RGV
RGV(Rail Guided Vehicle)は、工場や倉庫における物流の効率化を担う自動搬送システムとして注目を集めています。「どの搬送ロボットを選べばよいかわからない」「RGVとAGVの違いが曖昧」「導入前にどんな課題があるのか知っておきたい」こうした悩みを抱える現場担当者の方も多いのではないでしょうか。
本記事では、RGVの基礎知識から他ロボットとの違い、安全対策、導入のメリット・デメリット、さらには選び方やおすすめメーカーまでを網羅的に解説します。導入を検討している方にとって、判断の軸が明確になる内容が満載です。
「この一記事でRGVのおおよその全体像がわかる」そんな網羅性の高いガイドとなるよう、実務視点で構成しましたので、ぜひ最後までご覧いただき、最適な自動搬送システム選びにお役立てください。
目次
RGVとは? 基本情報やAGVとの違い、実際の事例も紹介
RGV(Rail Guided Vehicle)とは、レール上を走行する無人搬送車のことです。有軌道無人搬送車とも呼ばれています。自動倉庫や製造ラインなど、一定のルートで高頻度に搬送が発生する現場でよく使用されており、
物理的に設置されたレールをガイドとして走行するため、安定性・高速性・繰り返し精度に優れ、重搬送にも対応可能です。
AGVとの違い
AGV(無人搬送車)は磁気テープやレーザー誘導などの非物理的なガイドで走行するのに対し、RGVはレールで軌道が明確に決まっています。 そのため、以下のような違いがあります。
- RGV:軌道が必要なためルートが固定だが走行が高速で重荷重に対応しやすい
- AGV:軌道は必要ないためルート変更が可能でフレキシブルだが速度や精度はRGVに劣る
ほかにもAGVは割込搬送可能だが、RGVは順次走行のため割込搬送は不可であったり、AGVはルート上に障害物がある場合迂回ルートを判断して目的地に到達できる一方、RGVは軌道上の障害物は回避できないなどの違いも存在します。
AGVについて詳しく知りたい方は以下をご覧ください。
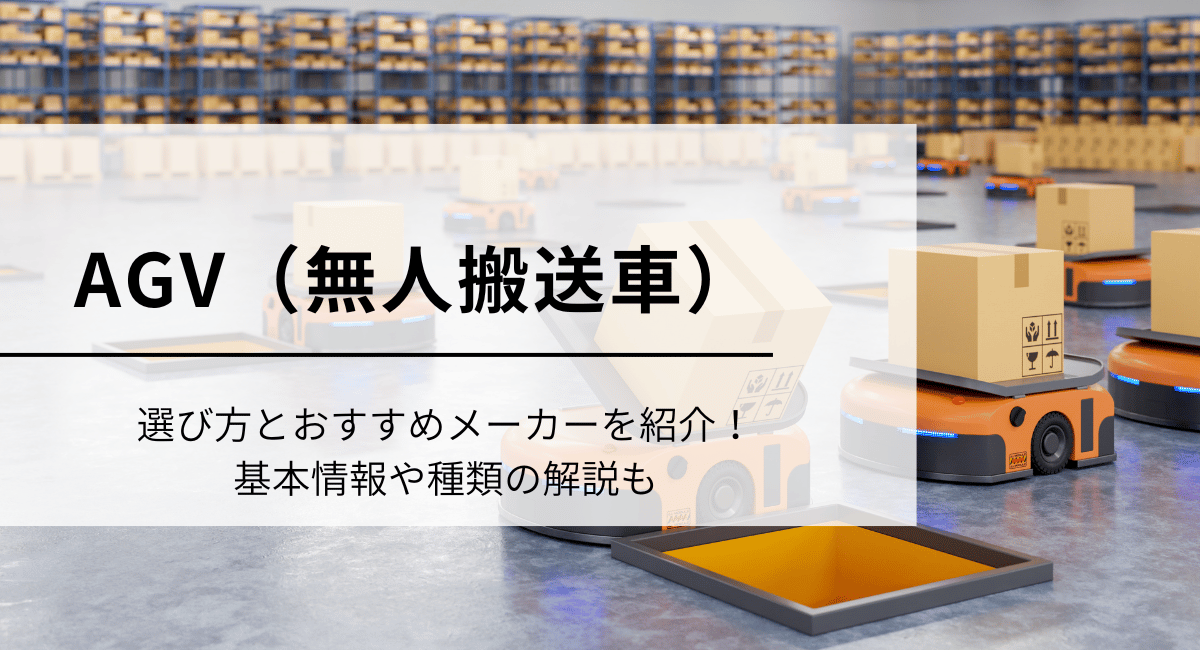
実際の導入事例
RGVは以下のような現場で導入されています。
- 製造業のライン間搬送:部品の供給をタイムリーに実施
- 大型倉庫間のパレット搬送:重量物を自動で長距離移動
- クリーンルーム環境:埃を巻き上げずに安定走行
次は、RGVを安全に運用するために必要な対策について詳しく解説します。
RGVの安全対策はどのようにして行うのか
RGVの安全対策は、工場や倉庫などでの人的接触リスクを低減し、安定した自動搬送を維持するうえで不可欠です。そのためには機械面とシステム面の両方からの対策が求められます。主な安全対策には以下のようなものがあります。
- 非常停止ボタンの設置
- レーザーセンサーやバンパーによる障害物検知
- 周囲への警報音・ライトでの接近通知
また、制御ソフトウェア側でも安全運転速度の設定、ゾーン制御(特定区域での走行制限)、複数台運用時の干渉回避アルゴリズムなどを活用し、衝突や暴走のリスクを抑えています。
安全対策は法規制との整合性も必要です。例えば、ISO3691-4などの国際安全基準や国内の労働安全衛生規則に準拠した設計・運用が推奨されます。
次は、RGVと比較検討されることの多い他の搬送ロボットについて紹介します。
ほかに候補に挙がることの多いRGVと用途の近いロボットの種類
RGV以外にも搬送の自動化を実現するロボットは数多く存在し、それぞれに特徴があります。ここでは代表的な種類とRGVとの違いを比較しながら紹介します。
AGV
AGV(Automated Guided Vehicle)は、磁気テープ、QRコード、レーザー誘導などを用いて走行する無人搬送車です。床面にガイドを敷くだけで導入可能なため、柔軟なルート設計が魅力です。RGVやGTPなどもAGVの一種と言えます。
GTP
GTP(Goods to Person)は棚搬送型ロボットで、保管棚ごと人の作業場所に搬送する仕組みです。主に倉庫業務におけるピッキング作業の効率化に使われます。
AGF
AGF(Automated Guided Forklift)は、無人で稼働するフォークリフト型の搬送機器です。パレット単位の搬送や棚入れ・棚出しに活用されます。
AMR
AMR(Autonomous Mobile Robot)は自律走行が可能なロボットで、カメラやセンサーを使って動的にルートを判断します。環境変化に柔軟に対応できるのが特徴です。
ソーター
ソーターは、荷物を自動で仕分けする装置で、コンベアやベルトを用いた高速仕分けが可能です。主に物流センターで使われています。
次は、RGVを導入したときに得られる具体的なメリットについて見ていきましょう。
使用しなかったときと比べた時のRGV使用時のメリット
搬送作業の自動化と省人化が可能
RGVの利点のひとつは、繰り返し行われる搬送作業を自動化できる点です。
これにより、従来人手で行っていた台車押しやフォークリフトによる移動が不要となり、搬送に割いていた人員を別の作業に回すことが可能になります。 省人化によって労働力不足への対応や、作業員の負担軽減にも直結します。
高精度・高速度な搬送を実現
RGVは物理的なレールを走行するため、走行経路が常に一定でブレがありません。
そのため位置ズレが起きにくく、搬送先での自動積み下ろしや生産ラインとの自動連携がスムーズに行えます。 また、構造上スピードを出しやすく、長距離搬送にも適しています。
作業現場の安全性が向上
人や他の車両との接触リスクが少ない点も魅力です。 RGVはあらかじめ定めたレール上しか走行しないため、不規則な動きをすることがありません。
さらに、非常停止ボタンや障害物検知センサー、接近警報音などを組み合わせることで、安全レベルを高めることができます。
長期的な搬送コストを削減
初期導入には設備投資が必要ですが、日常的な人件費や作業ミスによるロスを減らすことが可能です。
さらに、耐久性が高く長期運用を前提とした設計が多いため、メンテナンスコストも抑えやすく、TCO(総所有コスト)で見れば非常に効率的です。
次は、RGV導入前に知っておきたいデメリットや課題について整理します。
導入前に念頭に置いておくとよいRGVの課題やデメリット
初期導入コストが高い
RGVはレールに依存するため、導入時に施設内の構造に応じてレイアウト工事が必要です。
これに伴い高額な初期費用が発生することが多く、柔軟に導入できるAGVなどと比べるとコスト面でハードルを感じるケースがあります。
柔軟なルート変更に対応しづらい
レールが固定されているため、運用変更に柔軟に対応できません。 例えば搬送ルートを一時的に変えたい場合でも、物理的な制限があるため、柔軟な再設定が困難です。 頻繁に運用形態が変わる現場には不向きでしょう。
専門的な保守管理体制が必要
RGVシステムは、搬送体だけでなくレール、制御盤、ソフトウェア、センサーなど複数の要素から成り立っています。
それらの保守には専門知識が必要であり、内製化する場合は人材育成が必要ですし、外部委託の場合はコストが発生します。
レール敷設に一定のスペース確保が必要
狭小な現場や既存設備が密集している工場などでは、レールを敷設するスペースを確保できないケースもあるため、注意が必要です。また、レイアウトの自由度が制限されるため、新設時には綿密な設計が求められます。
このように、RGVはメリットの多いシステムではあるものの、現場特性や将来の運用方針を見据えたうえで慎重に検討する必要があります。
RGVを選ぶ際に押さえておきたい重要な視点
RGVは搬送の自動化を支える中核的な設備ですが、現場ごとの特性に合わせた選定を行わなければ、想定以上の運用コストや非効率な結果を招くおそれがあります。ここでは、選定時に特に重視すべき3つのポイントを紹介します。
走行速度と加速度のバランス
RGVの選定ポイントとして、走行速度と加速度のバランスが挙げられます。走行速度工場や倉庫の作業フロー、搬送対象の距離、求められるタクトタイムなどに左右されます。
仮にこの要素を十分に検討せず選定してしまうと、必要以上に搬送時間がかかってしまい、作業効率が落ちるばかりか、生産計画全体に影響を及ぼす可能性も否定できません。特に、多品種少量生産で頻繁な搬送が発生する現場や、短時間で繰り返しの移動が求められる環境では、この点は慎重に検討する必要があります。
最適な速度設定により、無駄な時間を省き、作業の流れをスムーズにすることができるため、生産性の向上につながります。
レール配置の柔軟性
RGVの選定において、レール配置の柔軟性も重要な視点です。この判断には、現場のレイアウト構成や将来的なレイアウト変更の予定が影響します。
もしレールの配置が現場に適さず、再配置も難しい構造だった場合、搬送効率が低下したり、運用の妨げになったりする恐れがあるため、注意しましょう。特に、定期的にライン構成を変更したり、設備の入れ替えを行ったりするような現場では、この点を無視すると柔軟性が損なわれます。
工場や倉庫のレイアウト変更に合わせてRGVを簡単に再配置でき、長期的に利用可能となるという視点は、持続可能な設備投資を実現するためにも重要です。
安全機能の充実
忘れてはならないのが、安全機能の充実です。施設内での人との接触リスク、他機器との混在運用、あるいは可動域の重複などの状況に依存します。
十分な安全機能が備わっていないRGVを導入した場合、万が一の接触事故や物損リスクが高まり、運用停止や人的損失につながる可能性もあります。とりわけ、作業員がRGVの走行ルート近くで作業するような構内環境では、避障センサーや非常停止装置、音声・光による警告機能の有無が重要です。
安全性を確保することで、事故のリスクを減らし、安心して運用できるため、安定稼働と企業リスクの低減に貢献します。
次は、主要なRGVメーカーについて、それぞれの特徴を踏まえて紹介していきます。
編集部がピックアップするおすすめのRGVメーカーを紹介
RGV(Rail Guided Vehicle)を導入する際、どのメーカーを選ぶかは導入後の運用効率や保守性に関わります。ここでは、国内の代表的なRGVメーカーを紹介します。それぞれの特徴を把握し、自社の用途や現場環境に最も適したメーカー選定の参考にしてください。
※JET-Globalの問い合わせフォームに遷移します。
※一部会社とは提携がない場合がありますが、ユーザー様に最適なご案内ができるよう努めています。
- 三菱ロジスネクスト / Mitsubishi Logisnext
- 村田機械 / Murata Machinery
※クリックすると該当箇所まで飛びます
三菱ロジスネクスト / Mitsubishi Logisnext
会社名 | 三菱ロジスネクスト / Mitsubishi Logisnext |
設立年 | 1937年 |
本社 | 京都府長岡京市東神足2-1-1 |
概要 | 総合物流機器メーカー |
三菱ロジスネクストは、無人搬送車(AGF)を含む多様な物流機器の設計・製造において長年の実績を誇り、業界全体をけん引してきた総合物流機器メーカーです。
同社が提供する代表的なRGVには、ムジンカーやレーザー誘導AGFなどがあり、用途に応じた多彩なラインアップが揃っています。日本初の無人搬送車を開発した実績を持ち、走行の安定性と堅牢性に定評があります。
同製品は自動車部品、食品、化学薬品など、多岐にわたる製造現場で、従来はフォークリフトや牽引車が担っていた搬送作業を自動化し、生産性の向上と構内の接触事故リスク低減に貢献しています。
村田機械 / Murata Machinery
会社名 | 村田機械 / Murata Machinery |
創業年 | 1935年 |
本社 | 京都市伏見区竹田向代町136 |
概要 | 総合機械メーカー |
村田機械は、ロジスティクスやFA分野で数多くの自動搬送システムを手がけており、高度な走行制御技術に定評がある老舗の総合機械メーカーです。
ラインナップにはAGV PremexやPremex XIO、RTN-Xといった高性能な搬送機があり、現場ごとに最適なモデルを選定できます。制振制御や高精度な停止制御技術により、正確な荷物搬送と安定した運用が可能です。
同製品は半導体工場や大規模倉庫など、より高速・高精度が求められる固定ルートの基幹搬送を担っています。
RGV全製品
RGVの製品はまだありません。
RGVのカタログ
RGV関連記事
RGV関連記事はまだありません。