Not all laser welding machines are created equal. They vary in specs, prices, and what they’re best for. Choosing the wrong one could end up costing you a lot and might even be risky.
In this article, we’ll break down the basics of laser welding machines, talk about the different types and what makes each one unique, explore where they’re used, weigh up their pros and cons, and give you some pointers on picking the right one, including a detailed manufacturer comparison.
By the end of this article, you’ll have a good grasp of the key selection criteria for choosing a laser welding machine. We have put together a list of recommended companies that manufacture laser welding machines. If any of them catch your eye, don’t hesitate to reach out to us!
目次
What is a laser welder? Five Types of Laser Welders
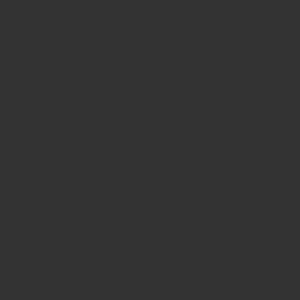
A laser welder is a welding machine that uses a focused beam of high energy light to fuse materials together. It works by shining a focused beam of laser light onto the surfaces of the materials to be welded, forcing them to melt and fuse together at the point of contact. Laser welders are quite well-known for their precision, speed, and versatility, making them ideal for a wide range of applications across industries. They are widely employed in manufacturing processes for metals, polymers, and other materials that demand high-quality and precise welding.
Let’s break down the basic operational structure:
Operation structure of laser welding machine
- A laser oscillator emits laser light, acting as the machine’s energy source
- This laser light travels along an optical path
- A focusing unit, like a focusing lens, concentrates the laser light into a spot system
- The focused laser light is then directed onto the material placed on the workbench
The above is the basic process. In addition, a process may be added to blow out shielding gas to prevent oxidation and nitridation of the welded area.
5 unique laser types
The most important point in the above structure is the type of laser light. Laser welding machines can be roughly divided into the following five types.- CO2 Laser
- YAG Laser
- Fiber Laser
- Disc Laser
- Semiconductor Laser
Let’s break this down and explain the 5 different types of lasers.
(Reference 1: Welding revolution “laser welding”)
(Reference 2: MONO Juku “What is laser welding? Easy-to-understand explanation of principles, types, etc.” )
CO2 (Carbon Dioxide) Laser
The CO2 laser stands out as a prominent example of gas laser welding. Its defining characteristic lies in utilizing carbon dioxide as a medium to amplify light. In particular, it is possible to perform uniform and high-strength welding when welding materials with a thickness of 10 mm or more or over large areas of several tens of square centimeters or more. It is also possible to weld resin, etc., so it is used in a wide range of fields.Another feature is that capable of stable continuous operation for long periods of time, allowing continuous work to be carried out on large-scale production lines. CO2 lasers are mainly used in the automotive industry but also play a pivotal role in advancing manufacturing processes.
YAG Laser
The YAG laser is a great example of solid-state laser welding technology. It uses a crystal with a garnet structure as its medium. Due to its characteristics as a pulsed laser, it repeats blinking at small time intervals. Because the wavelength is shorter than that of CO2 laser, energy absorption rate by metal is high and welding is easy.In addition, it has excellent coherency and laser spreading performance, and is easy to use as it has excellent laser light collection and diffusion. These qualities make them well-suited for welding precision components and delicate tasks.. YAG lasers are mainly used in medical device manufacturing.
Fiber Laser
A fiber laser is a type of solid-state laser that uses an optical fiber as its medium. Its remarkable efficiency comes from confining light within a slender fiber and then amplifying it, enabling exceptionally clean welding.With a short wavelength and the capability to narrow down the spot, fiber lasers boast high energy density, facilitating deep penetration into highly reflective materials like aluminum and copper. It is also used for welding dissimilar metals together.
Another attractive feature is the ease of automation, such as non-contact, high-speed welding and the ability to automatically set the beam focus. In addition, there tends to be a wide range of products, including handy (hand) torch types and types with cutting, burn removal, and cleaner functions. Fiber lasers are widely used in general industrial products.
Disc Laser
A disk laser is a type of solid-state laser. A crystal doped with rare earth elements such as ytterbium is used as the medium.These lasers are designed with the aim of overcoming a common issue found in solid-state lasers: a decline in welding accuracy. Traditional solid-state lasers encounter a challenge where heat generated during operation causes uneven temperature distribution in the laser crystal, leading to a thermal lens effect. This effect occurs because the crystal’s refractive index behaves akin to that of a lens, resulting in reduced laser focusing power.
Disk lasers solve this problem by making the laser crystal into a thin disk shape and attaching a heat sink to the back, resulting in higher welding accuracy than previous solid-state lasers. Disk lasers are commonly used in the aerospace industry.
Semiconductor Laser
A semiconductor laser is a type of solid-state laser. Mainly semiconductor materials are used as the medium. It’s also known by other terms such as diode laser or laser diode.What sets semiconductor lasers apart is their unique heat source: the laser light generated when an electric current passes through the semiconductor. Since it does not use a lamp as the excitation (supply) source, it can be used even in limited spaces.
It is also suitable for very detailed welding work. Semiconductor lasers are commonly used in electronics manufacturing.
So far, we’ve covered the principles and characteristics of various laser welding machines. In this next section, we will look into the industries and specific applications where these machines find use. Since each industry has different applications, we hope you will keep reading to understand the applications.
Industry Applications for Laser Welding Machines
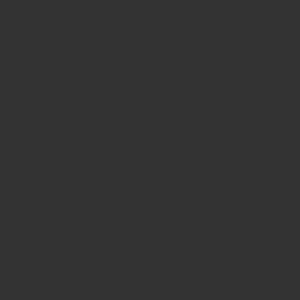
In the previous section, we looked into the workings of laser welding machines and the unique traits of each type of laser. Now, let us take a look at the diverse industries where laser welding machines find their applications, along with examples of how they’re used. Fields and industries where laser welding machines find regular use include:
(Reference: NISHIHARA “What is laser welding”)
Let us now break down each industry and see how these lasers are used in these fields.
Automotive Industry
In the automotive industry, laser welding machines are used for body spot welding and seam welding.Specifically, it is often used in the following assembly processes.
- Welding of vehicle frame and chassis (skeleton)
- Assembling the door panel and bonnet
- Precision welding of thin metal parts
- Manufacture of vehicle exhaust systems (systems related to exhaust gas)
- Assembling battery packs (ex. electric vehicles, etc.)
- Welding of lightweight materials (ex. aluminum alloy, etc.)
- Welding of composite materials (ex. fiber reinforced plastics, etc.)
- Welding of small electronic parts such as airbag sensors
The main reason why laser welding machines are used in manufacturing processes in the automotive industry is because Car assembly welding sometimes requires precision work. Laser welding machines are capable of extremely fast and precise welding, and are compatible with automation, contributing to efficiency and quality improvement in automobile manufacturing.
Electronic Component Manufacturing Industry
In the electronic component manufacturing industry, laser welding machines are used for spot welding of fine wires and pins.In particular, it is often used in the following manufacturing processes.
- Welding minute parts on the board
- Bonding of electronic chip and substrate
- Assembling sensor parts
- Precision connector manufacturing
- Assembling the battery pack
- Welding small parts inside smartphones
- Assembling the camera module
- Welding of small electronic components for medical equipment
Electronic component manufacturing requires precision processing. Laser welding machines can meet these demands. It is also possible to handle different materials and minimize heat damage to parts. These characteristics of laser welding machines contribute to consistent quality maintenance of electronic components.
Aerospace Industry
In the aerospace industry, laser welders are used to manufacture parts that require high strength to withstand safety standards.It may be used in the following manufacturing processes:
- Assembling structural parts such as aircraft frames
- Manufacture of turbine blades
- Precision welding of lightweight alloy materials
- Assembling engine components
- Welding of high strength aluminum alloy
- Manufacture of aerodynamic components
- Assembling small satellite parts
- Welding of electronic systems inside aircraft
Parts and products needed in the aerospace industry require durable quality and light weight. Laser welding machines are capable of high-strength welding and can handle a wide variety of materials, making them more efficient and lightweight. You can also do a combination.
Medical Device Manufacturer
Medical device manufacturers use laser welding machines to assemble and repair precision medical equipment.For example, it is often used in the following manufacturing processes and also finds use in reparing different electrical components.
- Precision assembly of surgical instruments
- Production and repair of implants (teeth and bones)
- Assembling small parts for medical electronics
- Manufacturing and repair of probes and sensors
- Advanced medical device housing manufacturing
- Joining metal parts of medical devices
When manufacturing medical devices, extremely high safety and quality standards must be met, and one manufacturing tool that can meet these standards is a laser welder.
Machine Manufacturer
Laser welding machines are also widely used in the manufacture of mechanical products other than the automobiles and medical devices mentioned above. Machine manufacturers use laser welding machines to assemble precision machine parts.For example, it is often used in the following situations:
- Assembling large structures
- Manufacture of metal parts that require high-precision welding
- Welding parts with complex shapes
- Use of lightweight and durable materials
- Use for seamless joining of metal parts
- High quality surface treatment
- Use in automated production lines
It is commonly used in the automotive and medical device industries, but it can also be used for assembly of large structures and work that requires high-quality surface treatment. >It is characterized by being often used.
Jewelry Maker
Jewelry manufacturers use laser welders to join and repair delicate metal parts.- Assembling delicate jewelry
- Precise joining of different metals
- Jewelry Restoration and Repair
- Jewelry installation
- Size adjustment (ring size, etc.)
- Custom design production
Laser welding machines are widely used by jewelry manufacturers because they require delicate and precise welding capabilities. The jewelry making process involves assembling small parts and attempting to realize complex designs.
Another reason for its use is that the range of thermal effects is small, so there is less risk of damaging expensive materials such as gold and platinum. Laser welding machines can perform welding at a level that satisfies the above conditions, so they are used in a wide range of applications in the jewelry industry.
Up to this point, we have introduced the industries in which laser welding machines are used and examples of their applications. In our next section, we will explain the advantages and disadvantages of using a laser welder.
Advantages and Disadvantages of Laser Welding Machines
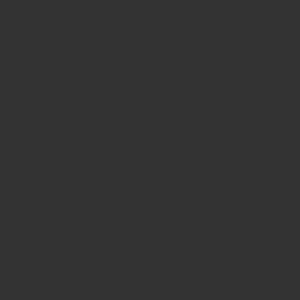
Now that we have gone over the industry applications, let us now take a closer look at the advantages and disadvantages of using laser welding machines.
(Reference: Weltecsha “Principles, usage examples, advantages, disadvantages, and tips of precision welding by laser”)
Advantages
There are three main advantages of laser welding machines:- High precision (spot welding, etc.) and high quality
- Welding speed leads to cost and time reduction
- Can process various materials
High precision (spot welding, etc.) and high quality
Laser welding machines enable extremely precise and high quality welding through precise beam control. This is especially important when joining small parts or complex geometries to ensure uniformity and strength of the weld.Maintaining strength while minimizing the visibility of welds enhances the overall quality of the product. This advantage holds significant importance in industries like electronic component manufacturing and medical device production, where both precision and aesthetic quality are paramount.
Welding speed leads to cost and time reduction
Laser welders operate at high speeds, significantly increasing production efficiency compared to traditional welding methods. This contributes to cost and time savings in manufacturing industries where high volume production is required.Although the market is changing rapidly these days, laser welding technology proves invaluable in industries such as automobile manufacturing and electronic component production, enabling swift responses to dynamic demands and market shifts.
Can process various materials
Laser welding machines can handle a wide variety of materials, allowing to weld various types of materials such as metals, plastics, and synthetic materials with one device. This increases flexibility in product design and allows for different material combinations.This advantage is especially sought after in the aerospace industry, where composite materials are heavily used.
Disadvantages
Identifying the disadvantages of laser welding machines is crucial, particularly when considering their adoption. In addition to the following three points, it’s essential to anticipate and address any potential concerns that may arise during the implementation of the system within your company.- High capital investment and running costs (gas, electricity, etc.)
- Technical expertise required
- Unavailable depending on board thickness
High capital investment and running costs (gas, electricity, etc.)
Laser welding machines use advanced technology such as expensive laser oscillators and precise control systems, so purchase costs are considerably higher than regular welding machines. Additionally, running costs such as electricity bills are incurred periodicallyThere are some products that can keep running costs low, such as handheld torch-type fiber laser welding machines, but if we include investment in environmental equipment, including safety, the overall initial cost tends to be high.
For small businesses or businesses that are installing a laser welding machine for the first time, be aware that the initial cost can be a big burden.
Technical expertise required
Handheld laser welding machines are often designed to be easy to use even for beginners, but in general, the operation and maintenance of laser welding machines requires specialized technical knowledge.To use laser welding machines properly, operators require specialized skills, such as specialized training and experience. Please keep in mind that this will entail the use of more resources as you will be required to secure appropriate human resources and provide continuous training to operators.
Unavailable depending on board thickness
Laser welders are optimized for a specific thickness of material and may not be suitable for very thin or, conversely, very thick materials. Therefore, if you need to weld materials of different thickness, you may also need to consider additional equipment or different welding methods.In particular, if you are in the manufacturing industry that handles a variety of products or products that must handle a variety of materials, be careful about how much the single laser welding machine you are considering can handle. is required.
So far, we have listed and explained three advantages and disadvantages of using a laser welder.
In the next chapter, we will explain six points to consider when choosing a laser welding machine.
What type of laser should I choose?
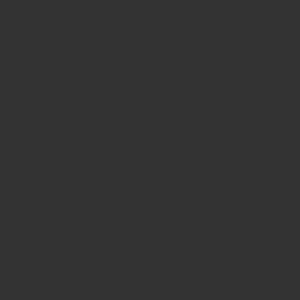
In this section, we will take some time to explain the best way to choose a laser welding machine from six key perspectives, depending on the type of laser. Please refer to the following items after understanding the applications required by your company and the materials used.
Commonly used industries and materials
With numerous types of materials available, it’s crucial to consider your industry and the materials your company deals with when selecting a laser welder. Before making a decision, consider the laser welding machine’s ability to accurately and precisely handle a wide range of materials.Let us now take a look at a list of suitable materials for different types of laser welding machines, along with the industries where they are commonly used:
Suitable Materials | Industry | |
---|---|---|
CO2 Laser | Nonferrous metals (aluminum, copper), steel, stainless steel | Automotive industry, aerospace industry, Heavy industry |
YAG Laser | Iron, stainless steel, titanium, alloy | Medical equipment manufacturing, electronic equipment manufacturing, Precision engineering |
Fiber Laser | Almost all metals (steel, stainless steel, aluminum, titanium, copper, etc.) |
Automotive industry, electronic equipment manufacturing, General industry |
Disc Laser | Stainless steel, steel, titanium, non-ferrous metals | Aerospace industry, automotive industry, Medical device manufacturing |
Semiconductor Laser | Light metals, thin sheet metals, plastics | Electronic equipment manufacturing, small parts manufacturing, Medical equipment manufacturing |
When considering the selection of a laser welding machine, it’s essential to focus on the breadth of materials that can be effectively welded. Let’s take a look
Fiber Lasers
- Pros: Fiber lasers offer versatility and can weld a relatively wide range of materials, including various metals such as copper, brass, and gold. However, they may not be suitable for plastics
- Cons: Not suitable for welding plastics
Semiconductor Lasers
- Pros: Semiconductor lasers are suitable for welding plastics, making them versatile for certain applications. They can effectively join materials like polymers
- Cons: Not ideal for thick materials such as steel, as they may lack the power required for deep penetration welding
Characteristics and Suitable Welding Applications
Depending on the welding method employed, the surface may show signs of burning. When selecting a laser welding machine, understanding your company’s performance needs is paramount. If you take time to properly examine the functional characteristics of the laser type to ensure it delivers the desired results, you will have made a good investment.Additionally, the functionality and quality of welding vary depending on the type of laser that is being used. Let us go over some of these characteristics by type.
Functional features | Appropriate use | |
---|---|---|
CO2 laser |
High energy efficiency deep penetration power |
Suitable for welding thick materials Enables uniform welding in large area welding work |
YAG laser |
Compatible with various metals Good at fine welding |
High precision and fine welding Suitable for small parts and precision equipment |
Fiber laser |
Excellent beam quality high energy density |
Beautiful and precise welding possible Suitable for thin to medium-thick plates |
Disc laser |
High beam quality and power Precise and deep penetration power |
High quality and uniform welding possible Suitable for metal processing |
Semiconductor laser |
Relatively low output Capable of welding small, lightweight parts |
Suitable for fine parts and thin materials High precision, welding with not too deep penetration possible |
The functionality of each type of laser and the resulting welding quality are closely related. For example, CO2 lasers have deep penetrating power, making it easy to weld thick materials.
Price and Cost
It is important to first organize the purpose of use in your company and calculate and understand the installation and operation costs. Then, based on your budget, find a laser welding machine that suits your purpose and keeps costs as low as possible.By understanding the overall price, you can plan for long-term operations. First of all, the price range of a single laser welding machine can be divided into the following three points of view.
Price range of laser welding machine
Low price range: Suitable for small-scale work and simple welding. For example, laser welding machines used in small workshops and jewelry repairs fall into this price range. Prices range from approximately 1,300 USD to 14,000 USD.Medium price range: Highly versatile and suitable for small-scale manufacturing. For example, this includes medium-sized parts manufacturing and repair operations. The price ranges from approximately 14,000 USD to 140,000 USD.
High price range: For large-scale manufacturing industries with high precision and mass production capacity. Suitable for the automotive and aerospace industries. The price ranges from about 140,000 USD to 650,000 USD
In addition to the unit price of the laser welding machine, there are also costs associated with it. There are three main points where costs occur:
- Introduction cost (initial cost including unit price)
- Operating costs (power consumption and maintenance)
- Training cost (operator training/education)
Below are the installation costs and operating costs for each type of laser.
Introduction cost | Operating costs | |
---|---|---|
CO2 Laser | Initial capital investment is high | Maintenance costs (gas replenishment, replacement, optical system adjustment) are required. |
YAG Laser | Initial capital investment is moderate |
The lifespan of the light source is short and replacement costs are incurred Maintenance of expensive optical system is required |
Fiber Laser | There are some cheap ones, but the initial capital investment tends to be high. | Lower maintenance costs in the long run |
Disc laser | Initial investment amount is high | Long-term operating costs are low due to high efficiency |
Semiconductor laser | Initial investment is relatively low | Costs incurred when repairing or replacing precision parts |
Ease of use and maintenance
When picking a laser welding machine, it is important to make a choice keeping in mind the ease of access and ability to maintain and handle the equipment at your factory or location. Let us take a look at a few prospective options.Ease of use | Maintenance | |
---|---|---|
CO2 Laser |
Complex compared to others It may be necessary to adjust the optical system |
Cleaning and adjusting optical components Regular laser gas replacement |
YAG Laser |
Simple compared to others Requires precise setup |
Regular replacement of lamps Particular attention should be paid to the lamp life. |
Fiber laser |
Relatively easy and intuitive operation Easy automation and integration |
Almost maintenance free Regular inspection of fiber cables and lenses |
Disc Laser |
Requires more advanced operation than others High stability once set up |
Regular cleaning and adjustment of optical components Overall maintenance is relatively easy |
Semiconductor Laser |
Often small and easy to operate Handheld type also available |
Low Maintenance Parts may need to be checked or replaced |
It is important to ensure optimal utilization and performance assessment of your existing laser welding machine. Evaluate its operational status, including usage patterns and any encountered issues and make note of these patterns.
It is also advisable to properly assess the proficiency of your staff and the company’s expertise in handling laser welding machines as this is crucial for safety.
Production Efficiency
Production efficiency also varies depending on the type of laser. Choose a welding machine that will give you the maximum efficiency you are looking for, while considering whether it will integrate well with your existing systems.It must also be noted that efficiency is affected by the application (operation panel), materials to be welded, and complexity of the welding process, which differ for each product. Let’s take a look at some of the factors that should be considered in this case.
- Is the laser type appropriate for the plate thickness?
- Can it be easily integrated into your production line?
- Is it an appropriate level of efficiency (does it compromise safety)?
Refer to our handy table below showcasing the advantages and disadvantages in terms of production efficiency.
Advantages in production efficiency | Disadvantages in production efficiency | |
---|---|---|
CO2 Laser |
Suitable for mass production Suitable for non-ferrous metals (aluminum, copper), steel, stainless steel, etc. |
As large equipment is required, it takes time to install and set up. |
YAG Laser |
Good efficiency for small-scale products Suitable for iron, stainless steel, titanium, alloys, etc. |
Maintenance such as lamp replacement takes time. |
Fiber Laser |
Suitable for mass production as rapid welding is possible Compatible with almost all metals (steel, stainless steel, aluminum, titanium, copper, etc.) |
May not be suitable for thick materials |
Disc Laser |
Suitable for complex welding operations, Efficient once in operation Suitable for stainless steel, steel, titanium, non-ferrous metals, etc. |
Setup requires specialized knowledge |
Semiconductor Laser |
High efficiency for small-scale products Suitable for light metals, sheet metals, plastics, etc. |
Not very suitable for mass production |
While larger laser welding machines are better suited for mass production, their setup requires more specialized knowledge.
Additionally, when introducing a new welding machine into an existing equipment environment, it’s crucial to consider its compatibility with the current setup.
Safety Measures
The risks and required safety measures vary depending on the type of laser. When choosing a laser welding machine, you should consider its compatibility with your company’s safety protocols and its manageability.All laser welding machines share the requirement for operators to undergo comprehensive safety training and adhere to safety protocols. Regular maintenance is also essential.
Danger | Necessary safety measures | |
---|---|---|
CO2 Laser |
Emit visible light Handles high power |
Appropriate safety glasses are required to prevent light from shining into your eyes Appropriate shielding or shielding is required considering the impact on the surrounding area |
YAG Laser |
Eye Risk There is a risk of high temperatures |
Appropriate safety glasses are required When using it, it is important to manage the safety of the surrounding area. |
Fiber laser |
Strong beam strength Care must be taken when handling fiber cables |
Strict protective measures are required to avoid direct beam exposure |
Disc laser |
Using high power laser Risk of beam leakage and reflections |
Appropriate protective measures and operator training required It is necessary to ensure a safe operating environment and shielding that takes into account the impact on the surrounding area. |
Semiconductor laser |
Although many have low output, Direct beam exposure is not good for the eyes. |
Safety glasses must be worn |
Since the welding method uses laser light, safety glasses, a welding surface, and a welding helmet are required. The range that requires safety management may vary depending on the size of the welding machine.
If you choose a method that only considers the installation cost, you should be careful because in the worst case scenario, it may lead to irreversible problems such as injury to staff.
Up to this point, we have explained the main points to consider when choosing a laser welding machine. In the next chapter, we will introduce a list of manufacturers that manufacture laser welding machines.
Laser Welding Manufacturer Comparison
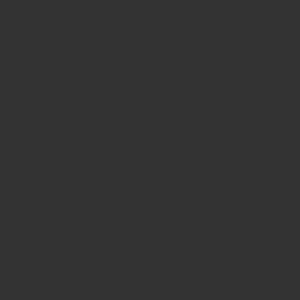
In the last section, we discussed six important factors to consider when choosing a laser welding machine. Now that we have reviewed most of the essential information behind the workings of laser welding machines, we can now attempt to find a company that offers the perfect laser welding machine for your needs.
Here, we’ll introduce some top manufacturers of laser welding machines. If any of them catch your eye, feel free to reach out to us!
CO2 Laser | YAG Laser | Fiber Laser | Disc Laser | Semiconductor Laser | |
---|---|---|---|---|---|
Kokyo | ‐ | ‐ | ✓ | ‐ | ‐ |
Aim | – | – | ✓ | ‐ | – |
Techno Coat | – | ✓ | – | – | ‐ |
Amada Weld Tech | ‐ | ✓ | ✓ | ‐ | – |
Daihen | ‐ | – | ✓ | ‐ | – |
TRUMPF | ✓ | ‐ | ✓ | ✓ | ‐ |
Laser Line | – | ‐ | ‐ | ‐ | ✓ |
Contact JET Global
Kokyo
Founded in 2009, Kokyo is a company specializing in the development and sales of products that utilize laser technology. They also handle precision processing and measuring equipment. Kokyo handles lightweight type handheld laser welding machines and conventional type hand torch laser welding machines. Both machines are fiber laser welding machines.Kokyo provides rental and subscription services starting at a fixed monthly fee of 1,300 USD, making it convenient in terms of cost. Additionally, you have the option to rent on a daily basis.
If you are thinking about installing a fiber laser welding machine but concerned about the expenses, we suggest giving Kokyo’s rental/subscription service a try first.
AIM
Founded in 1962, Aim is a company that engages in sheet metal processing, metal processing, and fiber laser welding machine development, sales, and leasing businesses. They handle hand torch type fiber laser welding machines. The torch is equipped with a galvano scanner that allows you to change the beam shape and irradiation range.Moreover, at Aim, you have the opportunity to try out the actual machine firsthand, enabling you to thoroughly examine it before making a decision to introduce it. We highly recommend this option for anyone interested in exploring the possibility of introducing a fiber laser welding machine through a demonstration.
Techno Coat
Founded in 1990, Techno Coat is a company that sells, manufactures, and undertakes contract construction of coating equipment for preventive maintenance of machine parts, molds, etc., and overlay equipment for repair. Laser welding machines handle fiber lasers and YAG lasers.In particular, YAG laser welding machines are used for overlaying and welding to dental laboratories and medical equipment. It is also used for welding mechanical parts and precision parts, and for repairing molds, etc. If you are looking for precise welding of mechanical parts, precision parts, etc., we recommend checking out Technocoat’s YAG laser welding machine.
Amada Weld Tech
Founded in 1972, Amada Weld Tech is a company that operates precision welding and processing businesses under the Amada Group. We are unique in that we have both resistance welding technology and laser welding/processing technology. We handle YAG laser welding machines and fiber laser welding machines.YAG laser welding machines come in two types: the standard version and the YAG SHG variant. The latter can weld copper and gold, which is challenging with YAG fundamental waves. If you are in the market for a YAG laser welding machine capable of handling a diverse range of materials, it might be worthwhile to consider this option.
Daihen
Founded in 1919, Daihen is known for its welding machine business and the development of industrial robots. It is attracting attention for its innovative factory automation products such as contactless power supply systems and AI transfer robots.Daihen offers laser welding machines featuring multi-fiber lasers and equipped with laser-arc hybrid torches. These machines excel in joining materials such as steel and aluminum, providing high strength. They are highly recommended for those interested in melding dissimilar types of metal.
TRUMPF
Founded in 1932, TRUMPF it is a multinational company headquartered in Germany. They primarily operate in the fields of industrial machinery and laser technology and are known for manufacturing high quality metal processing machines, punching machines, laser cutting machines, bending machines, etc.TRUMPF offers CO2 laser and disk laser welding machines. These days, there are fewer and fewer places that sell CO2 laser welding machines, so this is a manufacturer you should check out when considering a CO2 laser welding machine.
Laser Line
Founded in 1997, Laser Line develops and manufactures internationally leading industrial high-power semiconductor lasers.When Laserline was founded, many believed that using semiconductor laser equipment as a light source for laser material processing was impossible. However, the founders, Dr. Christoph Ullmann and engineer Volker Krause, were pioneers in semiconductor lasers from the very beginning.
If you’re considering investing in a semiconductor laser welding machine, Laserline is a manufacturer you definitely don’t want to overlook.
Looking to invest in your own Laser Welding Machine? Reach out to us!
Are you wondering which company would be best suited for your own unqiue needs? Are you choosing the right model? Please feel free to contact us if you have any concerns.We will consult on each product and company with you and suggest the machine that best suits your purpose.
Contact JET Global