また、選び方の基準や各機種の比較、さらに信頼できるメーカーもご紹介。初めてのプレス機選びで失敗しないためのポイントを押さえ、最適な機械を見つけるお手伝いをします。
目次
5種類のプレス機と特徴
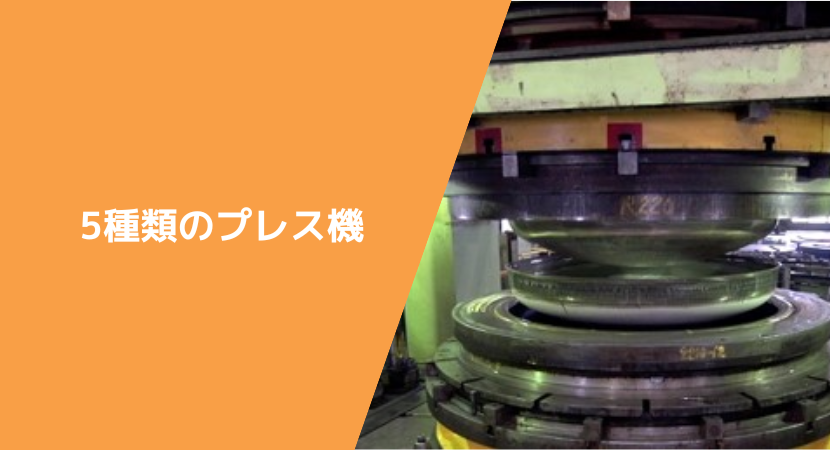
プレス機とは、2個以上の対をなす金型を使い、加工対象物(ワーク)に対して圧力をかけて加工を行う機械です。板金機械、鍛圧機械と呼ぶこともあります。
プレス機には、主に以下の5つの種類があります。
- 機械式プレス
- 液圧式プレス
- 空圧式プレス
- サーボ式プレス
- 人力プレス
機械式プレス
機械式プレスは、モーターの回転運動を利用して、金属などの材料に対して高精度かつ強力な圧力をかけ、成形、切断、穴あけなどを行う産業機械です。一定の圧力量と運動パターンにより、一貫した加工品質が得られ、様々な産業で広く利用されています。- 一貫した加工精度が得られるため、量産に最適
- 駆動方式やフレーム形式の多様性により、用途に応じた選択が可能
- 構造が比較的シンプルで、メンテナンスが容易
機械式プレスは、自動車製造工場で車体パネルの成形やシャーシ部品の打ち抜きに利用され、これにより大量生産が可能となり、自動車の製造コスト削減に貢献しています。また、家電製造業でも広く使用されており、冷蔵庫や洗濯機などの部品成形において、薄い金属板の高精度な加工が求められる場面で活躍しています。
さらに、建築資材の製造においても、金属の切断や成形を行うことで、高強度な建築用部材を効率的に生産し、建築現場での品質と信頼性の向上に寄与しています。
液圧式プレス
液圧式プレスは、油圧シリンダーを利用してスライドを上下させ、金属などの材料を加圧成形する装置です。機械式プレスに比べて、ストロークの長さが調整しやすく、精密な圧力制御が可能であるため、深絞り加工や複雑な形状の成形に適しています。液圧式プレスは、安定した加圧力と操作性の良さから、多くの製造現場で利用されています。- 加圧力とストロークの長さが容易に調整可能
- 深絞り加工に優れており、複雑な形状の成形が可能
- 過負荷時には安全装置が作動しやすい
液圧式プレスは、自動車産業においてボディ部品の深絞り加工に多用され、複雑な形状のパネルや部品の成形が可能です。また、航空機製造でも利用されており、軽量で強度のある部品の製造に適しています。さらに、家電製造においても、薄い金属を使用した外装や内部パーツの成形に広く活用されています。
空圧式プレス(エアプレス)
空圧式プレスは、圧縮空気を動力源としてラムを動作させ、圧入、カシメ、曲げ、成形などの加工を行う装置です。軽量で構造がシンプルなため、取り扱いやメンテナンスが容易です。さらに、動作スピードが速く、静穏性にも優れているため、効率的な作業が求められる場面で活躍します。- 動作が速く、効率的な加工が可能
- 軽量で、取り扱いやメンテナンスが容易
- 静穏性があり、騒音対策がしやすい
空圧式プレスは、電子機器の部品製造において、カシメや刻印などの精密な加工に利用されます。また、自動車部品の軽量素材の曲げ加工にも適しており、速やかな作業を実現します。さらに、日用品の製造現場でも、小型部品の成形や圧入に使用され、効率的な生産をサポートします。
サーボ式プレス
サーボ式プレスは、サーボモーターとメカニカル駆動機構の組み合わせにより、高精度な成形と生産性の向上を実現するプレス機です。機械プレスと油圧プレスの長所を兼ね備え、幅広い製造分野で活用されています。このタイプのプレス機には、以下の特徴があります。
- サーボモーターによる高精度・高機能な制御
- 機械プレスと油圧プレスの長所を兼備えたハイブリッド設計
- 省エネルギーと低騒音設計により、環境負荷を低減
サーボ式プレスは、例えば自動車産業で、部品の高精度加工に最適な選択としてサーボ式プレスが広く利用されています。また、省エネルギーを重視する製造現場でも、その効率性が評価され、導入が進んでいます。
人力プレス
人力プレスは、足踏みや手動レバー操作で力を加える簡易的なプレス機です。昔の町工場で広く使用されていましたが、精度や動力面での限界から、現在ではほとんど使用されていません。このタイプのプレス機には、以下の特徴があります。
- 手動操作による簡単な構造
- 動力不要のため設置が容易
- 精度が低く、動力不足による限界がある
人力プレスは、昔の町工場では、小規模な金属加工や板金作業に利用されていました。また、動力が利用できない環境下での簡易的な作業にも適していました。
6つの選定基準 | プレス機の選び方
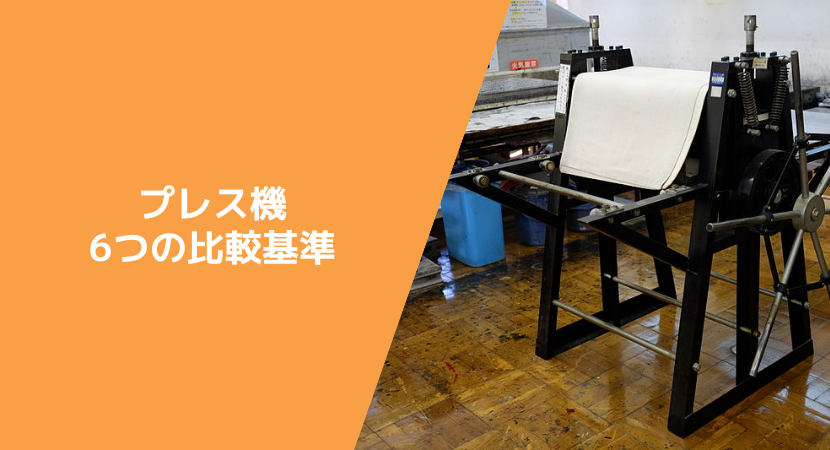
プレス機を選定する際には、以下の6つの観点を考慮することがおすすめです。
- 使用用途
- 生産能力
- プレス出力、必要圧力能力
- 製品精度
- 盤面サイズ
- ストローク長
使用用途
用途に応じて、機能性から選定する必要があります。以下に、各種類のプレス機に適している用途を一部ご紹介します。適した用途 | 業界活用事例 | |
---|---|---|
機械式プレス | 抜き加工、曲げ加工、絞り加工など | 自動車産業、電機部品産業など |
液圧式プレス | 深絞り加工、複雑な形状の成形 | 軍事、自動車、電気製品など |
空圧式プレス | 圧入、カシメ、刻印など | 部品製造など |
サーボ式プレス | 高精度な加工が必要な製品 | 自動車産業など |
人力プレス | – | 生産量が少なくて済む町工場など |
生産能力
必要とする生産能力や予算によってプレス機の生産能力を決定します。製品形状、材料等の特性を考慮しながら最適な加工法を選定する必要があります。以下にて、小規模生産に適しているプレス機と大規模生産に適しているプレス機をそれぞれ記載いたします。
小規模な生産におすすめのプレス機
- 手動プレス機(ハンドプレス):ハンドルやレバーを手動で操作して、局所的に圧力をかけてプレス
- 機械式プレス機:クランク式プレス機は、小バッチ生産や研究実験用途に最適
大量生産におすすめのプレス機
- 順送プレス:小さい製品向きで、複数の工程を単一の金型一面で利用
- トランスファープレス:大きい製品向きで、一台のプレス機械に、複数の独立した金型を取り付けて使用
プレス出力、必要圧力能力
プレス加工の内容に合わせ、余裕を持った圧力能力(kN)を選定します。計算値の1.5倍以上で選ぶことをおすすめします。製品1cm²に50㎏のプレス力が必要で、30㎝×30㎝の製品を作りたい場合に、30㎝×30㎝×50㎏=45000㎏=45tのプレス出力が必要です。
製品精度
プレス機を選定する際には、加工品の品質や金型の寿命に直結する精度が重要な要素です。精度には、負荷がかかっていない状態での静的精度と、実際に加工が行われているときの動的精度があり、どちらも高い精度を維持することが、安定した生産とコスト効率の向上に寄与します。選定時には、使用目的や加工内容に応じて、必要な精度を見極めることが必要です。静的精度とは、プレス機に負荷がかかっていない状態での機械の精度を指します。具体的には、ボルスター上面とスライド下面の平面度や、これらの間の平行度、スライド上下運動の直角度などが含まれます。この精度は、プレス機の基本的な性能を示すものであり、加工の一貫性や金型の寿命に大きな影響を与えます。
静的精度を考慮すべき理由は、以下の通りです。
- 加工品の精度を安定させるために必要
- 金型の摩耗を減らし、寿命を延ばすことが可能
- 長期間の安定稼働を実現し、メンテナンス頻度を低減
動的精度とは、プレス機が実際に稼働し、材料に対して加工が行われているときの精度を指します。機械が動作している際のフレームの剛性や、スライドの挙動が影響するため、負荷や振動の影響を受けやすくなります。動的精度は、特に高精度な加工を行う場合に重要で、加工のばらつきを最小限に抑えるために不可欠です。
動的精度を考慮すべき理由は、以下の通りです。
- 加工中の寸法変動を抑え、高品質な製品を生産するため
- 高速加工時でも精度を維持し、生産効率を向上させる
- 機械全体の剛性を保ち、長期間にわたる安定運転を実現する
盤面サイズ
金型の寸法に合わせて選定する必要があります。金型が収まるように、使用予定の最も大きい金型よりも、少し大きめのものを選定する必要があります。ストローク長
絞り加工において注意が必要な項目です。一行程でスライドが動く距離は、フランジのある製品の加工において、製品高さの2.5倍〜3倍程度が最低でも必要です。順送り加工やトランスファー加工において、自動加工をする際には製品高さの3倍〜4倍が最低でも必要です。できれば4倍以上の長さを確保することをおすすめします。
製品取り出しや材料送り等との関係と同時に、加工力も確認する必要があります。トルク能力曲線を超えないよう選定します。
オープンハイライト(デーライト)を決める
上盤面と下盤面が一番開いたときの距離については、金型の厚み、材料投入時の厚みに必要なスペースなどを考慮して選定します。シリンダーストロークを決める
ストローク250mm、オープンハイト250mmの場合は何も挟まなくても加圧することができます。ストロークが200mmの場合には、金型の厚みが50mm以上必要です。プレス機を設置する上で考慮する必要があること
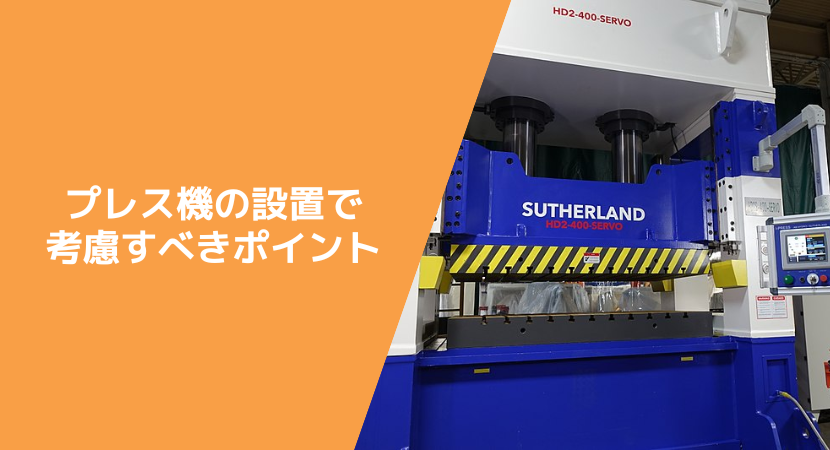
プレス機を設置する際には、以下の2点において注意が必要です。
- 安全対策
- 設置環境
安全対策
プレス機を使用する業界では、「指1本を落とさなければ一人前ではない」と言われるほど事故が多発していました。そこで、昭和30年代から本格的に安全対策が始まりましたが、いまだにプレス機における事故は労災事故の中でも多く見られます。安全対策に関する法令については、以下のボタンよりご確認ください。
場合により、身体の欠損や死亡につながる重大事故が起こることもあります。ほとんどの年で、数名がプレス機械での死亡事故が発生しており深刻な問題です。厚生労働省が公開している「労働災害事例」では、以下の例などが取り上げられています。
- プレスの金型に挟まれ死亡
- 右手を挟んだ状態で軌道ペダルを踏み右手を切断
- 供給材料位置を修正した際にプレス機に挟まれ怪我
プレスの金型に挟まれ死亡
事業場規模は5〜15人の現場でした。うち1人が、動力プレス機器を使用し金属加工作業をした際の事故で、亡くなっています。防護・安全装置が不完全であることを要因として、プレスの金型に挟まれました。事故当日は、作業者AとBが実施していました。動力プレスには、前面と後面の両方に光線式安全装置が取り付けられていましたが、安全装置が故障しており、全面の安全装置のみが作動していました。
そのため、Bが作業において後面へ回った際に、光線式安全装置によるAの検知ができず、動き出した金型に挟まれたとされています。
右手を挟んだ状態で軌道ペダルを踏み右手を切断
事業場規模は16〜29人の現場でした。経験1ヶ月の派遣作業員が、パソコンデスク昇降部レールの曲げ作業中に、プレス機内部に手を差し込んだ状態で、起動ペダルを踏んだため起きた事故です。作動したプレスにより、右手首を切断してしまい、休業しています。プレス機作動時に右手を入れたことも問題ですが、安全作業手順を熟知していなかったことも課題です。
ソフト面での対策は不十分であり、作業ゾーンに手を入れた場合に設備を停止する「インターロック機構」を設置することが対策につながります。
供給材料位置を修正した際にプレス機に挟まれ怪我
事業場規模は100〜299人の現場でした。自動プレス機(ホットプレス機)の運転をしている際、パネルが所定の位置に供給されず、光電センサーの検知によって停止しました。材料の位置を修正する際、ホットプレス機の周辺にある柵をこえてローダーとプレス機の間に立ち入ったことで、センサーによる停止が解除され、再起動されました。
可動式の遮熱板が上昇したことで遮熱板に持ち上げられ、電気配管と遮熱板の上端に挟まれ、休業しています。
設置環境
プレス機を設置する際には、以下の点に注意することをおすすめします。- 温度変化が少ない
- 湿気が多くない
- 直射日光が当たらない
- ほこりが多くない
- 床は水平で凹凸がなく強度もある
- 騒音を抑えることができる
- 腐食室の側等ではない
- 近くに電源(コントロールボックス)がある
- 近くに水源がある ※縦型プレス機ではない場合
- プレス機械を操作する者がスライドの方向を見ることができる向きである
- 作業者の位置が、共同して作業を行う者の作業行動を見ることができる場所である
プレス機は衝撃を用いた加工法のため、高周波など複数の音が複雑に絡まりあって騒音に発展することがあります。
一般的な騒音値は、100〜105dB程度です。パチンコ店内で90dB、車のクラクションで100dBと言われているため、相当な音であることがわかります。加えて、一瞬の音ではなく、継続して騒音が続くことになります。
85dBを超える騒音環境では、音源対策や作業者側の対策が必要です。防音カバーなどを用いると、建物全体に工事を施す必要がないため、コストカットができます。
振動による騒音を抑えるために、防振装置の取り付けを検討してみてください。
プレス機を設置する際の注意点①
プレス機は、「労働安全衛生規則」第86条第1項で定められる「機器等」に該当しています。そのため、プレス設備の購入・設置、移設、主要な構造部分を変更する際には、「設置届」を提出することが義務付けられています。工事開始30日前までに届け出てください。
概要を説明する書類も必要ですが、書式の決まりはありません。「労働安全衛生規則」第86条関係 別表第七”の事項を確認し、提出しましょう。
監督署によっては、手続き方法が異なるだけでなく、指定の書式が用意されている場合もあります。必ず、管轄の労働基準監督署に確認してください。
プレス機を設置する際の注意点②
ベルトコンベアを使用し且つ床面からフラットに投入口を設置する場合に、基礎工事が必要です。また、現地での組立の多い据付工事や1件の請負契約金額が500万円以上の場合に、機械の設置工事は建設業法による「機械器具設置工事業」の建設業許可が必要です。
ですが、機械が一体のもので、トラックなどから降ろして設置場所に据え付ける場合には不要です。
プレス機を製造する代表的なメーカー5社
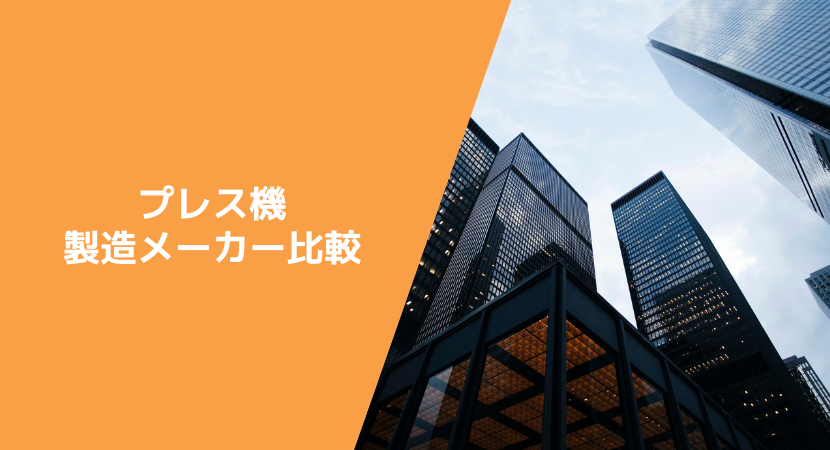
プレス機を製造する主なメーカーには、以下の企業が挙げられます。
- コマツ産機
- 山岡製作所
- アイダエンジニアリング
- アマダ
- タナカカメ