切断ロボット
複雑化する加工ニーズや高精度なエッジ品質への要求に応える手段として、切断ロボットの導入を検討する企業が増えています。しかし、レーザー・プラズマ・ウォータージェットなど多様な切断方式が存在し、さらにメーカーごとの特徴も異なるため、自社に最適な機種の選定は一筋縄ではいきません。
本記事では、切断ロボットの定義や方式ごとの特性を解説したうえで、選定時に押さえるべき技術的視点や現場条件を整理し、代表的なメーカーの特徴と導入事例を比較紹介します。
これから切断ロボットの導入検討を始める方も、選定段階で迷っている方も、本記事を通じて判断材料を体系的に得られるでしょう。
目次
切断ロボットとは? 基本情報や導入事例を紹介
切断ロボットとは、製造現場で金属や樹脂などのワークを切断する作業を自動で行う産業用ロボットの一種です。
切削ロボットには、レーザー、プラズマ、ガス、ウォータージェットなどの様々な切断手法があります。また、ワークを削り取って成形する切削ロボットとは別物です。
切断ロボットは、自動車、造船、航空機、建設機械、金属加工など、多岐にわたる業界で活用されており、人手不足の解消や生産性向上、加工精度の安定化を目的として導入が進んでいます。
実際の導入事例としては、以下のようなものがあります。
- 自動車メーカーにおける車体外板の3Dレーザー切断
- 造船所での厚板鋼材のプラズマ切断
- 航空機製造ラインにおける複雑形状部材のウォータージェット切断
各現場では、従来の手作業では困難だった加工を高精度かつ安全に実施できるようになっています。
また、切断と似た概念として溶断がありますが、次章では、切断と溶断の違いを整理します。
溶断と切断の違いを確認しておこう
切断と溶断は、どちらもワークを分離する手段を指し、溶断は切断の一種になります。
まず、溶断は高温の火炎やアークを使って素材を部分的に溶かし、その溶融部を除去することで切断する方法です。溶断は主に鉄鋼や金属厚板に用いられ、特にガス溶断やアーク溶断が代表的です。
また、溶断で使われる熱エネルギーを使った方法以外にも、ワークを分離する方法はあります。例えば機械的な力を使った剪断やウォータージェットなどがこれにあてはまり、これらも切断の一種です。
つまり、切断とは、レーザー等の熱エネルギー的な力を使った溶断や、ウォータージェット等の物理的な力で分離する方法など、ワークを分離するための技術の総称です
切断の概念や切断ロボットの基本情報が分かったところで、次章では切断ロボットの種類分けを解説します。
切断方法でロボットを種類分けして解説
切断ロボットは、活用する切断方法によって種類分けできます。それぞれの切断方法にメリット・デメリットがあるので、本章ではそれらも合わせて解説します。
レーザー切断
レーザー切断は、高出力レーザービームをワークに照射して局所的に加熱・溶融・蒸発させ、素材を切断する方式です。
主に薄板や複雑な形状の精密加工に強みがあり、非接触かつ高精度な切断が可能です。ただし、反射率の高いアルミや銅などの素材には不向きで、レーザー装置自体の導入コストも高い傾向があります。
※従来のCO2レーザーでは難しかったが、近年のファイバーレーザーでは反射素材への対応も可能になっている。
ガス切断
ガス切断(酸素・アセチレンなどによる溶断)は、金属を局所的に加熱し酸化反応を利用して切断する方法です。
主に鉄鋼などの厚板切断に使用され、設備コストが低いのが特徴です。ただし切断面は粗く、加工速度も他方式より遅い傾向にあります。
プラズマ切断
プラズマ切断は、ガスを高温・高圧でプラズマ化し、その熱で金属を溶融して高速で吹き飛ばすことで切断します。
中厚板までの切断に適しており、ガス切断よりも高速かつ高精度な加工が可能です。ただし、やや熱変形のリスクがあり、消耗部品の定期交換も必要です。
プラズマ切断ロボットについてより詳しく知りたい方は、プラズマ切断ロボットに特化した以下の記事をご覧ください。
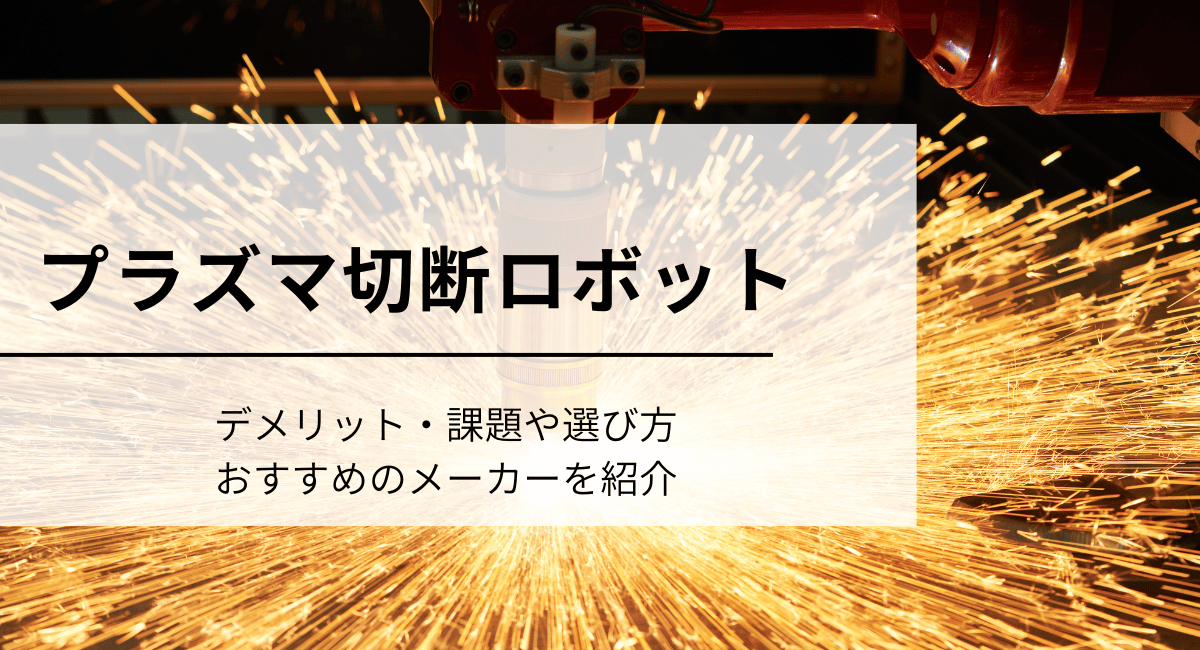
ウォータージェット切断
ウォータージェット切断は、高圧水流に研磨材を混ぜて噴射し、ワークを削り取る方式です。
熱を使わない「冷却切断方式」であるため、熱に弱い素材や複合材の加工に適しています。ただし、設備が大型化しやすく、ランニングコストも高めです。
自社の目的に適した種類の切断方法は見極められたでしょうか? はっきりとしない場合は、まず自社の導入目的や予算、設置スペースなどを改めて整理しましょう。
次章では、切断ロボット選定のポイントを解説します。ここまでで自社に適した種類は分かっても、具体的な製品選定には他のポイントも重要なので、ぜひご覧下さい。
切断ロボットの選定で重視すべき3つのポイント
切断ロボットにも多くの製品があるため、自社に適した製品を導入できないと、ロボットの導入がかえって効率を悪化させてしまいかねません。
そのため、本章で選定のポイントを確認して、できるだけ導入失敗が起きないようにしておきましょう。
ワーク材質・板厚・仕上がり品質に応じた切断方式の選定
切断ロボットを導入するにあたって基本的な選定ポイントの一つが、ファイバレーザ・CO₂レーザ・プラズマ・ウォータージェットなどの切断方式を、加工対象の材質や板厚、そして要求されるエッジ品質に合わせて適合させることです。
この選定は、母材の熱伝導率や反射率、最大切断厚、さらに溶接や接着といった後工程の有無といった要因によって左右されます。
もし方式選定を誤ると、バリ除去や熱歪みの補正など余計な後処理が発生し、タクトタイムの延長や歩留まりの低下といった生産効率への悪影響が避けられないでしょう。
特に、多品種少量生産や異種材の混流が求められる生産ラインでは、段取り替えの最小化を実現するうえでもこの観点は重要です。
最適な切断方式の切断ロボットを見極めることで、後処理工程を省きつつエネルギーコストも抑えられ、ワンパスでの高品質加工が可能となります。
熱影響とスラグ生成を最小化できる熱プロセス制御性能の比較
特に熱を用いた方法の切断ロボットを選定する場合は、ヘッドの光学制御性能やパルス制御機能、アシストガスの種類と圧力設定によって、熱影響層(HAZ)やスラグの生成をいかに抑えられるかが大事な比較軸となります。
この制御性能は、ビーム径や切断速度、ノズルの冷却能力といった構成要素によって変動し、導入機種ごとの仕様差が品質に直結します。
これを軽視すると、スラグの残留や熱変質によって部品強度が低下し、微細なクラック発生や検査不合格によりロット単位での廃棄リスクが高まる可能性があるでしょう。
特に、無熱工法を採用できず、材料特性を保ったまま加工する必要がある航空機部品や医療機器部品などの製造ラインでは、この観点を無視することはできません。
適切な熱プロセス制御機能を備えた切断ロボットを選ぶことで、追加の熱処理や研磨工程を省きながら、初回の加工のみで品質検査をクリアし、出荷までのリードタイムを短縮可能です。
消耗部品の寿命とメンテナンス性を考慮した総運用コスト評価
切断ロボットの選定では、ノズルやレンズ、シールといった消耗部品の耐久性と、それらの交換作業のしやすさも見逃せません。
これらの項目は、1日に処理するカット総距離や対象材質の不純物含有率、さらには部品の補充体制と供給リードタイムといった運用条件によって変わります。
もし部品の交換頻度が高く、しかも工具を使わないと交換できないような構造であれば、1回の停止ごとの作業時間(MTTR)が増加し、結果的に稼働率が下がってしまいます。
特に、24時間体制での連続運転や、段取り替えの猶予がごく限られた量産工場においては、この視点を重視しないと月間の生産計画を満たせなくなるリスクが高まるでしょう。
そのため、耐久性の高い部品と工具不要で素早く交換可能な機構を持つ切断ロボットを選べば、安定した高稼働を維持しながら、部品費用も平準化され、短期間での投資回収が見込めます。
上記を参考に、各企業が自社に適切な製品を選定していくことを願っております。次章では、編集部がおすすめする切断ロボットのメーカーをピックアップして紹介するのでぜひご覧ください。
編集部おすすめの切断ロボットの代表的なメーカーを紹介
本章では、切断ロボットを製造している数あるメーカーから、当編集部がおすすめするメーカーを数社に絞って紹介します。ぜひご一読ください。
※JET-Globalの問い合わせフォームに遷移します。
※一部会社とは提携がない場合がありますが、ユーザー様に最適なご案内ができるよう努めています。
- 川崎重工業 / Kawasaki Heavy Industries
- ダイヘン / DAIHEN
- ファナック / FANUC
※クリックすると該当箇所まで飛びます
川崎重工業 / Kawasaki Heavy Industries
会社名 | 川崎重工業 / Kawasaki Heavy Industries |
設立年 | 1896年 |
本社 | 東京都港区海岸1丁目14-5(東京本社) 兵庫県神戸市中央区東川崎町1丁目1番3号 神戸クリスタルタワー(神戸本社) |
概要 | 重工業・産業用ロボットの大手メーカー |
川崎重工業は、6 軸ロボットにレーザ・プラズマヘッドを組み合わせる加工パッケージと、CAD 形状から切断経路を自動生成するオフラインソフト KCONGを一体提供し、厚板から成形部品まで多様なワークを高精度かつ高スループットで切断できる総合エンジニアリング力を強みとするメーカーです。
同社の切断ロボットである「RS020N」は、20 kg 可搬・1 725 mm リーチの 6 軸アームに ±0.05 mm の繰返し精度と 11.5 m/s の高速動作を備え、IP65 本体/IP67手首の防塵防滴設計によりレーザ・プラズマ切断ヘッドを搭載しても高精度パス追従と長時間連続運用を両立できる点が特徴です。
同製品は、船舶ブロックの輪郭切断や建機フレーム・自動車プレス部品のトリミング、鋼板・アルミ形材のネスティング切断など、造船・建設機械・自動車/金属加工各業界の切断工程に導入されています。
ダイヘン / DAIHEN
会社名 | ダイヘン / DAIHEN |
設立年 | 1919年 |
本社 | 大阪府大阪市淀川区田川2丁目1番11号 |
概要 | 溶接機器、産業用ロボット、クリーン搬送ロボットなどを手掛ける総合FA機器メーカー |
ダイヘンは、ロボット本体・高性能レーザ/プラズマ電源・CAD連携オフラインCAM「FD-ST」を自社で一体開発し、切断プロセスのプログラム生成から電源制御・ロボット制御までワンストップで最適化できる総合エンジニアリング力を強みとするメーカーです。
同社の切断ロボットである「FD-A20」は、20 kg 可搬・2 m クラスのリーチを持つ6軸高精度アームにより、直線±0.15 mm・φ10 mm円弧±0.10 mmの軌跡精度でレーザ切断を行え、主要レーザ発振器インターフェースと CADから切断経路を自動生成するオフライン CAM「FD-ST」を標準装備して段取りを短縮できる点が特徴です。
同製品は、自動車ボディのテーラードブランクや超ハイテン材トリミング、EV バッテリーケースの高精度開先切断など、自動車・金属加工・電装部品業界のレーザ切断工程に導入されています。
ファナック / FANUC
会社名 | ファナック / FANUC |
設立年 | 1972年 |
本社 | 山梨県南都留郡忍野村忍草3580 |
概要 | FA機器、ロボットのメーカー |
ファナックは、CNC・サーボ制御を自社開発してロボットに統合し、高剛性アームと加工用パス制御ソフトを組み合わせて多用途切断セルを短期間で構築できる総合エンジニアリング力を強みとするメーカーです。
同社の切断ロボットである「M-800iA/60」は、60 kg可搬・2 040 mmリーチの6軸アームに±0.1mmのパス精度とIP67耐環境性を備え、レーザやウォータジェットヘッドを搭載して厚板や複雑形状ワークを高速・高品位に切断できる点が特徴です。
同製品は、自動車車体パネルのトリミング工程や重機・建設機械部品の輪郭切断、航空機用複合材の高精度カッティングなど、自動車・建設機械・航空宇宙を中心とした金属/複合材加工業界に導入されています。
切断ロボットのカタログ
切断ロボット関連記事
切断ロボット関連記事はまだありません。