It is important to remember when using this advanced sensor, that choosing the wrong LiDAR sensor carries the risk of going over budget, delaying development, or even differences in the functionality of the final product.
So, in order to avoid such risks, it is important to understand the basic knowledge of LiDAR sensors and how to select them.
In today’s article, we will explain in detail LiDAR sensors, their mechanisms, its various types, how to choose one, as well as looking over some major manufacturers for this technology.
目次
What is a LiDAR sensor?
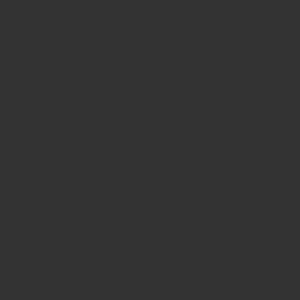
LiDAR sensor is an abbreviation for “Light Detection and Ranging”.
Lidar is technology that uses light to measure the distance and shape of objects and the environment. By irradiating an object with laser light and measuring the time for the reflected light to return and measuring the frequency of the light, the distance to the object can be calculated with a distance measurement accuracy of a few millimeters to a few centimeters. By repeating this operation at high speed, detailed 3D maps of objects and environments can be constructed.
What are the features of LiDAR?
LiDAR has many capabilities that normal sensors do not. These features can range from excellent 3D mapping technology to being able to perform in locations usually inaccessible by other forms of technology.Key LiDAR features include:
- Delivering detailed 3D models with a remarkable accuracy of around 10 mm
- Resilience to day/night variations and weather changes
- Reliable measurements over substantial distances, spanning hundreds of meters
Additionally, while regular cameras only provide 2D information about the color and shape of objects, LiDAR can measure the depth of objects
Ultrasonic sensors and radar also provide distance information, but cannot provide high-resolution 3D mapping like LiDAR.
For this reason, LiDAR has become indispensable in situations where highly accurate 3D data is required, such as in self-driving cars and topographic surveying.
What are the types of LiDAR sensors and how do they work?
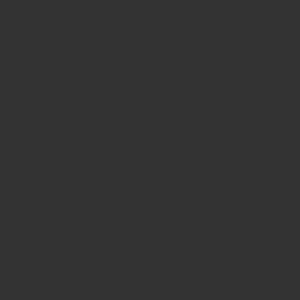
Due to its ability to acquire highly accurate 3D data, LiDAR sensors are being used in a variety of industries and research
In particular, as autonomous driving technology evolves, the importance of LiDAR sensors is increasing day by day
LiDAR sensors can be broadly divided into the following two types.
Solid State Scanning
Solid-state scanning is a type of LiDAR sensor that has a static structure with no moving partsThis type of LiDAR is highly durable and reliable, and exhibits stable performance even over long periods of use and in harsh environments.
There are several types of solid state Lidar, but here we will introduce the two main types
- Optical Phase Solid State Lidar: Leveraging electronic control for enhanced durability
- MEMS-based Solid State Lidar: Utilizing microfabrication technology for rapid laser direction changes
Optical Phase Solid State Lidar
Optical phase solid-state LiDAR is a LiDAR system that measures distance based on changes in the phase of laser light.The most important feature is that it does not use any moving parts and is highly durable as it electronically controls the direction of laser radiation and the light receiving section.
The features of the Optical Phase Solid State LiDAR are as follows :
- High durability and low risk of failure
- Long lifespan of 10 to 20 years and robust
- Fast scanning and responsiveness
- High measurement accuracy of several millimeters – tens of micrometers
- Can accurately detect objects hundreds of meters away
- Compact and easy to integrate due to its small size
On the other hand, system design for optical phase solid-state LiDAR is complex and may require advanced technology.It may also be more expensive for some applications compared to other LiDAR technologies.
Possible changes in performance under extreme environmental conditions should also be considered.
Let’s take a look at some application examples of this technology:
- Immediate detection of road obstacles and other vehicles during vehicle driving assistance and autonomous driving
- Drone navigation and collision avoidance
- Environmental 3D mapping of factories and warehouses, precision manipulation of robot arms, object detection and identification
- Overall, optical phase type solid-state LiDAR is expected to be used in a wide variety of applications due to these useful features, and further developments are expected as technology evolves in the future
MEMS-based Solid-State LiDAR
MEMS-based solid-state LiDAR is an advanced LiDAR system that uses MEMS mirrors, small mirrors made using microfabrication technology, to control the scanning direction of laser lightThis MEMS mirror reacts very quickly in response to electrical signals.Taking advantage of this property, it is possible to scan the environment at high speed while changing the direction of the laser.
Some features of MEMS-based solid-state LiDAR sensors include:
- The direction of the laser can be quickly moved at speeds of less than milliseconds
- About 1/10th the size and weight of conventional LiDAR sensors
However, this technology is not without its disadvantages as we will be seeing soon
Due to the fine structure of MEMS mirrors, they are more vulnerable to physical shocks,There are also physical limits to the movement of the mirror, which may limit the range that can be scanned.
In addition to this, they are also sensitive to external environments such as extreme temperatures and vibrations.
Real World Applications of LiDAR Scanners
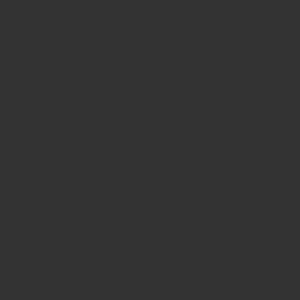
Now that we know of the two types of LiDAR sensors, let us take a deeper look at the real world applications of this technology
- Automobile driving assistance and autonomous driving
- Household robot vacuum cleaners and toys
- Drone navigation and collision avoidance
These features, coupled with the industry wide functionality of this technology make it a perfect choice for applications that require precision and measurement
Some of these benefits include :
Mechanical Rotation Scanning
Mechanical scanning LiDAR is a LiDAR system that uses physical components, such as motors and mirrors, to redirect laser light and scan the environment.This technique is especially prevalent in applications ranging from autonomous vehicles to geographic mapping.
360 Degree Laser Scanning
360 Degree Laser Scanning has a proven track record and reliability, being used in markets such as automobiles, robot vacuum cleaners, and industrial robots.On the other hand, disadvantages include the risk of wear and failure of moving parts and the large size.
The other two types are also used for autonomous driving support, but as of 2023, the mechanical rotation scanning method is gaining the most support.
Two types of LiDAR sensor scanning methods
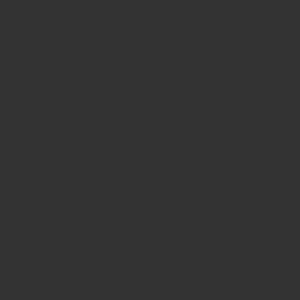
There are various scanning methods for LiDAR sensor technology, but here we will explain the main “TOF method” and “FMCW method”.
TOF method
The TOF (Time-of-Flight) method, which is one type of LiDAR sensor, is a method of determining the distance to an object by measuring the time from the emission of a laser pulse to the detection of its reflection.This system uses a combination of flight time and the speed of light to instantly calculate the exact distance to a target.The TOF Method is especially handy in the following applications :
- Calculating the distance from laser pulse emission and reflection time
- Quick data acquisition
- Long-distance measurement is also possible
However, on the other hand, there are also drawbacks
In particular, there is a risk that measurement accuracy will decrease due to weather conditions such as fog or rain, or external factors such as atmospheric turbulence
It can also be difficult to measure objects that move very quickly or to distinguish between multiple reflections.
Here are some examples of situations where the TOF method is used :
- High Speed Topography Measurement
- Drone adjusts flight path using real-time distance measurement from the air
- Used for car driving support and environmental scanning during autonomous driving
FMCW Method
FMCW (Frequency Modulated Continuous Wave) LiDAR is a distance measurement system that utilizes continuous wave laser technology.In this method, the distance to an object is determined by emitting a laser whose frequency is continuously modulated and measuring the difference between the frequency of the reflected laser and the frequency of the reflected laser.
In addition, by utilizing the Doppler effect, this method can also measure the velocity of an object at the same time.
Features and Benefits of FMCW Technology
- Simultaneously measure distance and object speed by analyzing the frequency shift of reflected signals
- Measures the distance of an object with extremely high accuracy, with a distance measurement accuracy of several micrometers
- Capable of measuring relative velocity of objects
- Even if the pulsed light is disturbed, the distance to the object can be measured based on the degree of frequency change
With that being said, one of its weaknesses is that implementation of this technology requires complex hardware and high-performance equipment.Costs may also be higher when compared to traditional methods.
Now, let us take a closer look at some of the many advantages of LiDAR technology and its use in industry, automation and even medical fields.
The advantages of LiDAR Technology
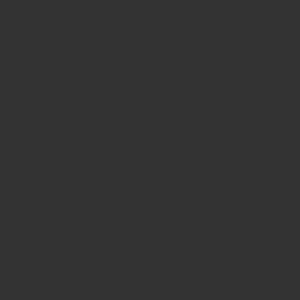
LiDAR tech paves the way to making information more detailed and easier to process allowing for the visualization of complex systems in a very unique way.
Some of these advantages include
- Self-Driving Cars: Accurately detects obstacles and tracks movement for safe navigation
- Production Line Monitoring: Real-time tracking of product position and speed on assembly lines
- Drone Aerial Surveys: Utilizes LiDAR sensors for high-precision 3D mapping during aerial surveys
LiDAR sensors find application across diverse machines, enhancing environmental awareness and navigation abilities, notably in these three domains.
Use of LiDAR Sensors in Drones
Drones equipped with LiDAR sensors are recognized as powerful tools for high-precision 3D mapping.The technology makes it possible to perform measurements over a wide range from 300 meters above the ground and in areas that are normally difficult to access.
Using LiDAR technology on a drone can yield the following advantages
- Accelerated Ground Surveys: Reduces survey duration from days to hours
- Enhanced Data Detail: Provides nearly 100 times more detailed data than ground methods
- Aerial Measurement Flexibility: Measures in challenging terrains like mountains and wetlands from the air
- Reduced Obstacle Interference: Decreases shadow effects of obstacles compared to ground measurements
So what can using LiDAR technology on a drone get us? Let us take a look at some of the practical applications!
- Ecosystem Assessment: Measures tree height, density, and growth for resource management and ecosystem research
- Flood Risk Evaluation: Conducts measurements crucial for assessing flood risks in various areas
- Archaeological Surveys: Collects data on underground ruins and ancient landscapes for research purposes
- Infrastructure Inspection: Checks the condition of power lines, roads, etc., aiding in early problem detection and maintenance planning
- Mining Evaluation: Assesses mining status and estimates remaining resources for resource management purposes
LiDAR use in Logistics and Warehouse Robots
The reason why logistics and warehouse robots are equipped with LiDAR sensors is to support complex tasks in that area.These robots must operate efficiently in environments where a large number of goods and equipment are located.
LiDAR enables high-precision environmental mapping and obstacle avoidance in such environments.
Companies like Amazon use technology like LiDAR to keep their inventory and warehouse organized.
Advantages of LiDAR Sensors on Logistics Robots:
- Precision in Obstacle Detection: Accurate positioning of obstacles and shelves becomes achievable
- Real-time Safety: Instantly detects and avoids collisions with people and other robots during operations
- Robust Data Acquisition: Provides highly accurate data even in low-light conditions or at night
Applications of LiDAR Sensors in Logistics Robots:
- Efficient Item Identification: Accurately identifies and efficiently picks up items
- Automated Transport: Enables automated transportation of warehouse products
- Inventory Optimization: Optimizes inventory management and enhances space utilization within the warehouse
Use of LiDAR Sensors in Automobiles (Self-driving Vehicles)
LiDAR sensors are playing a central role in the evolution of autonomous driving technologyLiDAR installed in self-driving cars uses its environmental recognition ability to support safe driving on the road.
Advantages of LiDAR Sensors in Autonomous Driving
- Real-Time Obstacle Detection: Identifies vehicles, pedestrians, bicycles, etc., ensuring real-time detection of obstacles
- Unexpected Obstacle Recognition: Detects unexpected obstacles, recognizes lanes, intersections, and exits accurately
- Highly Accurate Distance Measurement: Enables precise distance measurement with high accuracy
- Reliable Data in Challenging Conditions: Provides consistent data even during low-light conditions, at night, and in changing weather like rain and fog
With so many potential benefits, its no wonder that a lot of Fortune 500 companies use LiDAR in their operations,
Here are some examples of companies that use LiDAR in their day to day business.
- Waymo: Conducts advanced self-driving technology research and development utilizing numerous LiDAR sensors
- Uber: Researching autonomous driving tech and focusing on environmental recognition with LiDAR sensors
- Aptiv and Hyundai: Collaboratively developing sensor fusion tech centered on LiDAR technology
Let’s take a look at some of the Benefits of LiDAR Sensors when it comes to autonomous vehicles
- 3D Image Acquisition: Offers the ability to obtain detailed 3D images of the environment
- Long-Range Detection: Capable of detecting objects over considerable distances
- Weather Robustness: Less affected by adverse weather conditions compared to other sensors
LiDAR has several distinct advantages over traditional ultrasonic sensors
LiDAR lasers have extremely short wavelengths of 905nm and 1550nm, allowing for highly accurate mapping (approximately 9,500 times finer than ultrasound). Laser measurement uses light, so it is effective not only for hard and flat objects but also for soft objects and sound-absorbing materials.Advantages of using LiDAR Sensors in 3D Scanning
- Long-Distance Detection: Accurately measures distance to objects hundreds of meters away
- Wide Range and High Accuracy: Capable of highly accurate detection from several to hundreds of meters
- Real-time Response: High-speed data acquisition enables instant responses
- Weather Resistance: Highly resilient in adverse weather like fog or rain due to its optical technology
To properly understand these key differences in 3D Mapping, let us look at a comparison of LiDAR Sensors with Ultrasonic Sensors.
LiDAR vs Ultrasonic
LiDAR excels in long-distance detection and robustness in varying weather conditions compared to ultrasonic sensors.Ultrasonic sensors are optimized for shorter distances, typically from centimeters to several meters.
Disadvantages of LiDAR Sensors in 3D Scanning
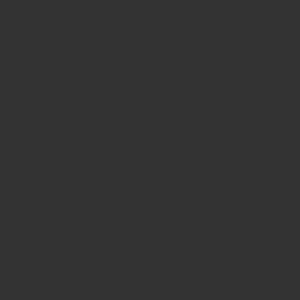
- Large Data Generation: High-resolution scanning produces massive data requiring substantial processing power
- High Power Consumption: Demands increased power proportional to data acquisition, affecting device temperature and reducing drone flight time
- High Cost: LiDAR sensors are pricier due to advanced technology, numerous components, and intensive research and development
What are you sacrificing for these features?
While LiDAR has remarkable precision and weather resilience, its data volume, power consumption, and cost pose trade-offs that must be considered based on specific applications and environments. You should carefully consider the trade-offs between these strengths and price and other disadvantages.How to choose a LiDAR Sensor | 7 points to consider
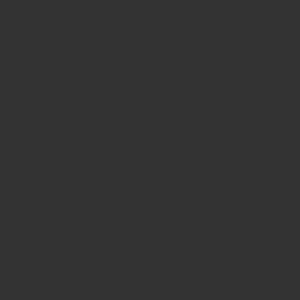
LiDAR sensors are increasingly being used in various fields due to their high accuracy and detailed 3D mapping capabilities.
However, no single LiDAR sensor is suitable for all applications.
Scanning Range
- Choose based on application needs
- Mechanical scanning: 360-degree measurement but slower
- Solid-state scanning: Quick processing but limited range
Prioritize Precision and Speed
-
High-speed scanning suits dynamic environments but poses challenges in data handling and power consumption.
Slow scan speed allows detailed mapping but limits tracking in dynamic scenarios.
Scanning Environment
- Laser types and wavelengths impact data accuracy
- Near-Infrared Laser (NIR): Safe, long-distance detection for topographic surveys and city modeling
- Green Laser: Ideal for underwater surveying and shallow water mapping
- Mid-Infrared Laser (SWIR): Specialized in identifying chemical properties for mineral mapping and industrial monitoring
Laser Strength
- Strong lasers offer long-distance detection, high-resolution mapping, and adaptability in bad weather
- Weak lasers are safer but have limited detection distance and resolution
LiDAR Sensor Size
Consider dimensions based on the intended use and installation area.LiDAR Sensor Cost
Evaluate cost relative to performance and application needs.Certifications
Obtain necessary certifications for legal compliance in the country of use. Understanding these factors helps in choosing the right LiDAR sensor for specific applications, optimizing data collection, and ensuring efficient execution. The world of LiDAR technology involves various components and considerations crucial for optimizationLaser diodes determine output intensity and wavelength, while lenses and collimators regulate laser spread and focus
The power supply unit, driver circuit, and optical filter influence output stability and light passage based on specific wavelengths.
LiDAR Sensor Size
Choosing the right size sensor hinges on several factors.There are benefits to both large as well as small sensors.Let us take a look at some of these features :
Large Sensors Advantages :
- High performance and resolution suitable for detailed data acquisition like topographic surveys and large-scale 3D modeling
- Larger LIDAR sensors generally have the capacity for more powerful lasers and better optics. This translates to higher accuracy in distance measurements and a finer resolution
Large Sensors Disadvantages:
- Challenging to attach to moving objects
- Higher price and increased power consumption
Small Sensors Advantages:
- High installation flexibility, affordability, and energy efficiency
- Used in drones, vehicle sensors, and indoor navigation
Small Sensors Disadvantages:
- Reduced measurement ability compared to larger sensors due to complex circuitry
- Quality concerns due to mass production may impact durability and additional feature integration
What is the cost of LiDAR Sensors?
Sensor prices correspond to their specifications and performance, with expensive sensors offering advanced features like high performance, reliability, and suitability for demanding tasks such as high-resolution and long-distance measurements,Conversely, cheaper sensors, while reducing initial investment, may lack the necessary resolution and durability.
Components Affecting Cost
Depending on the requirements of the machine, several internal components can vary and influence the final cost; components such as- Laser oscillator: Output strength determines price
- Photo Detector: Sensitivity impacts cost
- Galvano and MEMS mirrors: Scanning speed is proportional to cost
- Optical lenses: High-quality materials drive up costs
- Certification for LiDAR Sensors:Obtaining certification in the target market ensures compliance with safety standards and legal requirements
- Ensuring laser safety for users and the environment
- Meeting import and sales regulations
- Demonstrating reliability and quality to consumers and business partners
It’s crucial for:
Manufacturer Comparison
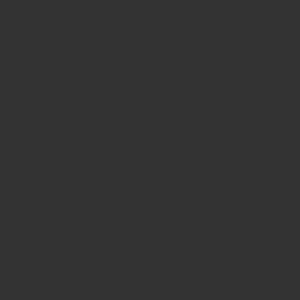
Now that we have learnt so much about LiDAR, perhaps you are interested in researching some prominent companies who employ the use of LiDAR in their operations.
Several manufacturers are pioneering LiDAR technology across various sectors.
Some of the best manufacturers as recommended by us are as follows :
Technology | Konica Minolta | Kokyo | BEA Japan | Optex FA | Ouster Systems |
---|---|---|---|---|---|
Mechanical LiDAR | ✓ | × | × | × | ✓ |
Solid state Optical phase LiDAR | ✓ | ✓ | ✓ | ✓ | × |
Solid state MEMS-based LiDAR | × | ✓ | ✓ | ✓ | × |
Konica Minolta
Develops LiDAR sensors with high accuracy and reliability using optical phase technology.The company’s LiDAR sensors are used in fields such as self-driving cars, robots, and drones.
The company manufactures optical phase LIDAR suitable for detection, yet can acquire information with a resolution of up to 0.03mm.
Kokyo Co., Ltd.
Kokyo is a Japanese LiDAR sensor manufacturer founded in 2009. Headquartered in Minato-ku, Tokyo, they have offices all over the world.The company manufactures MEMS-based LiDAR sensors suitable for detection, achieving a resolution of 0.03m and a measurement distance of up to 300m.
They are deploying high-performance, low-cost LiDAR sensors, which are increasingly being adopted in advanced technology fields such as self-driving cars, robots, and drones .
BEA Japan
BEA Japan is a company that develops, manufactures, and sells LiDAR sensors in Japan.The company’s optical phase LiDAR is particularly used for surveying using drones, AGVs (unmanned transportation robots), and autonomous driving.
BEA Japan is recommended if you require high-precision measurement and surveying such as 3D mapping using drones and AGVs.
Optex FA
Optex FA is a company with many years of experience in the development, manufacturing, and sales of laser displacement sensors. Laser displacement sensors are also applied in LiDAR sensors.The strength of the company’s LiDAR sensor is its laser displacement sensor technology, with a measurement accuracy of about ±0.1mm. A typical LiDAR sensor has an accuracy of about ±1mm, so Optex FA’s LiDAR sensor is about 10 times more accurate than average.
Ouster Systems
Ouster focuses on mechanical LiDAR, offering small, lightweight sensors with industry-leading performance.Ouster Systems’ LiDAR sensors are being introduced in a wide range of fields, from self-driving cars to robotics to agriculture and infrastructure-related industries, and in 2022 Ouster Systems’ LiDAR sensors were acquired by Geely, a major Chinese automaker.
Each manufacturer has unique technologies catering to diverse industries like self-driving cars, robotics, and drones, setting benchmarks in LiDAR technology.
Purchasing your own LiDAR Sensor
At JET Global, we are committed to helping you find the best machine that suits your business needs.If you have any questions regarding any of the topics mentioned in today’s article, please feel free to reach out to us via our Contact Page.
Our team of specialists would be happy to help with your questions.
Contact Us Today