It uses two molds, a punch and a die, to sandwich the plate material and bend it to the desired angle, and is mainly suitable for bending thin plates such as steel plates and aluminum plates.
Press brakes are used in everyday products such as home appliances and steel furniture, and are also essential machines in advanced industries such as automobiles and aircraft.
In this article, we will introduce the types and characteristics of press brakes, their advantages and disadvantages, four points to compare, and five specific manufacturers.
目次
4 types of press brakes and mechanisms
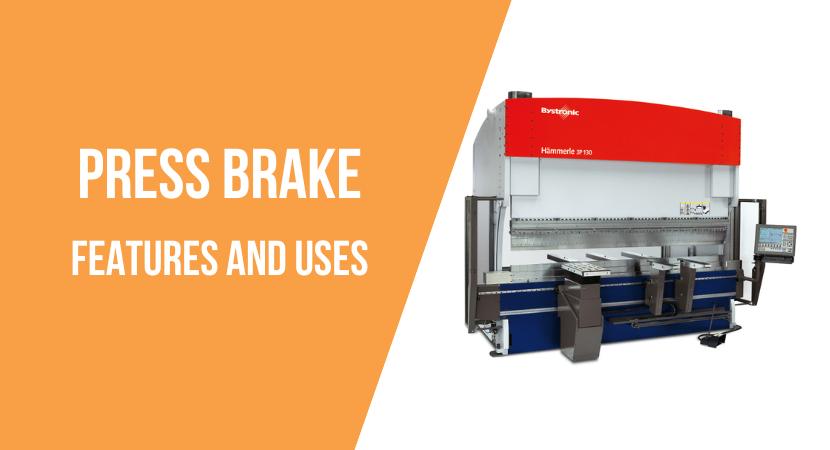
A press brake is divided into a press part that reciprocates up and down, and a part that attaches the receiving mold, and the types of press brakes are divided by drive method.
There are four main types of repairs:
- Mechanical press brake
- Hydraulic press brake
- Servo motor press brake
- Hybrid press brake
Mechanical press brake
A mechanical press brake is a method in which the press part is driven by the rotational movement of a motor.Since the processing speed is fast, it is suitable for bending small parts, but it is also difficult to adjust the pressure and control the speed.
The strengths of mechanical press brakes are as follows.
- Fast processing speed and high productivity
- Simple mechanical structure, easy maintenance
On the other hand, mechanical press brakes also have the following weaknesses.
- Difficult to adjust pressure and control speed, unsuitable for highly accurate bending
- Low pressing force, unsuitable for bending thick plates
It is used for bending small parts and for bending where accuracy is not very important.
Hydraulic press brake
Hydraulic press brake is a method that uses a hydraulic cylinder to drive the press part.This method is currently mainstream because it allows for flexible control of pressure and processing speed.
The strengths of hydraulic press brakes are as follows.
- High pressure capacity allows for bending of thick plates
- Multiple identical press brakes can be lined up side by side to bend long materials
On the other hand, hydraulic press brakes also have the following weaknesses.
- Uses a lot of hydraulic oil and generates a lot of heat, which has a large impact on the environment
- It is necessary to pay attention to maintenance and failure of hydraulic system
Therefore, it can be said that this technology is especially suitable for mass production.
Servo motor press brake
A servo motor press brake is a method that uses a servo motor to drive the press part.It has the great advantage of being environmentally friendly as it does not use hydraulic oil. In addition, it is especially suitable for highly precise bending processes because it allows precise control of pressure and processing speed.
The strengths of servo motor press brakes are as follows.
- Eco-friendly, as it uses less hydraulic oil and heat
- Suitable for high-precision bending as pressure and processing speed can be finely adjusted
However, this type of press brake also has some weaknesses.
- Unsuitable for bending thick plates due to low pressing force
- Machines are expensive and maintenance is complicated
These characteristics make servo motor press brakes an excellent choice, especially for bending operations that require precision.
Hybrid press brake
Hybrid (hydraulic servo) press brakes are an advanced system that combines the advantages of hydraulic and servo motor systems.- The press part is driven by controlling the hydraulic pump with a servo motor
- Precise control of machining speed and powerful hydraulic pressure can be achieved at the same time, allowing for high machining accuracy and efficiency
- It has an environmentally friendly design, as it uses less hydraulic oil and generates less heat
The strengths of the hybrid type (hydraulic servo type) press brake are as follows.
- Combines the powerful pressing force of a hydraulic system with the precise controllability of a servo motor system
- Improves machining accuracy and productivity, and reduces operating costs due to energy saving effects
However, this method also has some weaknesses.
- The price of the machine is high as an initial investment
- Regular maintenance of hydraulic system is required
Hybrid press brakes, which combine the advantages of hydraulic and servomotor systems, are the perfect choice for manufacturers who value high machining accuracy, productivity, and environmental performance.
Advantages and disadvantages of press brake
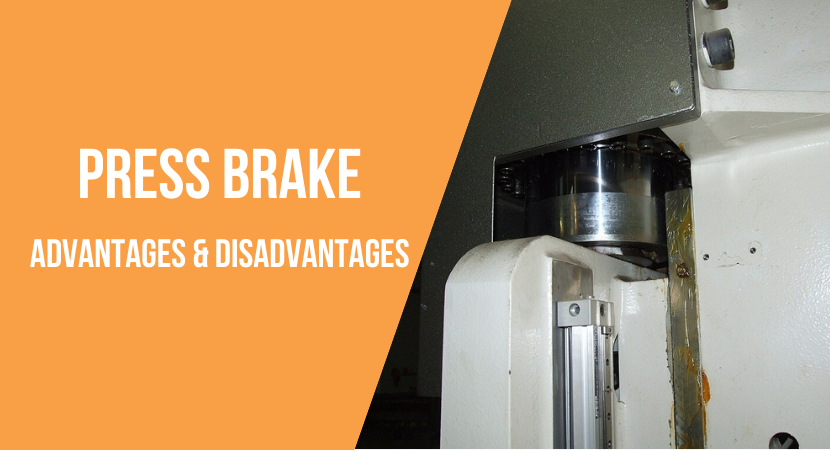
Machines for bending metal sheets include roll benders and folding machines. Here, we will explain the advantages and disadvantages of choosing a press brake.
Advantages of press brake
There are three major benefits of using a press brake:- A wide variety of mold types and combinations
- Can also handle bending of long materials
- High precision in bending process
A wide variety of mold types and combinations
Press brakes are able to meet a wide variety of metal processing needs.- A wide variety of bending shapes such as V-shape, U-shape, box-shape, etc. can be realized
- By combining molds, complex bending and continuous processing are possible
- Flexible response to unique design requirements
- Saves time and costs in repetitive tasks and mass production
Because of this feature, press brakes are useful in the following situations:
- Linear bending or precise angle adjustment is required
- Manufacturing parts with complex folds and multiple bending angles
- The process of adding shapes and angles to parts after processing
Overall, the variety of press brake mold types and combinations greatly improves flexibility and efficiency on the manufacturing site. This allows us to meet a wide range of product design requirements and manufacture high-quality products with short lead times.
Can also handle bending of long materials
Press brakes play an important role in manufacturing, especially when large panels or long strips of metal are involved. These machines are suitable for machining large parts and offer high precision and uniformity as well as flexible machining options.- Capable of processing building materials, large machine parts, and long frame structures
- Maintains consistent precision and quality even when processing long materials
- Available for different metal thicknesses and types, easy to customize for specific projects
The introduction of a press brake is especially effective when manufacturing large parts or precision bending of long materials is required. You can take full advantage of its capabilities in large-scale, precision-demanding projects such as building materials, aerospace parts, and frames for large transportation equipment.
Press brakes play a particularly important role in the manufacturing industry, where large panels and long metal strips are involved. Below, we will provide an overview of this advantage and explain in detail how it is used when compared to other metal processing machines.
High precision in bending process
Press brakes use sophisticated control systems and precision molds to bend metal sheets to predetermined angles and shapes.- Fine control with CNC technology enables bending at precise angles
- Available for consistent quality bending with the same settings even during mass production
- Complex bending patterns and multi-step machining can be easily set
Due to these features, press brakes play an important role in fields that require high quality and dimensional accuracy, such as aerospace, automobiles, and precision machine manufacturing.
Its precision bending capabilities are essential to improving product functionality, appearance, and consistency.
Disadvantages of press brake
On the other hand, press brakes also have disadvantages that you should be aware of.In particular, we recommend that you pay attention to the following points.
- Low productivity
- Requires an environment compatible with hydraulic oil and heat generation
- Machine costs can be high
Low productivity
When using a press brake, there are several points where productivity may be low.For example, the following situations often take some time.
- Press brake setup requires selection of appropriate molds, positioning, program settings, etc., which takes about 30 minutes to start production (compared to about 5-10 minutes for other processing machines) li>
- Bending with a press brake takes several tens of seconds (other machines often finish in a few seconds)
If you really need a machine with high productivity, we recommend considering the following machines.
- Panel bender: allows for fast, automated bending, especially suitable for large panels or simple bending in large quantities
- Roll forming machines: Ideal for bending continuous long materials at high speeds and useful for manufacturing continuous shapes such as profiles and channels
- Combination with automatic punching machine/laser cutting machine: A series of operations, including not only bending but also drilling and cutting, can be automated
Requires an environment compatible with hydraulic oil and heat generation
The use of press brakes requires special consideration in the design and maintenance of the workplace.- The hydraulic system of press brakes relies on hydraulic oil, and it is necessary to design flooring and drainage systems to prevent oil leaks, regularly replace and replenish the oil, and maintain oil quality with a filtering system.
- Excessive heat during operation affects machine performance and lifespan, so it is necessary to have cooling systems and proper ventilation.
The following machines can be used in place of press brakes in any environment.
- Servo press brake: Easy environmental control as it generates little heat and does not use hydraulic oil. Precise processing is possible and energy efficiency is high
- Electric press brake: Fully powered by electricity and has a lower environmental impact than hydraulic types. Features low energy consumption, and quiet and clean operation
When using press brakes, it is necessary to pay attention to the design and maintenance of the workplace, including environmental requirements and measures against heat generation.
Machine costs can be high
Workplace design and maintenance require special consideration when using press brakes. The main problems are handling of hydraulic fluid and heat generated by the machine.- Regular replacement and replenishment of hydraulic oil is required, and flooring and drainage design are required to prevent leakage
- Specific temperature maintenance and filtering for oil quality control are important to properly maintain hydraulic systems
- Requires cooling system and good ventilation to avoid affecting mechanical performance and durability
When looking for environmentally friendly alternatives, you can also consider the following options:
- Servo press brake: Can be used in a variety of environments because it generates little heat, does not use hydraulic oil, allows precision machining, and is highly energy efficient
- Electric press brake: Operated entirely by electric power, less environmental impact than hydraulic type, lower energy consumption, quieter operation
These alternative machines solve environmental requirements related to hydraulic fluids and heat generation issues during operation, allowing use in a wider range of environments. It is important to consider these points when selecting a press brake.
Six comparison points | Choosing a press brake
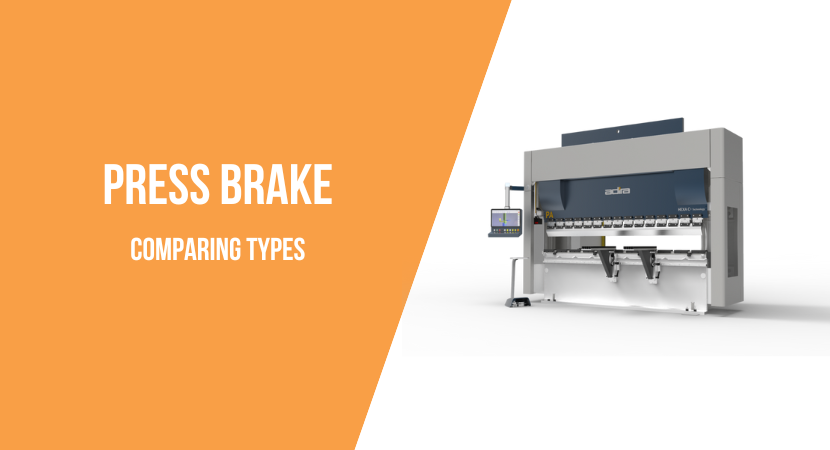
To compare press brakes and choose the best press brake for your company, you need to compare the following six points.
- Applying force
- Torque
- Frame length
- Accuracy
- Number of control axes
- Processing speed
Pressure force
Pressure force is the pressure that a press brake applies to a plate material, and changing the pressure force changes the accuracy, efficiency, and environmental impact of bending.Generally, if the pressure force of a press brake exceeds 100 tons, it is classified as having a high pressure force. We can perform high-precision bending of thick plates such as structural members for bridges, metal plates for construction machinery, and ship parts.
Machines with high pressurizing force have high installation and maintenance costs, generate a lot of hydraulic oil and heat, and often place a burden on the environment
On the other hand, press brakes with a pressurizing force of less than 100 tons are considered to have a low pressurizing force, and are used when processing thin metals used in electronic device cases, office furniture, bicycle parts, etc.
These machines are often less expensive, less expensive to maintain, and more environmentally friendly because they use less hydraulic fluid and less heat.
On the other hand, it is not suitable for bending thick plates or high-precision bending.
Torque
Press brake torque is the bending force applied between the punch and die.Torque varies depending on the thickness and hardness of the plate to be bent, the bending angle, the bending width, etc.
Press brake torque is generally classified as follows.
- Light torque (less than 50 tons): electronic equipment parts, decorations and accessories, prototyping, etc.
- Medium torque (50-100 tons): Auto parts, construction hardware, mechanical parts, etc.
- Heavy torque (over 100 tons): frames of heavy machinery, bridge members, large parts of ships, etc.
A large load is placed on the drive part of the press brake and the mold. There is a high risk of failure and damage due to overload, and high energy consumption.
On the other hand, press brakes with low torque place less load on the drive unit and mold, and the risk of failure or damage due to overload is low. On the other hand, since the processing force itself is weak, there are limits to the bending angle and width.
Frame length
Press brakes have a wide range of frame lengths, from small benchtop models to large industrial models, depending on the size of the part being machined and the application. The longer the frame length, the more large parts can be machined, but the more floor space is required for installation.Press brakes with long frame lengths can exceed 10 meters in length. This is often used for machining large parts or for machining many small parts at once.
The actual space for the machine must take into account not only the frame length of the machine, but also operating space, space for loading and unloading materials, and access space for maintenance.
For example, a press brake that is 10 meters long requires at least the length of the machine plus a few meters of width. Therefore, a total length of approximately 12 to 15 meters and a width of 4 to 6 meters is often required.
On the other hand, many short press brakes have a frame length of about 1 meter to 2 meters. These are suitable for machining relatively small parts and working within confined spaces.
Even with such a press brake, it is necessary to consider the operating space, loading/unloading of materials, and maintenance space. Overall, it is reasonable to estimate a length of at least 2-3 meters and a width of 3-4 meters in addition to the length of the machine.
Accuracy
The machining accuracy of press brakes is measured by how close the machined parts are to the required dimensions, angles, shapes, etc. shown in the blueprints and specifications.High processing precision means that the product has very small dimensional tolerances and high repeatability (the probability that the same result will be obtained when performing the same operation) is high. This refers to the ability to achieve tolerances of a few microns.
High machining accuracy has the following advantages:
Highly accurate press brake | Press brake with low precision | |
---|---|---|
Features | The dimensional tolerance of the product is very small, High repeatability (Tolerance of several microns) |
Small axis control press brakes generally range from 2 to 4 axes Y-axis (up and down of the beam) and X-axis (back before and after the gauge) |
Advantages | Manufactured parts are interchangeable Requires little or no adjustment during assembly Provides long-term reliability Reduced production of non-defective products Results in material and time savings |
For parts that do not require high machining accuracy Production costs can be lowered Production efficiency can be improved by increasing machining speed Machining No need to take advantage of material damage Easy to process with various materials |
Utilization industry examples | Aerospace parts High-precision automotive parts Medical equipment, etc. |
Architectural hardware Agricultural machinery General industrial products |
Number of control axes
The performance and flexibility of a press brake is largely determined by the number of control axes. The control axis is the axis that controls the movement of the press brake, including bending angle, depth, back gauge position adjustment, etc.The features of the multi-axis control press brake include the following:
Press brake with large number of axis control | Press brake with fewer axis controls | |
---|---|---|
Features | 10 or more axes. | |
Advantages | ||
Utilization industry examples |
Machining speed
The processing speed of a press brake is an important factor that greatly affects the machine’s capacity and productivity.This speed is determined by the speed at which the beam moves up and down, the time of the bending cycle, and the time it takes to handle and position the part.
Press brakes with high processing speed have the following characteristics.
Press brake with high processing speed | Press brake with slow processing speed | |
---|---|---|
Features | ||
Advantages | ||
Utilization industry examples |
5 manufacturers of press brakes
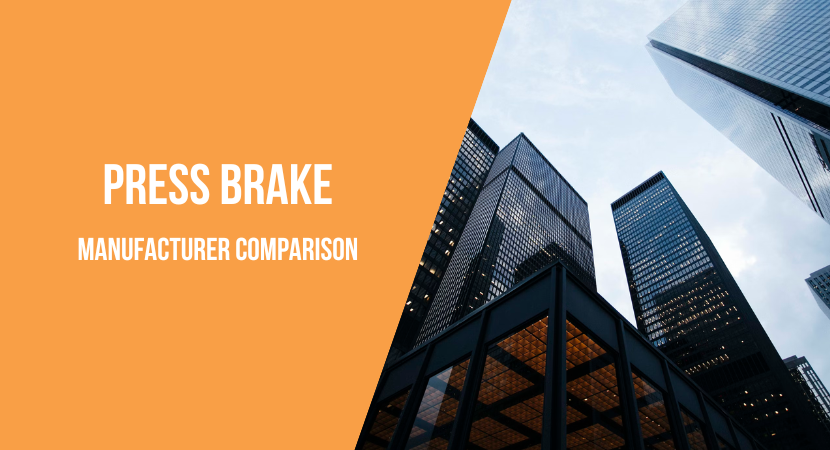
The following are the five representative companies that manufacture press brakes.
Mechanical Press brake |
Hydraulic type Press brake |
Servo motor type Press brake |
Hybrid type Press brake |
|
---|---|---|---|---|
Fuji Kiko | – | ✔ | – | – |
Amada | – | ✔ | ✔ | – |
Komatsu | ✔ | ✔ | ✔ | |
Murata Machinery | – | ✔ | ✔ | – |
Trumpf | – | ✔ | ✔ | – |
Contact JET Global
Fuji Kiko
Fuji Kiko was established as a subsidiary of Fujibo in 1944 as Fuji Weapons, and after the war it shifted to manufacturing automobile parts.Currently, they mainly manufacture and sell automotive parts such as steering columns and shifters.
The company primarily handles hydraulic press brakes, and supplies press brakes and molds to a variety of industries, including the automobile industry, construction machinery, agricultural machinery, and home appliances.
Amada
Amada, founded in 1946, is a comprehensive manufacturer of metal processing machinery.Currently, the company is developing various businesses such as sheet metal machines, cutting machines, grinding machines, press machines, precision welding machines, etc., and supports customers’ manufacturing.
Press brakes provided by Amada include hydraulic press brakes and servo-electric press brakes.
Additionally, Amada supplies press brakes and molds to a wide variety of industries, including automobiles, aircraft, architecture, infrastructure, medical care, and energy.
Komatsu
Since its founding in 1921, Komatsu has expanded its business worldwide as a comprehensive manufacturer of construction machinery, mining machinery, forestry machinery, industrial machinery, and more.Currently, they operate in a wide range of fields, including construction machinery and vehicles, utilities, forestry machinery, and industrial machinery, contributing to technological innovation.
Komatsu offers press brakes that utilize a variety of technologies, including mechanical, servo motor, and hybrid (hydraulic servo) types.
In addition, Komatsu contributes to the development of various industries by delivering press brakes and molds to a variety of industries, including automobiles, aircraft, architecture, infrastructure, medical care, and energy.
Murata Machinery
Murata Machinery has grown as a machine tool manufacturer since its founding in 1935. They are expanding their business into fields such as automobiles and communication equipment, with a focus on sheet metal processing machines such as turret punch presses, laser processing machines, and press brakes.The company handles hydraulic press brakes and servo motor press brakes, and its products are delivered to a variety of industries, including automotive, aerospace, construction, and machinery. This supports manufacturing in a wide range of fields.
Trumpf
Trumpf is a German machine tool manufacturer founded in 1923 that operates in a wide range of fields including laser technology, electric tools, and medical technology. Currently, they have offices in approximately 70 countries around the world and operate globally with approximately 14,000 employees.The press brakes handled by the company include hydraulic and servo motor types, and they use these technologies to provide high-quality products.
Trumpf supplies press brakes to cutting-edge companies in a variety of industries, including German auto parts manufacturer Heller and Italian aircraft manufacturer Alenia Aermacchi, leading the industry with its technological capabilities and reliability.
If you are unsure which company to contact, please reach out to us
Is the company really suitable for your goals? Are you choosing the right model? Please feel free to contact us if you have any concerns.We will consider the differences between each product and company and suggest the company that best suits your purpose.
Contact JET Global