Its appeal lies in its efficiency and superior results compared to manual labor or grinding machinery. However, achieving optimal results hinges on familiarity with both the polishing machine and the specific polishing stones employed.
In this article, we will introduce the types and characteristics of barrel polishing machines. We will also touch up on the influence of processing conditions on quality and the manufacturers that sell them.
目次
Barrel Polishing Machine Features
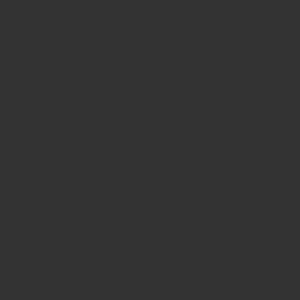
The barrel polishing machine is a solution capable of handling a broad spectrum of polishing tasks. Inside a barrel-like structure, the workpiece, polishing stone, compound, and water are combined and subjected to rotational friction for polishing.
Depending on the combination of polishing stones and polishing aids (compounds), deburring and surface finishing of various workpieces can be done all at once.
The structure of the machine is simple because the entire barrel containing the workpiece and polishing stones is rotated and polished. Polishing can be done without the need for complicated work procedures.
In addition to deburring, radiating, and descaling, one barrel polisher can also perform mirror polishing, which is very time-consuming to do by hand.
Six Types of Barrel Polishing Machines, Advantages and Disadvantages and Installation Locations
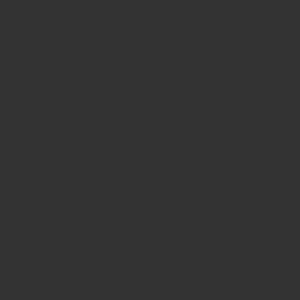
Let us now take a look at the many types of barrel polishing machines.
- Fluid barrel polishing machine
- Rotary barrel polishing machine
- Centrifugal barrel polishing machine
- Vibrating barrel polishing machine
- Heavy pressure barrel polishing machine
- Magnetic barrel polishing machine
Let us now discuss the characteristics, advantages and disadvantages of each polishing machine.
Characteristics of fluidized barrel polishing machine
A fluidized barrel polishing machine uses a rotary disk attached to the bottom of the barrel tank that rotates. The workpiece, polishing stone, and compound flow and rub against each other to polish. Barrel capacity ranges from 10 liters to 300 liters. The polishing power of this system is classified as medium.Barrel polishing machines require a lot of time and effort to sort the workpiece and polishing stone, but each manufacturer has come up with various improvements of their own. These improvements range from types that automate everything from product loading to polishing, discharge, sorting, and even final collection.
This polishing machine is suitable for mass production and making low-cost products because it can significantly shorten the overall processing time.
Advantages of fluidized barrel polishing machine
The fluidized barrel polishing machine offers the capability to polish large quantities of workpieces uniformly and consistently, making it a perfect choice for processing thousands of small parts.Since the barrel tank is not sealed, you can polish the product while checking its finish. It is also effective when you want to improve work efficiency. This type of barrel polishing machine is also extremely quiet compared to regular polishing machines, so you can use it with confidence even in urban areas.
Summary of advantages
- Excellent uniformity
- Facilitates mass production
- Allows simultaneous polishing and finish inspection
- Exceptionally quiet operation
Disadvantages of fluidized barrel polishing machine
The structure and operation are simple, but the direction of rotation of the polishing tank is constant. A major disadvantage here is that it is difficult to adjust the polishing conditions.Summary of disadvantages
- Rotation direction is constant
- Difficult to adjust conditions
Installation points for fluidized barrel polishing machine
In this case, the barrel tank is not sealed. If installed on a slope, there is a risk of workpieces and water splashing out. As such, we recommend install it on the floor of the factory or in a stable and flat place outdoors.Characteristics of rotary barrel polishing machine
A rotary barrel polisher works by rotating a polygonal barrel container and rubbing the polishing stone against the workpiece for polishing. With a polishing power ranging from low to medium, this type of barrel polishing machine is well-suited for medium to light deburring and achieving smooth finishes.Advantages of rotary barrel polishing machine
The rotary barrel polishing machine boasts a simple structure compared to other barrel polishing machines. Combined with its high versatility, it excels in handling a wide range of workpieces, including metal, plastic, ceramics, precious stones, and glass.It also offers a very noticeable cost advantage, being easily installable at a low cost. With minimal maintenance requirements and low ongoing costs, it provides peace of mind regarding expenses post-installation.
Summary of advantages
- Highly versatile
- Suitable for various workpieces
- Low cost
- Easy to maintain
Disadvantages of rotary barrel polishing machine
Among barrel polishing machines, it does not have the strongest polishing power. Extending the polishing time increases the possibility of wear of the polishing stone and deformation of the workpiece. If you are looking for a strong polisher, it is better to choose a different polisher.Summary of disadvantages
- Weak polishing power
- Easy to wear and tear
Rotary barrel polishing machine installation points
Although it is a relatively small polishing machine, it is recommended to install it in a large area. It is best to install it on a stable, flat surface.Features of centrifugal barrel polishing machine
Centrifugal barrel polishing machines are used on many sites. This is a polishing method that uses high pressure and high-speed flow to polish a barrel container by combining rotation and revolution.It has stronger polishing power than rotary or vibrating barrel polishers, and can perform everything from heavy cutting to precision finishing in a short time.
This means that it is suitable for workpieces with high quality requirements.
Advantages of centrifugal barrel polishing machine
Its attractive features include short polishing time and high productivity. Due to its strong abrasive power, it is possible to perform a wide range of polishing tasks, from heavy cutting to precision finishing. Another strength is that it is easy to change the shape and rotation speed of the polishing tank. Polishing conditions can be easily adjusted and can be applied to a variety of workpieces.Summary of advantages
- Reduced polishing time
- High productivity
- High polishing power
- Easy to adjust conditions
Disadvantages of centrifugal barrel polishing machine
Centrifugal barrel polishing machines have a strong abrasive power, so the longer the polishing time is, the more the workpiece and abrasive material will become hot. This makes it unsuitable for workpieces that are sensitive to heat. Additionally, since the barrel capacity is small, it is not suitable for large parts or large quantities of polishing. Maintenance and maintenance costs are higher than other polishing machines due to the complexity of the mechanical structure.Summary of disadvantages
- Easy to get hot
- Unsuitable for polishing large parts or mass production
- High cost
Centrifugal barrel polishing machine installation points
The barrel rotates, so the barrel shaft is more likely to wear out in inclined locations. Please install it on a flat surface. In addition, if the capacity is large, the polishing machine itself will also be large, so a corresponding amount of space will be required.Features of vibrating barrel polishing machine
A vibrating barrel polishing machine is a method of polishing by applying three-dimensional vibration to a barrel tank. It is used for polishing metal, plastic, ceramic, and glass products, and is suitable for deburring and smoothing small to large parts.Advantages of vibrating barrel polishing machine
The polishing power is medium, but the motor vibration can be adjusted, so polishing conditions can be easily changed. Depending on the conditions, it is resistant to scratches and dents and can be used on a variety of workpieces. Furthermore, since the heat it generates is minimal, it can be used for workpieces that are sensitive to heat.The high workability is also noteworthy. The unsealed barrel bath allows you to check the finish of the workpiece during polishing.
Summary of advantages
- Easy to change conditions
- Can be used for various types of work
- Depending on conditions, scratches and dents are less likely to occur
- Generates very little heat
- You can polish while checking the finish
Disadvantages of vibrating barrel polishing machine
Processing time tends to be longer due to the process being performed using fine vibrations. Also, compared to other polishing machines, the shape of the barrel tank is special, and there are restrictions on the type and size of polishing stones. It is easy to operate and easy to automate, but the polishing machine is expensive.Summary of disadvantages
- Processing tends to take a long time
- Limited to type and size of polishing stone
- High cost
Installation points for vibrating barrel polishing machine
Vibrating barrel polishing machines come in a variety of sizes, but the larger ones require a larger space. Some models do not have a sealed barrel, so they require installation on a flat surface.Features of heavy pressure barrel polishing machine
A heavy-pressure barrel polishing machine is a polishing machine that applies pressure to a barrel tank and rotates it to polish the workpiece at high speed. It has high polishing power even at low speeds, and has the feature of significantly shortening processing time.Advantages of heavy pressure barrel polishing machine
High pressure increases the contact area between the polishing stone and the workpiece. Polishing time can sometimes be cut in half compared to a regular rotary barrel polisher due to the enhanced polishing effect. It also ensures uniform wear of the polishing stone and improves the accuracy of the surface finish of the workpiece.Summary of advantages
- High polishing effectiveness
- Potential time savings
- Precision surface finishing of workpieces
Disadvantages of heavy pressure barrel polishing machine
The structure of heavy pressure barrel polishing machines is noticeably more intricate when compared to standard rotary barrel polishing machines. This complexity extends to requiring ancillary equipment such as heavy pressure and hydraulic systems, contributing to a potentially high initial investment. Moreover, there is also a very high pressure exerted on the barrel tank during its operation. This restricts the possibility of size expansion, rendering it unsuitable for accommodating large workpieces.Summary of disadvantages
- High cost
- Not suitable for large workpieces
For optimal installation of a heavy pressure barrel polishing machine, it is imperative to ensure that multiple barrels are placed on a flat surface to prevent shaft galling. Additionally, sufficient separate space is necessary to accommodate the installation of additional equipment.
Features of magnetic barrel polishing machine
The magnet rotates with the rotary disk, and the magnetic abrasive grains inside the container move violently and polish. In addition to rotational motion, the abrasive grains move in a complex manner using magnetic force, so even complex workpieces can be polished uniformly. It is often used for deburring metal parts and adding shine.Advantages of porcelain barrel polishing machine
Polishing of abrasive grains using magnetic force is combined with normal polishing techniques. The advantage is that even complex workpieces can be polished easily. Deburring, polishing, and cleaning can be done quickly and efficiently. This polishing machine is popular in many industries because of its convenience.Summary of advantages
- Excellent polishing properties
- Highly convenient
Disadvantages of porcelain barrel polishing machine
It is not suitable for large-scale polishing due to its weak polishing power. It is only used for deburring and pretreatment before plating that does not cause shape changes.Installation Points for Porcelain Barrel Polishing Machine
Porcelain barrel polishing machines are available in various sizes, with most being relatively compact, making them convenient for storage. However, as with any polisher, it is important to set it up on a flat surface for optimal operation.Four comparison criteria | How to choose a barrel polishing machine
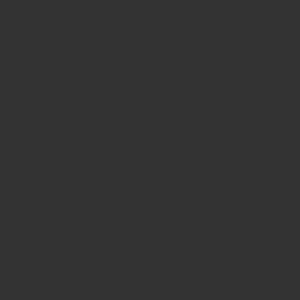
The simple processing method tends to be the province of craftsmen. Processing conditions of machines vary widely, so we will touch on the points you should check when selecting a polishing machine.
- Rotation speed
- Barrel capacity
- Processing time
- Concentration of polishing media
Rotation speed
The centrifugal force and frictional force applied to the workpiece and polishing stone will change. It directly affects the polishing conditions. If the rotation speed is high, the polishing power will increase, but the workpiece will become hot. Look for a polishing machine that allows you to choose the rotation speed that suits the workpiece.Barrel capacity
Barrel capacity affects the amount of work that can be processed at once and is directly linked to production capacity. However, if the size is too large, the polishing time will be longer, so it is necessary to choose the optimal capacity depending on the purpose.Processing time
If productivity is important, shorter machining times are better. Media consumption is also reduced, and total costs can be reduced. Short polishing time affects burrs, scratches, and surface gloss, so it is important to select a polishing machine that can meet quality standards.Concentration of polishing media
The concentration of the medium is also important for polishing. It affects the frictional force and fluidity of the workpiece and abrasive material, and is directly linked to the overall quality. Please choose the medium that suits your work. The selling manufacturer also has the know-how, so if you have any concerns, it’s a good idea to ask them directly.Four recommended manufacturers of barrel polishing machines
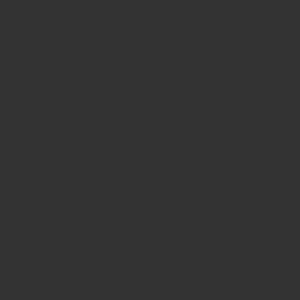
Barrel polishing machines may be a niche market, but there are manufacturers with a proven track record. Here we will introduce some of the major manufacturers in Japan.
Tipton | Imahashi Manufacturing | Snail | Shinto Kogyo | |
---|---|---|---|---|
Fluid barrel polishing machine | – | – | ✔ | ✔ |
Rotary barrel polishing machine | ✔ | ✔ | – | ✔ |
Centrifugal barrel polishing machine | ✔ | – | ✔ | ✔ |
Vibrating barrel polishing machine | ✔ | ✔ | ✔ | ✔ |
Heavy pressure barrel polishing machine | ✔ | – | – | – |
Magnetic barrel polishing machine | ✔ | ✔ | – | – |
Contact JET Global
Tipton Co., Ltd.
“Tipton” is the largest manufacturer of barrel polishing machines with a 65% market share. They have a full lineup of barrel polishing machines and over 80 years of experience and know-how. In addition to polishing machines, they have a lineup of approximately 1,500 types of polishing stones and approximately 500 types of compounds. They do business not only domestically but also overseas.Imahashi Manufacturing Co., Ltd.
Imahashi Seisakusho is a manufacturer of jewelry processing machines and high-precision processing machines for brittle materials. They are developing polishing machines by applying the technology developed in jewelry processing. They have a rich lineup of cylindrical electromagnetic barrel polishers that use electromagnetic force.Tanishi Co., Ltd.
Tanishi has been in business for over 30 years and sells equipment and consumables related to surface treatments such as shaving, polishing, and forging.Shinto Kogyo Co., Ltd.
Shinto Kogyo has accumulated know-how in various fields such as surface treatment business, casting business, and environmental business. Companies with multi-disciplinary experience are more likely think of ideas that cross over different fields.Their barrel polishing machine lineup also has a wide range of features.
Their barrel polishing machines can easily polish by simply putting work, media, compound, and water into the barrel tank and operating it. They are responsible for the final process of many parts in the automobile, aviation, medical, food, and other fields.
In the past, usage of these machines required knowledgeable craftsmen, but as the technology of polishing machine manufacturers improves, more and more models are becoming available that are easy for anyone to use.
Purchasing your own barrel polishing machine
Is the company really suitable for your business? Are you choosing the right model? Please feel free to contact us if you have any concerns.We will consider the differences between each product and company and suggest the company that best suits your business and its unique needs.
Contact JET Global