However, SCARA robots have different characteristics depending on the product. This is why it is important to choose a proper machine that suits the purpose and site.
In this article, we will introduce the characteristics, price range, and structure of general SCARA robots, as well as the advantages and disadvantages of each type, selection criteria, and a list of major manufacturers.
Let us explain these robots better so that we may have a better understanding of what would be best suited for your business and its unique needs.
目次
What is a SCARA robot? Introducing features, mechanisms, and price range
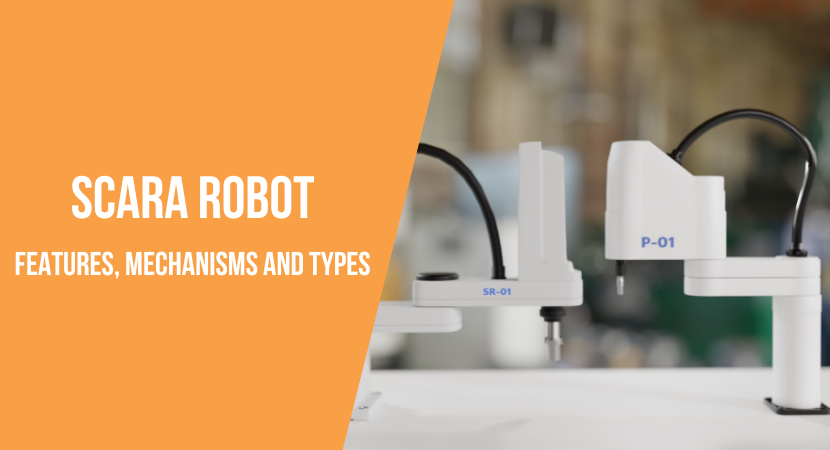
SCARA stands for Selective Compliance Assembly Robot Arm.
Let us now take a closer look at the basic features, mechanism, and price range of SCARA robots.
Basic features and mechanisms
SCARA robots excel in horizontal high-speed movement and vertical rigidity, making them ideal for automating precision processes including assembly, transportation, screw tightening, and coating. The main body of a SCARA robot comprises a total of 4 axes: 3 axes for horizontal movement (positioning) and 1 axis for vertical movement (pushing motion, etc.). Thanks to their simple structure, SCARA robots can be introduced at a relatively low cost.SCARA robots specialize in horizontal movement. The mechanism operates through a series of movements as outlined below:
- It horizontally moves the tip using 3 rotating axes, swiftly positioning it directly above the target.
- It utilizes the vertical axis to approach the object directly from above.
- It executes tasks such as grasping objects.
SCARA Robot Price Range
The price of a SCARA robot varies greatly depending on the type and performance, but it is usually priced at several thousand dollars.We can divide the price range into three categories:
SCARA Robot Price Range
Low Price Range: Approximately $12,000 – $36,000Type: Compact type, standard type
Reason for Price: This price is relatively low due to basic functions, suitability for small-scale jobs, and the use of relatively inexpensive parts and a simple design.
Medium Price Range: Approximately $36,000 – $78,000
Type: Standard type, special purpose type, high speed/high precision type
Reason for Price: Applications requiring high precision or specific functionality require more advanced technology and materials. This increase in precision and technology is reflected in the price.
High Price Range: $78,000 or more
Type: High speed/high precision type, high load type, special purpose model
Reason for Price: High performance, complex customization, advanced technology, specialty materials, and precise design required for advanced applications require higher costs.
So far, we have explained the basic features, mechanism, and price range of the SCARA robot. Next, we will explain the basic structure of the SCARA robot.
Basic structure of a SCARA robot
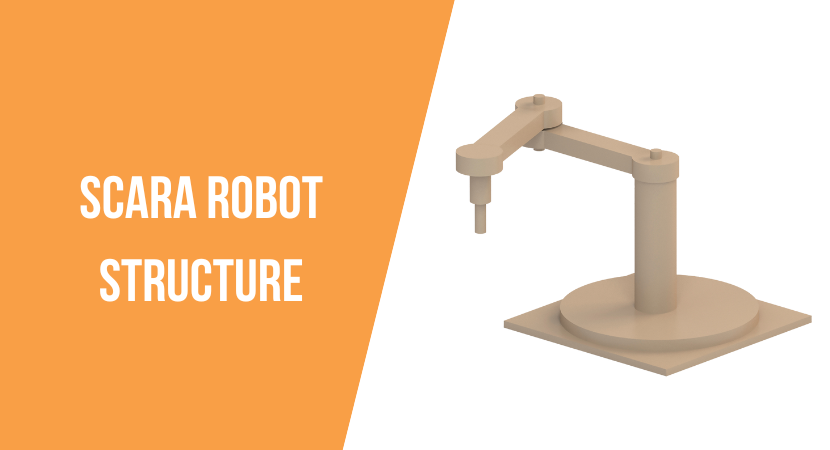
A SCARA robot generally consists of the following elements:
- Base
- Rotation axis
- Parallel arm
- Lift mechanism
- End effector
The functions of each part are as follows.
Base
The base is the most fundamental part, crucial for maintaining the stability of the entire robot. Built from strong, high quality materials, it minimizes the effects of vibrations and external forces during operation. The design emphasizes weight distribution and shape to ensure accurate and stable motion.Rotation Axis
The rotation axis is a vital component supporting the movement of the robot arm, attached to the base. This joint enables horizontal rotation and positioning. Driven by high-precision motors and gears, this joint allows for precise control, directly influencing the robot’s operating range and positioning accuracy.Parallel Arm
The parallel arm, typically consisting of two arms arranged in parallel, serves as the primary moving part of a SCARA robot. Precise pick-and-place operations are possible, as it is controlled by a rotating axis. Built using stiff lightweight materials, it enables fast and precise movement, with its length and structure determining the robot’s reach and working range.Lift Mechanism
The lift mechanism, situated at the arm’s tip, allows for vertical movement, making it easier for actions such as lifting and lowering objects. Various drive systems, such as pistons, provide precise control of force and speed, tailored to job requirements.End Effector
The end effector serves as the “hands” of the robot, equipped with interchangeable tools and devices for specific tasks. Some examples of end effectors that can be used are suction pads, chuck hands, electric screwdrivers, and dispensers. End effector selection and design can heavily depend on application requirements, significantly impacting work efficiency and accuracy.Now that we are familiar with the structure of a SCARA robot, we will review the four types of SCARA robot and explain the advantages and disadvantages of each.
What are the characteristics of each product? Advantages and disadvantages of four types of SCARA robots
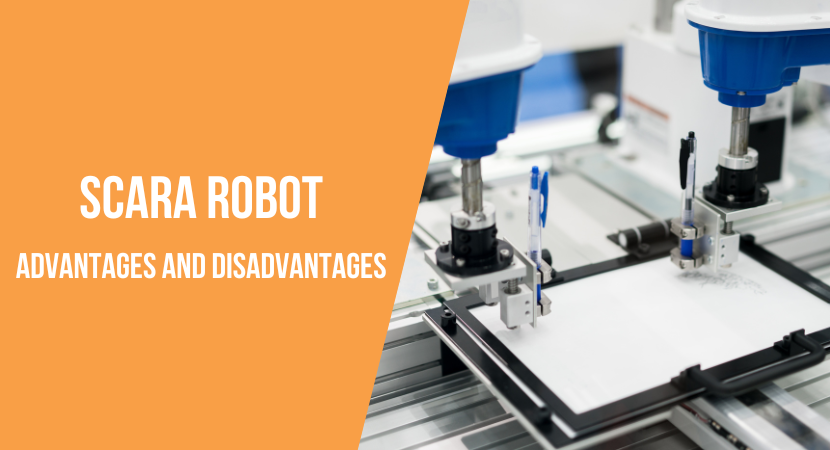
From here, we will explain the types of SCARA robots and the advantages and disadvantages of each. SCARA robots can be divided into the following four types of characteristic trends.
High durability type
High durability type SCARA robots are models designed to handle heavy parts. They have strong arms that are required to have a high load capacity and durability.Advantages
This stype of SCARA robot features a strong arm and high durability suitable for assembling and transporting heavy objects. They are particularly useful for manufacturing processes that require the handling of heavy objects, such as large automotive parts, metal industrial components, or construction materials.They also provide stable operation and long-term reliability, improving worker safety and significantly improving production efficiency by automating labor-intensive tasks.
Disadvantages
Because they are specialized in the ability to handle heavy objects, the size and cost of the machines themselves tend to be large. This means that they may only be applicable in large manufacturing facilities or certain work environments.They may not necessarily be optimal for applications that require high-speed, precise work. Additionally, their scope of application may be limited.
High speed/high precision type
These models are optimized for applications that require high-speed and precise work. They usually serve a rich lineup of high-speed, high-rigidity, and high-precision products.Advantages
They are especially suitable for assembling delicate electronic components and inspection work that requires a high degree of precision.The optimum acceleration/deceleration can be automatically set using the zone control function. As a result, you can significantly improve product quality and production efficiency. They are highly consistent and reliable in repetitive tasks and can meet the precision demands of manufacturing process automation.
Disadvantages
Technical requirements to achieve advanced performance tend to drive costs higher. For example, increased implementation costs can be a major barrier, especially for small and medium-sized enterprises that are sensitive to initial investments.Furthermore, these robots are not optimized for heavy-lift handling or tasks that cover large areas, and may have limited applicability.
Compact type
Compacy types are small models intended for use in limited spaces. There are also ultra-compact SCARA robots that are highly rigid and highly accurate, yet are palm-sized and inexpensive.Advantages
They greatly increase flexibility and efficiency on your product line, ideal for environments with limited space or handling small parts.Its low price also makes it an attractive option for companies looking to automate their manufacturing processes while keeping costs down.
Disadvantages
Their compact design has a limited working range and low load capacity. They are not suitable for applications that require handling of large parts or extensive work.Due to this design, compact SCARA robots are optimized for specific applications with specific needs.
Special purpose type
Special-purpose SCARA robots are designed specifically for specific industries and applications, such as hygienic models for the food industry.Advantages
They are customized for specific environments and requirements and optimized for performance under those working conditions. Customization allows robots to efficiently perform tasks that would be difficult for traditional robots to handle.For example, in order for a SCARA robot to start operating, it is necessary to align and adjust the position where the workpiece is set in advance. It is also possible to correct the position.
Disadvantages
They may not be flexible enough for other applications because they are designed for a specific application.It is important to consider that if choosing a special purpose type SCARA robot, there may be additional costs to accommodate special requirements, which may increase overall implementation costs.
So far, we have explained the characteristics, advantages and disadvantages of each SCARA robot. In the next chapter, we will explain six criteria for selecting the most suitable machine for your company. Please read on to understand the selection criteria for choosing the most appropriate SCARA robot for your company.
How to Choose a SCARA Robot | 6 Comparison Criteria
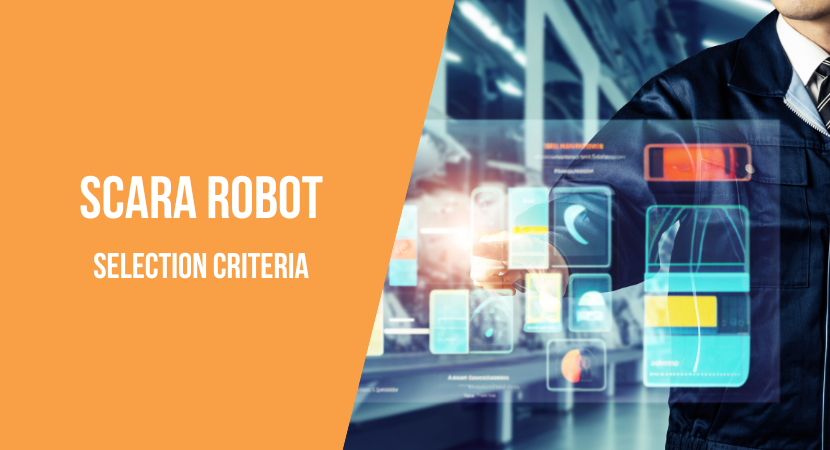
When investing in a SCARA machine, it’s essential to consider the following six points:
Work content/requirements definition
When considering the introduction of SCARA robots, the first thing to do is clarify the specific work content and process to be used. For example, in the case of assembly work, define in detail what parts need to be assembled and in what order.At this stage, it is important to consider the flow of work, the required speed of work, the type and size of the items being handled, and the working environment.
Once the work details are clear, the next step is to identify the required work precision. For tasks that require high precision, such as precise assembly, transportation of minute parts, and quality inspection, it is essential to select a SCARA robot that can achieve the necessary precision.
The required accuracy includes positioning accuracy, repeatability, and balance between speed and accuracy.
Total cost
Assessing the total cost of ownership is essential to determining economic viability. It is important to analyze both the initial investment and operating costs in detail and carefully evaluate whether the return on investment is worth the cost.In order to accurately evaluate the initial investment, it is necessary to comprehensively consider the cost of all equipment and services required for implementation. Initial investments include not only the price of the main unit, but also the cost of integrating ancillary equipment and systems, programming and operator training costs, and more.
Additionally, operating costs can vary greatly depending on the robot’s operating hours and usage conditions, so it is necessary to evaluate it based on a long-term operating plan.
Operating costs include energy consumption, regular maintenance costs, the cost of consumables and replacement parts, and the cost of software updates and system upgrades when necessary.
Payload capacity
It is important to consider the weight of the object that needs to be lifted and choose a SCARA robot with appropriate load capacity.As the payload changes, the type and number of workpieces that the robot can handle will change. For example, the higher the payload capacity, the more heavy workpieces or large numbers of workpieces can be transported at the same time.
In addition, the price and power consumption of the robot body also change depending on the payload capacity. Basically, the larger the payload capacity, the higher the price and power consumption of the main unit.
In addition to this, the payload also affects the robot’s operating speed and accuracy. The higher the payload capacity, the lower the operating speed and accuracy may be.
Reach/work range
It is important to choose a robot with the reach (arm length) that can cover the required work area.As the work range changes, the size and shape of the workpieces that the robot can handle will change. The larger the travel range, the more you can handle large and complex workpieces.
On the other hand, the larger the work area, the larger the size and weight of the main body, which affects the speed and accuracy of the operation. It also requires more space and requires more safety measures.
Installation location
The expected installation location will change depending on changes in payload, etc. The following is the expected installation location based on the payload. Please use this as a reference if you have limited installation space.Payload capacity and installation location
- Payload capacity: 1-5kg Suitable for small spaces such as desktops and benchtops
- Payload capacity: 5-10kg Can be installed relatively flexibly in not-so-wide spaces, such as by placing it on the floor or hanging it from the ceiling.
- Payload capacity: 10-20kg Suitable for large spaces, such as by placing on the floor or hanging from the ceiling.
Speed/repetition accuracy
It is important to consider production efficiency and select a robot that meets the speed required to perform the work. To ensure the quality of the product, it is a good idea to check that it has the required repeatability.Variations in speed change the workpiece cycle time that the robot can handle. If you choose the highest speed, the workpiece can be transported and processed much faster.
On the other hand, this has an impact on the price and power consumption of the robot itself. The faster the speed, the higher the price and power consumption of the device.
Speed is also connected to the accuracy and safety of a robot’s movements. This is because the higher the movement speed, the lower the accuracy and safety of movement tend to be. Be sure to check the repeatability (stopping accuracy) and any errors.
These are the six criteria for selecting a SCARA robot. In the next chapter, we will introduce a list of manufacturers that manufacture SCARA robots. Read on to find out which manufacturer is right for your company.
5 major manufacturers of SCARA robots
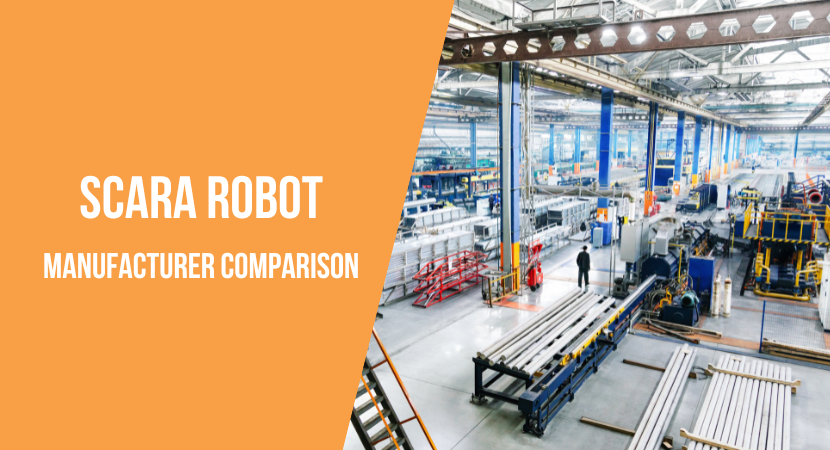
From here, we will introduce the major companies that manufacture SCARA robots. After sorting out your company’s introduction requirements and checking the six comparison criteria, it’s time to look for a company that actually manufactures SCARA robots.
5 representative SCARA robot companies
High durability type | High speed/high precision type | Compact type | Special purpose type | |
---|---|---|---|---|
Epson | – | ✔ | – | – |
Yamaha Motor | – | ✔ | – | ✔ |
IAI | – | ✔ | ✔ | – |
DENSO WAVE | – | ✔ | ✔ | – |
FANUC | ✔ | – | – | ✔ |
Contact JET Global
Epson
Epson is a global company known for high-quality printing solutions based on precision processing technology, and is highly regarded as a pioneer in the field of industrial robots, especially SCARA robot technology.The types of SCARA robots that Epson handles are mainly high-precision, high-speed types. These robots combine extremely delicate movements and high speeds, making them the perfect solution for precision assembly tasks in manufacturing and advanced quality inspection processes.
The strength of Epson’s SCARA robot is its unique efficient design and excellent repeatability. This allows maximum productivity even in limited space and ensures stable operation over long periods of time.
Epson’s SCARA robots demonstrate their full potential, especially in work environments that require high precision.
Yamaha Motor
Yamaha Motor boasts high technological capabilities and a proven track record in the field of industrial robots. It offers a wide variety of robots, including cartridge robots and single-axis robots in addition to SCARA robots.Yamaha Motor handles SCARA robots in the above categories: high-speed, high-precision types, and special-use types.
The strength of Yamaha Motor’s SCARA robots lies in high speed, high rigidity, high precision, and a rich lineup. Thanks to its superior technology and functions, it has high maintainability, durability, and reliability. Yamaha Motor’s SCARA robots are backed by 30 years of history and achievements.
Yamaha Motor’s SCARA robots contribute to the automation of screw tightening, soldering, transportation, loading, inspection processes, etc. SCARA robots with clean room specifications are also used in semiconductor manufacturing factories and food, medical equipment, and cosmetics manufacturing sites.
IAI
IAI is a specialized manufacturer of industrial robots founded in 1976. Their main products are electric actuators and SCARA robots, and they have sales and service bases around the world.IAI handles high-speed, high-precision, and compact SCARA robots.
The strength of IAI’s SCARA robot is that it achieves top-level speed, high portability, and high accuracy. Additionally, it is equipped with a battery-less absolute encoder as standard, eliminating the need for battery replacement and contributing to a reduction in maintenance man-hours.
IAI delivers SCARA robots to a wide range of industries, including food, medical care, cosmetics, electronics/electricity, and automobiles.
Denso Wave
DENSO WAVE is a leading company that develops and manufactures automatic recognition devices such as barcodes, QR codes, and RFID, and industrial robots (FA equipment). As a member of the DENSO Group, they provide innovative technology in various fields including the automobile industry.DENSO WAVE handles high-speed, high-precision, and compact SCARA robots.
DENSO WAVE’s strength is that it guarantees high quality and performance because it develops and manufactures SCARA robots based on the automotive industry’s strict quality standards. They also provide advanced technologies and solutions, such as COBOTTA, a SCARA robot that can work in collaboration with humans.
DENSO WAVE has a record of delivering SCARA robots to a wide range of industries, including automobiles, electronics/electricity, food, and pharmaceuticals.
Fanuc
FANUC is a global manufacturer of CNC (computer numerical control) systems for machine tools, robots, and robot machines. In particular, in the field of robots, they lead the industry with their wide product lineup and innovative technology.The SCARA robots provided by FANUC are classified into high durability types and special purpose types. Rhey have a high load capacity and excellent durability, making them ideal for transporting heavy parts and assembly work. They also carry washable models that meet hygiene standards for the food industry.
FANUC’s strength lies in its high reliability and applicability to a wide range of industries. In addition, advanced control technology and a wealth of functions enable work automation and efficiency. FANUC also offers customer support and technical services, providing full support from installation to operation and maintenance.
They have experience delivering products to multiple industries, including the automotive industry, electronics manufacturing, food processing, and pharmaceutical manufacturing.
Consider Introducing SCARA Robots to Improve Your Production Line
SCARA robots achieve high-speed, high-precision movement and automate delicate tasks such as product assembly and quality inspection. As a result, you can significantly increase productivity and reduce operating costs, accelerating your business growth.There are several types of SCARA robots, so please consider installing a machine that suits your company’s purposes and use it to improve the efficiency of your production line.
Is the company really suitable for your business? Are you choosing the right model? Please feel free to contact us if you have any concerns.
We will consider the differences between each product and company and suggest the company that best suits your unique requirements.
Contact JET Global