この記事では、研削盤の種類とそれぞれの特徴、メリットや比較方法について詳しく解説します。
目次
7種類の研削盤
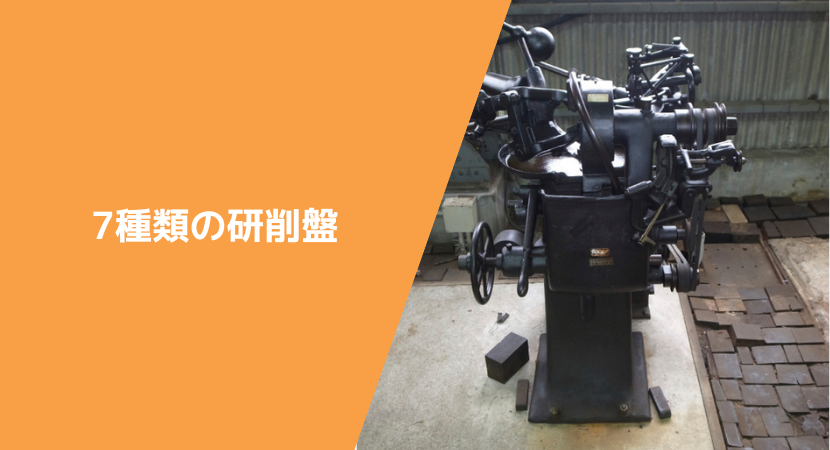
研削盤とは、高速で回転する砥石をワークに当てて、表面を削り取ったり、仕上げたりする工作機械のことです。研削盤は、硬度が高いものでも加工が可能かつ、精度が高くて表面をキレイに仕上げられるのが特徴です。
研削盤は、大きく分けると以下の7種類があります。
- 平面研削盤
- 円筒研削盤
- 内面研削盤
- センタレス研削盤
- プロファイル研削盤
- ネジ研削盤
- 工具研削盤
平面研削盤
平面研削盤とは、高速で回転する砥石をワークに当てて、表面を削り取ったり、仕上げたりする工作機械です。砥石の回転方向や動かし方、ワークを固定するテーブルの形状や動かし方によって、さまざまな種類があります。寸法精度や面粗さを要求される平面の研削に最適な加工法です。平面研削盤の強みは、以下のとおりです。
- 硬度が高いものでも加工が可能かつ、精度が高くて表面をキレイに仕上げられる
- 砥石のあて方によって様々な研削に対応できるため、応用性が高い
- 砥石の自生作用により、切れ味が悪くなりにくく、砥石の交換頻度が低い
平行度が求められる機械部品や半導体ウエハなどの加工に使われることが多いです。
円筒研削盤
円筒研削盤とは、高速で回転する砥石を円筒状のワークの外面に当てて、表面を削り取ったり、仕上げたりする工作機械です。砥石とワークの両方を回転させて研削することで、高い精度や面粗さを実現できます。砥石のあて方によって、トラバース研削、プランジ研削、アンギュラ研削という3種類の研削方法があります。円筒研削盤の強みは、以下のとおりです。
- センタレス研削盤に比べて、ワークの両端をセンターで支持することで、高い加工精度や真円度を得られる
- ワークの外周に溝や穴があっても加工できるため、汎用性が高い
- アンギュラ研削によって、ワークの外周面と端面を同時に仕上げることができるため、生産性が高い
円筒状のワークの外面を研削する工作機械で、自動車シャフトや軸部品などの仕上げに使われます。
内面研削盤
内面研削盤とは、円筒形状の工作物の内面を加工する機械です。研削加工は、硬い砥粒を結合剤で固めた砥石を用いて材料を削る加工方法を指します。内面研削盤は精密加工に適した機械で、寸法精度や仕上げ面の荒さが良いため、焼き入れ鋼のような硬い材質を削ることが可能です。内面研削盤の強みは、以下のとおりです。
- 砥石の直径を工作物の内径に合わせることで、さまざまな内径に対応できる
- 工作物の形状やサイズに応じて最適な研削方式を選択できる
- 砥石の状態を常に最適に保つことで、高品質な研削を実現できる
寸法精度や仕上げ面の荒さが良いことから、精密加工に適しています。
センタレス研削盤
センタレス研削盤とは、丸い筒状の対象物(ワーク)の外側の面を削って滑らかに加工する機械です。通常、研削する際はワークの真ん中に穴をあけて空洞にし、その間に支えとなる軸を差し込むことで固定します。しかし、センタレス研削盤はその名の通りセンタ支持は行わず、固定されたブレード・研削砥石・調整砥石(調整車)でワークを支持します。センタレス研削盤の強みは、以下のとおりです。
- 研削抵抗によるたわみの影響が少ない
- センター穴の加工が不要
- 量産加工に最適
長尺や小径のワークに対して高い真円度や直線度を得られるため、軸やピンなどの部品に適しています。また、ワークの供給や排出が容易なので、大量生産に向いています。
プロファイル研削盤
プロファイル研削盤とは、精密な金型部品加工に適している加工方法で、投影機で拡大された製品図を用いて素材の外形を砥石でなぞるように研削する機械です。プロファイル研削盤の強みは、以下のとおりです。
- 高精度が求められる加工に対応できる
- 寸法精度や面粗さはもちろん、幾何公差ではほとんどの幾何公差に対応することができる
- 小物で複雑な形状や細溝・狭ピッチ・極小等の金属部品の加工も可能
高精度で複雑な形状の部品を少量加工するのに適しています。
ネジ研削盤
ネジ研削盤とは、ねじの表面を砥石で研削する工作機械です。精密ボールねじなど、高精度が要求されるねじ製品の加工に不可欠な機械です。ネジ研削盤の強みは、以下のとおりです。
- 切削や電着砥石に比べて、砥石のコストが低い
- 砥石の成形にNC制御を用いることで、自由な形状のねじを加工できる
- 重研削が可能で、切削並みの能率で加工できる
- 研削によって、高い寸法精度や表面粗さを実現できる
雄ねじや雌ねじ、ボールねじなどの特殊な形状のねじを加工する場合に適しています。
工具研削盤
工具研削盤とは、一定量の切削に使用し切れ味が悪くなった切削工具に再度研削を施し、切れ味を復活させるための機械です。工具研削盤はグラインダーとも呼ばれます。また、この場合の切削工具にはドリルやエンドミル、フライスカッターやホブカッターなどがあります。工具研削盤の強みは、以下のとおりです。
- 使用した工具を再研削することで、工具の寿命を延ばし、コストを削減できる
- 再研削だけでなく工具の製造にも利用できる
切削工具の再研削や製造に特化した機械で、それ以外の用途には適しません。
研削盤を活用するメリット・デメリット
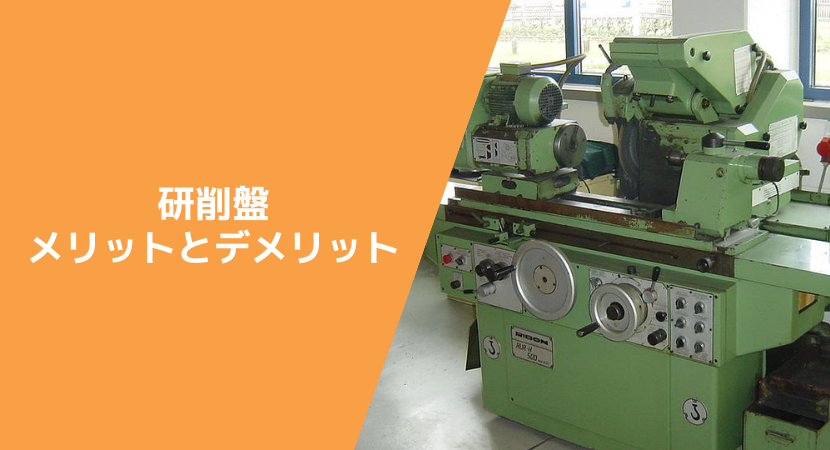
研削盤を導入する際は、メリットだけではなくデメリットも考慮する必要があります。このセクションでは、研削盤を導入するメリットとデメリットをご紹介します。
メリット
研削盤を導入するメリットには、以下のポイントが挙げられます。- 硬い素材や焼入れされた部品も加工可能
- 高い寸法精度
- 切れ味が良い
硬い素材や焼入れされた部品も加工可能
研削盤は、特に、硬い素材や焼入れされた部品の加工で活躍します。砥石の高速回転によって素材の表面を削り取ることで、ミクロン単位の精度での加工が可能です。このため、他の加工方法では難しい高硬度材料の精密加工が実現できます。そのため、以下のような場面で活躍することが多いです。
- 自動車産業のエンジン部品の加工:非常に硬い素材の加工が必要なエンジン内部の部品
- 工具製造における切削工具の製造と再研磨:高速で硬い材料を削る必要がある
高い寸法精度
研削盤は、非常に高い寸法精度を実現する工作機械です。ミクロン単位での誤差が許容範囲内に収まることを意味し、この精度は製品の品質と性能に直結します。そのため、特に精密な部品が要求される分野で研削盤は不可欠です。以下のような場面で活躍しています。
- 航空宇宙産業における精密部品の製造:タービンブレードやエンジン部品など、高温や高圧にさらされる部品の製造において高い寸法精度を保証
- 半導体製造におけるシリコンウエハの加工:ウエハの表面を高精度に研削し、半導体デバイスの性能を向上
切れ味が良い
研削盤は、素材を高精度で削ることができるため、加工後の製品や工具の「切れ味」が非常に良くなります。研削盤が砥石の回転を利用して表面を均一に削り取ることで、滑らかな仕上がりを実現するためです。この切れ味の良さは、特に刃物や工具の製造において重要な要素となります。そのため、以下のような場面で活躍しています。
- 精密刃物の製造:包丁やカミソリなどの刃先を精密に研ぐことで鋭い切れ味を実現
- 切削工具の製造および再研磨:ドリルビットやエンドミルなどの刃先を鋭く研磨することで、切削抵抗を減少させ、工具の寿命を延ばす
デメリット
一方で、研削盤には以下のようなデメリットもあります。- 加工時間が長い
- 熱によるワークの変形やヤケが発生しやすい
- 砥石の摩耗やドレスが必要
加工時間が長い
研削盤は、加工に時間がかかるというデメリットがあります。これは、素材を少しずつ削り取る必要があるためであり、特に大きな部品や複雑な形状の加工には時間がかかります。このデメリットを軽減するには、以下のような手段が挙げられます。
- 高効率の砥石を使用する:最新の高効率の砥石を使用することで、研削速度を向上させる
- 複数工程の一括加工:複数の研削工程を一度に行うことで加工効率向上
熱によるワークの変形やヤケが発生しやすい
研削盤を使用する際、砥石が高速で回転し、ワーク(加工対象物)に対して強い摩擦が生じるため、熱が発生します。この熱がワークに蓄積されると、材料の変形や「ヤケ」(熱変色)を引き起こし、製品の精度や品質に悪影響を与える可能性があります。これらの問題を防ぐためには、適切な対策が必要です。このデメリットを軽減する手段は以下の通りです。
- 冷却液の適切な使用:冷却液(クーラント)を適切に使用することで、熱の発生を抑え、ワークの温度上昇を防ぐ
- インターバル加工と低速加工:インターバルを取りながら加工を行うことで熱の蓄積を防ぐ
砥石の摩耗やドレスが必要
研削盤を使用する際、砥石は加工を繰り返すことで徐々に摩耗し、形状や切削性能が劣化していきます。このため、砥石の摩耗を補正するためのドレス(修整)が定期的に必要になります。ドレスは砥石の切削性能を維持し、加工精度を保つために重要ですが、頻繁なドレス作業は生産性を低下させる要因となります。このデメリットを軽減するためには、以下のような対策が挙げられます。
- 高耐久性の砥石を使用する:砥石の素材や構造を工夫することで、摩耗を抑え、ドレスの頻度を削減
- 自動ドレッシング装置の導入:ドレス作業の手間を減らし、生産性を向上
4つの比較基準 | 研削盤の選び方
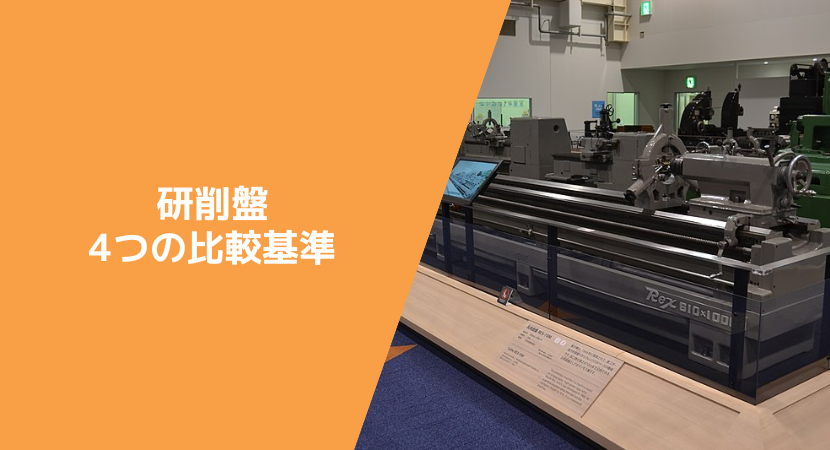
研削盤を比較する際には、以下の4つのポイントを抑える必要があります。
- テーブルの大きさ
- 砥石の寸法
- 砥石の回転数
- 送り量
テーブルの大きさ
研削盤を選定する際は、研削する素材の大きさに合わせて選択する必要があります。テーブルの大きさが変わると、研削できる素材の大きさや形状、研削範囲、研削精度などが変わります。大きなテーブルの場合、大きな素材や複雑な形状の素材が研削可能になるため、加工できる素材の大きさの幅が生まれます。
一方で、テーブルが小さいと、機械の価格や設置スペースが小さくなり、テーブルの移動が速くなります。
砥石の寸法
砥石の寸法は、外径×厚み×孔径の順序で表示されます。砥石の寸法が変わると、研削できる素材の大きさや形状、研削速度や精度、砥石の寿命や摩耗などが変わります。大きな砥石の場合、大きな素材や複雑な形状の素材を研削できるため、研削速度が速くなります。
一方で、小さな砥石の場合、砥石の価格や重量が低くなり、砥石の摩耗が少なくなるため、小さな素材や単純な形状の素材しか研削できず、研削速度が遅くなります。
砥石の回転数
砥石の回転数は、砥石の周速度と密接に関係しています。砥石の周速度とは、砥石の外周で1点が1分間に進む距離のことです。砥石の回転数が変わると、砥石の周速度も変わります。砥石の周速度は研削抵抗や砥石の摩耗、研削速度や精度、砥石の表面温度などに影響します。砥石の回転数が多いと、研削速度が速くなり、研削時間が短くなるメリットがあります。また、砥石の摩耗が少なくなり、砥石の寿命が長くなるほか、砥石の表面温度が低くなり、砥石や素材に熱ダメージを与えません。
一方で、回転数が低い場合、研削速度が遅くなり、研削時間が長くなります。
送り量
送り量とは、砥石が素材に切り込む量のことです。送り量が変わると、研削抵抗や砥石の摩耗、研削速度や精度、砥石の表面温度などが変わります。送り量が大きい場合、以下のような利点があります。
- 研削速度が速くなり、研削時間が短くなる
- 砥石の摩耗が少なくなり、砥石の寿命が長くなる
- 砥石の表面温度が低くなり、砥石や素材に熱ダメージを与えない
一方で、送り量が小さい場合、研削速度が遅くなり、研削時間が長くなります。
研削盤を製造するメーカー5社
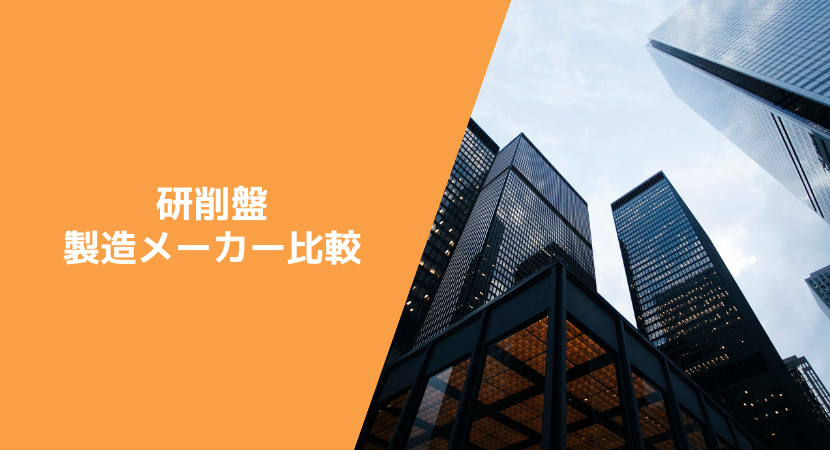
研削盤を製造する主なメーカーには、以下の5社が挙げられます。
- アマダマシナリー
- オークマ
- 岡本工作機械製作所
- ジェイテクト
- ニデックマシンツール
アマダマシナリー
アマダマシナリーは、1946年に創業した切削機械・研削盤・鋼材切断用レーザ機械の開発・製造・販売・サービスを行う企業です。アマダグループの一員として、切削・研削盤・鋼材切断用レーザ機械の製品・製品の修理・復旧・企業活動についてのお問い合わせ窓口も提供しています。同社は、プロファイル研削盤、円筒研削盤、平面研削盤を扱っています。
オークマ
オークマは、日本の工作機械メーカーで、1918年に設立しました。オークマは、NC旋盤、マシニングセンタ、複合加工機、研削盤などの工作機械や、独自のCNC装置(OSP)や自動化システムなどの製品を提供しています。同社は、内面研削盤、円筒研削盤、プロファイル研削盤を扱っています。
岡本工作機械製作所
岡本工作機械製作所は、群馬県安中市に本社を置く研削盤を主とした工作機械、半導体関連装置を製造する工作機械メーカーです。「技術は正しく」をモットーに、品質的な精度はもちろん、お客様が求めるものの、その先を創造することを目指しています。同社は、平面研削盤、円筒研削盤、内面研削盤を扱っています。
ジェイテクト
ジェイテクトが扱っている研削盤は、円筒研削盤、センタレス研削盤、内面研削盤、プロファイル研削盤です。ジェイテクトの研削盤は、ジェイテクトグループの技術を用いたシナジー効果で、同一工作物で異なる径の同時研削ができる広幅円筒研削盤や、立形複合研削盤などの革新的な製品を開発しています。また、自動化、生産性向上、工程集約、難削材加工、簡単操作、エコノミーなどの課題に応えるソリューションを提供しています。
ニデックマシンツール
ニデックマシンツールは、2021年に日本電産グループの一員となった工作機械メーカーです。工作機械、切削工具、金属3Dプリンタなどの設計・製造・販売・コンサルティング・アフターサービスを行っています。滋賀県栗東市に本社を置き、国内外に多数の拠点を展開しています。同社は、円筒研削盤、平面研削盤を扱っています。