Occurrence of solidification cracks and internal stress: Melting and solidification caused by laser irradiation may cause solidification cracks and internal stress
- Limitations to printing speed: Printing speed may be slow due to laser scanning speed and power limitations
The surface of the model is smooth and highly accurate, and it is also possible to create cavities inside.
This eliminates the need for processes such as molds and cutting, and its applications are expanding in the aerospace, medical, and energy fields.
Electron beam melting (EBM)
Electron Beam Melting (EBM) is a process that crafts three-dimensional objects by melting metal powder with an electron beam.Originating from Sweden in the 1990s, EBM shares similarities with Selective Laser Melting (SLM) but operates in a high vacuum, enhancing the quality of the final product.
Without the need for conventional molds or machining, EBM excels in producing intricate designs and internal features.
It finds significant applications within the aerospace, medical, and energy sectors.
The strengths of EBM are as follows.
- High quality printing: By using an electron beam in a high vacuum environment, it is possible to print with fewer pores, high strength and heat resistance
- Wide choice of materials: Compatible with metals and alloys such as titanium, cobalt chrome, and Inconel
- No post-processing required: the object is built in a preheated powder bed, eliminating the need for heat treatment to relieve stress
However, EBM also has the following weaknesses.
- High equipment costs: Requires special equipment such as a high-vacuum chamber and high-power electron beam source
- Limitations in printing speed: The speed may be slow due to the scanning speed and power limitations of the electron beam
- Surface roughness: Powder particles may remain and the surface may become rough
The surface of the model is smooth and highly accurate, and it is also possible to create a cavity inside.
Because molds and cutting are not required, applications are expanding, especially in the aerospace, medical, and energy fields.
Laser direct deposition method (LENS)
Laser directed energy deposition (LENS) is a method of creating three-dimensional objects by irradiating metal powder ejected from a nozzle with a laser and layering it on the surface of a base material.This technology was developed in the 1990s at Sandia National Laboratories in the United States, and is used to repair, reinforce, and add functionality to metal parts.
The strengths of LENS are as follows.
- Direct lamination to existing parts: Metal can be laminated directly to the base part, extending the life of the part or adding functionality
- Suitable for metals that are resistant to high temperatures: The laser melts metal powder heated to high temperatures, so it can be applied to metals and alloys such as titanium and nickel
- Precise modeling: Achieve precise modeling by controlling laser scanning speed, power, and nozzle blowout volume
On the other hand, LENS also has the following weaknesses.
- High equipment costs: Requires special equipment such as high-power lasers, high-quality metal powder, and inert gas supply/exhaust equipment
- Limitations in printing speed: Printing speed may be slow due to limitations in laser scanning speed and power
- Necessity of post-processing: Residual stress and distortion may occur in the modeled object, requiring heat treatment to remove stress and cutting to adjust accuracy
The surface of the model is smooth and highly accurate, and it is also possible to create a cavity inside.
This makes it widely used for repairing metal parts and adding functionality.
Liquid metal inkjet 3D printing
Liquid metal inkjet 3D printing is a method of printing three-dimensional objects by spraying ink containing metal particles dispersed in a liquid from a nozzle and fusing them at high temperatures.This technology was developed by the Israeli company Xjet, and unlike traditional metal 3D printing methods, it does not use powder or lasers and can be operated like an inkjet printer.
It is used in the medical, aerospace, and automotive industries because it is capable of producing high-definition and smooth surfaces.
The strengths of liquid metal inkjet 3D printing are as follows:
- High-definition modeling: By spraying submicron-level metal particles and fusing them at high temperatures, it is possible to create designs with fewer pores, high strength, and heat resistance
- Low equipment costs: No need for special equipment such as high-power lasers or high-vacuum chambers
- Easy to operate: Just load the ink cartridge and you can easily print
On the other hand, it also has the following weaknesses.
- Slow printing speed: There are limits to the spray speed and amount of metal particles, so the printing speed may be slow
- Small printing volume: The size of the build plate is limited, making it difficult to print large sizes
- Narrow material choices: Currently limited to stainless steel and titanium, material types and compositions are limited compared to other metal 3D printing technologies
The surface of the model is smooth and highly accurate, and it is also possible to create a cavity inside.
These properties have led to applications in the medical, aerospace, and automotive industries, among others.
So far, we have explained the types of metal 3D printers.
In the next section, we will explain the advantages and disadvantages of introducing a metal 3D printer, so if you want to compare the advantages and disadvantages before introducing it, please read on.
Advantages and disadvantages of introducing a metal 3D printer
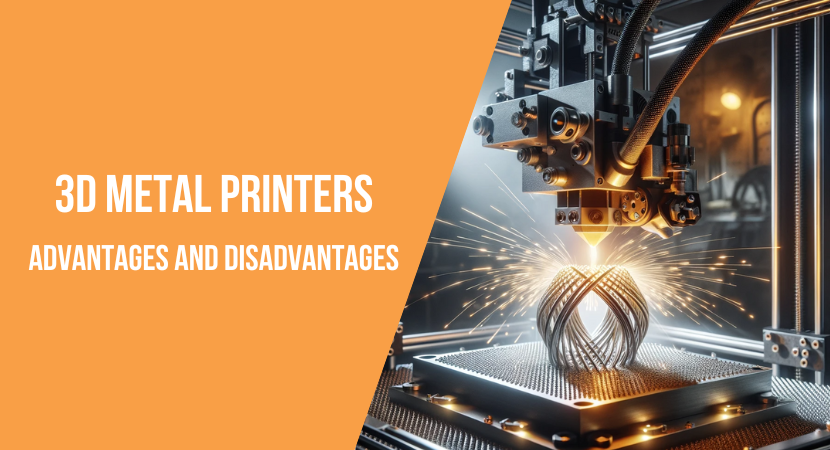
When introducing a metal 3D printer, you need to consider whether it is really a necessary choice for your company by comparing both the advantages and disadvantages.
In this section, we will explain the specific advantages and disadvantages of metal 3D printers.
Advantages
By introducing a metal 3D printer, you can get the following benefits:- Products with high strength and complex shapes can be manufactured
- The weight of the molded product can be reduced
- Efficiency of assembly work is possible
- Fast delivery possible
Products with high strength and complex shapes can be manufactured
Traditionally, casting, cutting, and assembly techniques have been used to manufacture metal parts.However, with these methods, it was difficult to manufacture products with particularly complex internal shapes and lightweight, high-strength products.
Metal 3D printers have the following features:
- Products with internal cavities or lattice structures can also be manufactured at once without support structures
- Products with different shapes can be easily manufactured by simply changing the design data
- Since materials are used only in the necessary areas, lightweight yet strong products can be made
These features make 3D metal printers especially useful for manufacturing products with complex geometries or specific functions, such as lightweight, high-strength turbine blades in the aerospace industry or customized artificial joints in the medical field. I am.
Can be light weight
Since parts can be easily hollowed out, the weight of objects made with metal 3D printers can be reduced.Reducing the weight of printed products provides the following advantages.
- Lighter parts can improve fuel efficiency, especially in the automotive and aircraft industries
- Improves power transmission efficiency and increases speed of drones and robots
- Reduced material costs: Lower production costs because less material is needed
- Design freedom: designs not possible with traditional manufacturing methods can be achieved
Metal 3D printers offer innovative solutions in these areas, offering multiple benefits including improved product performance, reduced production costs, and environmental friendliness.
-
Advantages gained by being lighter
For example, in what industry or application will it be used?
Enables more efficient assembly work
Since one part can have multiple functions, the number of parts can be reduced and work efficiency can be improved.For example, with a metal 3D printer, it is possible to reduce the number of parts as shown below.
- Aerospace parts: For example, one fuel nozzle, which used to be assembled from about 25 to 30 parts, can now be manufactured as a single part
- Automotive parts: Engine parts and car body structural parts that require more than 140 parts can be manufactured as one complex part
- Medical devices: Custom-made surgical implants, artificial joints, etc. made from a few to dozens of parts can be manufactured as a single part
This simplifies the manufacturing process, improves quality and reduces failure rates, improving overall quality and reliability.
Fast delivery
Because we can flexibly respond to design changes, we can deliver products on short delivery times.In conventional manufacturing, design modifications are a common occurrence.
Adjustments to the design are frequently needed, espeically when it comes to the development phase of intricate components or uniquie one of a kind products.
When changes to the design are necessary, traditional techniques often require the creation of new molds or alterations to production methods, resulting in delays ranging from weeks to months.
Yet, with the advent of Metal 3D Printing, it’s now feasible to bypass previously time-consuming and labor-intensive processes.
.
- Fast implementation of design changes
- No need to create types
- Production flexibility
For example, parts that would take months using traditional manufacturing methods can be completed in weeks or even days with 3D printing.
Disadvantages
Introducing a metal 3D printer is not only a good thing.You should also consider the following points when considering implementation.
- Dimension accuracy may not meet standards
- The surface of the printed product may be rough
- Unsuitable for mass production
Dimension accuracy may not meet standards
If dimensional accuracy of 10μ level is required, additional processing is required.Therefore, 3D metal printers are difficult to use in the following applications.
- Precision industries that require extremely high dimensional accuracy, especially fields such as aerospace and medical equipment
- When a precise fit with other parts is required, such as internal parts of an engine or connecting parts of precision equipment
For such applications, we recommend using machines and technologies such as CNC machining centers, electric discharge machining, and precision cutting.
Rough Surface
3 Metal 3D printers do not have surface smoothing technology, so if a high level of surface roughness is required, additional processing is required.In particular, it is not suitable for the following uses.
- Fields that require high precision and surface quality, such as aerospace and medical equipment
- Products where aesthetics are important, such as jewelry and luxury goods
- Parts that control fluid flow, such as nozzles and piping
If these processes are required, we recommend using the following equipment.
- CNC machines: used for post-processing of metal 3D printed parts to improve accuracy and surface quality
- Sanding machine: smooth the surface and improve the appearance of the product
- Electropolishing: Applicable to parts that require high precision
Unsuitable for mass production
Metal 3D printers are often not suitable for mass production.The main reasons are as follows.
- Metal 3D printing takes longer to produce because parts are built layer by layer
- High cost per unit product due to high quality materials and technology required
- Variations in the manufacturing process can make it difficult to maintain consistent quality
If you need mass production, the following equipment is suitable:
- Injection molding: Producing parts at high speed by injecting material into a mold
- Stamping press: stamping parts from metal sheets
- CNC machining: runs a large number of machines, especially suitable for mass production of metal parts
So far, we have explained the advantages and disadvantages of introducing a metal 3D printer.
Next, we’ll delve into the important factors you need to consider when selecting a Metal 3D Printer for your business.
If finding the ideal Metal 3D Printer for your company is your goal, continue reading.
5 Points Comparing Metal 3D Printers
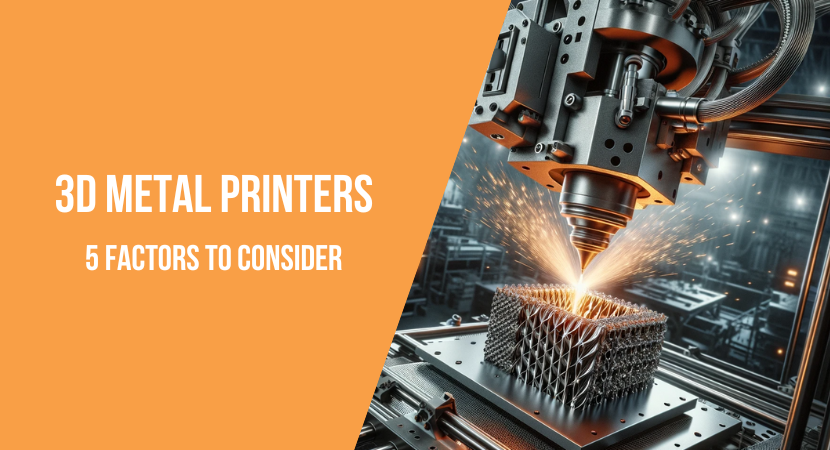
The following points should be compared when selecting a metal 3D printer.
- Lamination pitch
- Laser power
- Powder flow rate
- Build box temperature
- Price
Lamination pitch
The lamination pitch refers to the lamination thickness.By changing the lamination pitch, the following three elements will change.
- Appearance of the modeled product
- Building time
- Strength of printed product
For example, if the lamination pitch is fine, the following characteristics will appear in the printed product.
- Lamination marks are less noticeable, allowing for smooth, strong, and precise modeling
- Easy to create detailed structures and curved surfaces
- Longer build time and higher cost
Conversely, if the lamination pitch is coarse, a printed product with the following characteristics will be created.
- Lamination marks are easily noticeable, resulting in poor appearance and low strength of the model
- Difficulties in modeling fine structures and curved surfaces
- Shorter build time and lower costs
Therefore, it is necessary to decide what to prioritize before setting the stacking pitch.
Laser output
Laser power refers to the intensity of the laser used to melt metal powder.The following three factors change when the laser output changes.
- Quality of printed product
- Building time
- Printing cost
For example, when the laser power is high, the following characteristics occur:
- Improve the quality of printed products such as density, strength, and heat resistance by more efficient melting of metal powder
- Metal powder can be melted faster, reducing build time
- Deterioration of equipment due to laser power consumption and heat increases, making printing costs high
Conversely, if the laser power is low, a printed product with the following characteristics will be produced.
- Insufficient melting of metal powder reduces the quality, density, strength, and heat resistance of the printed product
- Modeling time is longer due to slower melting speed
- Low cost due to less power consumption and equipment deterioration
Therefore, it is necessary to set the laser output by considering the balance between the quality of the printed product, the printing time, and the printing cost.
Powder flow rate
Powder flow rate refers to the amount of metal powder delivered during 3D printing.Changes in powder flow rate affect the quality of the printed part, the printing time, and the printing cost.
For example, increasing the powder flow rate produces the following characteristics:
- Increasing the supply of metal powder improves the stability of the molten pool, resulting in higher density, strength, and heat resistance of the model
- Fast metal powder supply speed improves build speed and shortens build time
- Increased metal powder consumption increases material costs and increases manufacturing costs
Conversely, if the powder flow rate is reduced, a printed product with the following characteristics will be created.
- Reduced supply of metal powder reduces the stability of the molten pool, which reduces the density, strength, and heat resistance of the model
- The metal powder feed rate is slower, which reduces the build speed and increases the build time
- Reduced metal powder consumption, resulting in lower material costs and lower build costs
It is necessary to set the powder flow rate by considering the balance between the quality of the printed product, the printing time, and the printing cost.
Build box temperature
Build box temperature refers to the temperature inside the build area during 3D printing.Changing the build box temperature will affect the quality of your build, build time, and build cost.
For example, if the build box temperature is high, the following effects will occur.
- Smaller temperature differences in metal parts reduce thermal stress and strain, improving precision, strength, and heat resistance of printed parts
- Overall build time is longer due to increased post-print cooling time
- Maintaining the high temperature inside the build box increases electricity and gas consumption, resulting in high printing costs
Conversely, if the build box temperature is low, the following characteristics will occur:
- The temperature difference between metal parts increases, increasing thermal stress and strain, which reduces the accuracy and strength of the printed product
- Reduced cooling time after printing, shortening overall build time
- Less energy consumption to maintain low temperature inside the build box, lowering printing costs
It is necessary to set the build box temperature appropriately, taking into account the balance between the quality of the printed product, the printing time, and the printing cost.
Price
You need to choose a metal 3D printer according to your budget and purpose.The price range for metal 3D printers is very wide, with cheap ones starting at around 10,000 USD and expensive ones costing hundreds of thousands of dollars.
Therefore, you need to choose a machine that matches your company’s use of the metal 3D printer and the required precision.
The price of a metal 3D printer often changes depending on the following factors, which are introduced as comparison standards.
Lamination Pitch Laser Power Powder Flow Rate Build Box Temperature When comparing inexpensive metal 3D printers with expensive ones, each has the following characteristics.
Expensive metal 3D printer | Cheap metal 3D printer | |
---|---|---|
Lamination pitch | Lamination pitch is rough, but printing is relatively fast | High-resolution and high-precision modeling possible with fine layer pitch |
Laser output | Several tens of W to several hundred W | High-speed printing is possible with an output of several hundred W to several kW |
Powder flow rate | Difficult to secure a uniform powder layer | Enables precise control and ensures uniform powder layer |
Build box temperature | Due to limited temperature control settings, distortion of the printed product is likely to occur | Precise control is possible and distortion of the printed product is less likely to occur |
In addition, expensive metal 3D printers and cheap metal 3D printers each have their own disadvantages, so be careful.
Generally, expensive metal 3D printers are used in the space industry, medical equipment, automobiles, and other fields where high-precision, complex parts manufacturing is required.
On the other hand, inexpensive metal 3D printers are often used in educational and research institutions, prototyping, and custom parts manufacturing, where ease and speed are more important than precision.
So far, we have explained the points necessary to compare when choosing a metal 3D printer.
In this next section, we will introduce specific manufacturers that produce metal 3D printers.
5 Recommended Metal 3D Printer Manufacturers
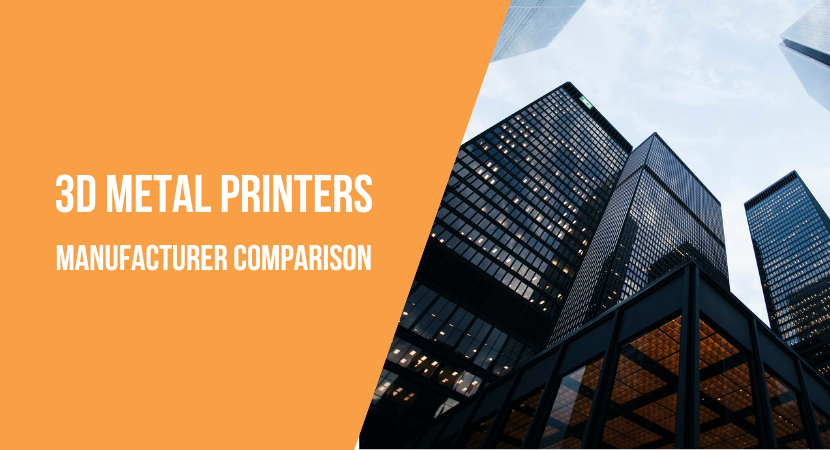
The following are some of the major manufacturers of Metal 3D Printers:
EOS | GE Additive | Nikon SLM Solutions |
3D Systems | Renishaw | XJet | |
---|---|---|---|---|---|---|
Laser Sintering Method (SLS) |
– | ✓ | ✓ | – | – | – |
Laser Melting Method (SLM) |
✓ | ✓ | ✓ | – | – | – |
Binder Jet method |
– | – | – | – | – | – |
Direct metal laser Sintering method (DMLS) |
– | – | ✓ | ✓ | ✓ | – |
Electron beam melting method (EBM) |
– | ✓ | – | – | – | – |
Liquid metal Inkjet 3D printer |
– | – | – | – | – | ✓ |
EOS
EOS is a pioneer in industrial 3D printing, founded in Germany in 1989.We develop and sell 3D printers that can print high-quality parts using a variety of materials such as metal and resin.
In the 3D printing field, we also provide customization of mechanical products, development of materials and software, and modeling services.
EOS manufactures metal 3D printers using a technology called powder bed fusion (PBF).
PBF is a method in which metal powder is melted using a heat source such as a laser or electron beam, and then stacked in layers to form parts.
The company’s metal 3D printers can handle not only common metal materials such as stainless steel and titanium alloys, but also specialized metal materials such as maraging steel and nickel-based alloys.
Therefore, EOS’ metal 3D printers have been delivered to the following industries.
- Aerospace industry: Printing parts such as fuel injection nozzles and brackets
- Automotive industry: Molding engine and chassis parts and tools such as press molds
- Medical industry: Printing parts such as artificial joints and dental implants
GE Additive
GE Additive operates an additive manufacturing (metal 3D printing) business as a member of the GE Group.In addition to developing and selling metal 3D printers, the company provides materials, software, and consulting services, and provides innovative products and solutions for industrial fields such as aerospace and automobiles.
GE Additive offers two types of metal 3D printers: laser and electron beam.
The laser method uses a laser beam to melt metal powder and stack it in layers to form parts.
The electron beam method uses an electron beam to achieve a similar modeling process.
GE Additive’s metal 3D printers are used in the following industries:
- Aerospace industry: Printing parts such as fuel injection nozzles and turbine blades
- Automotive industry: Molding tools such as engine and chassis parts, press molds, etc.
- Medical industry: Printing parts such as artificial joints and dental implants
Nikon SLM Solutions
Nikon SLM Solutions, a leading German metal 3D printer manufacturer, was acquired by Nikon in September 2023.The firm specializes in the development and sale of metal 3D printers, alongside offering materials, software, and consulting services.
With this acquisition, Nikon has reinforced its dominance in the metal 3D printing industry and aims to collaborate with Nikon SLM Solutions in crafting high-quality products and solutions.
Nikon SLM Solutions provides metal 3D printers utilizing the laser powder bed fusion (L-PBF) technique.
This method employs a laser to fuse metal powder, layering it to create intricate parts.
Nikon SLM Solutions metal 3D printers are used in the following industries:
- Aerospace industry: Used by Boeing to create parts such as fuel injection nozzles and turbine blades
- Automotive industry: Used by Bosch to create tools such as engine and chassis parts, press molds, etc.
- Medical industry: Syntactics uses it to create parts such as artificial joints and dental implants
3D Systems
3D Systems, an innovator in the 3D printing industry, was established in the United States in 1986.This company designs and markets 3D printers capable of producing premium parts from diverse materials, including metal and resin.
In addition to customizing 3D printers, materials, software, and offering consulting services, 3D Systems delivers cutting-edge products and solutions to sectors such as aerospace, automotive, and healthcare.
Range of metal 3D printers: 3D Systems offers metal 3D printers leveraging two distinct technologies: laser powder bed fusion (L-PBF) and direct metal printing (DMP).
L-PBF technology involves a laser to fuse metal powder, layering it to fabricate parts.
Conversely, DMP creates components by melting metal powder and dispensing it through a nozzle.
Industry Case Studies: 3D Systems metal 3D printers are used in the following industries:
- Aerospace industry: NASA uses it to create parts such as rocket engine combustion chambers and nozzles
- Automotive industry: Used by Honda for molding tools such as engine and chassis parts, press molds, etc.
- Medical industry: Syntactics is used to create parts such as artificial joints and dental implants
Renishaw
Renishaw is a leading global entity based in the UK, specializing in metrology, motion control, spectral observation, and precision machining.It excels in the development and sale of metal 3D printers, along with providing materials, software, and consulting services.
The company is committed to delivering innovative products and solutions to sectors such as aerospace and healthcare.
Selection of metal 3D printers: Renishaw offers metal 3D printers employing laser powder bed fusion (L-PBF) technology.
This method utilizes a laser to melt metal powder, layering it to construct parts.
Renishaw’s metal 3D printers are used in the following industries:
- Aerospace industry: Airbus uses it to create parts such as fuel injection nozzles and turbine blades
- Automotive industry: Used by Land Rover to create tools such as engine and chassis parts and press molds
- Medical industry: Renishaw himself uses it to create parts such as artificial joints and dental implants
XJet
Founded in 2005, XJet is a rapidly growing company in the field of 3D printing technology.Headquartered in Rehovot, Israel, we are the world’s only manufacturer of liquid metal inkjet 3D printers.
The technology can be applied to a wide range of industries including aerospace, automobiles, medical equipment, and electronic equipment.
Looking to invest in your own Metal 3D Printer? Reach out to us!
Is the company really suitable for your goals? Are you choosing the right model? Please feel free to contact us if you have any concerns.We will consider the differences between each product and company and suggest the company that best suits your purpose.
Contact JET Global