超音波はんだ付けロボット
多くの製造現場共通の課題のひとつに、ガラス等難接合材へのはんだ付けとフラックス洗浄廃止が挙げられます。
この解決策のひとつが、超音波はんだ付けロボットです。超音波で材料表面を活性化し、フラックス不要で直接接合を実現します。
ただし、その効果を最大限引き出すには技術特性や選定基準の理解が必要です。知識不足は、不適切な機種選定や運用トラブルによる接合不良、コスト増を招き、期待した投資効果を得られないリスクがあります。
そこで本稿では、特徴から種類、難接合材対応、導入注意点、選定ポイント、メーカー情報まで解説することで、最適なロボットを選定し、導入失敗リスクを抑え、投資効果を高めるための具体的な知識を提供します。
貴社の自動化、生産性・品質向上の可能性がありますので、是非ご一読ください。
また、JET-Globalでは、超音波はんだ付けロボット以外にもはんだ付けロボットを解説しています。はんだ付けロボット全体について詳しく知りたい方は、以下の記事をご覧ください。
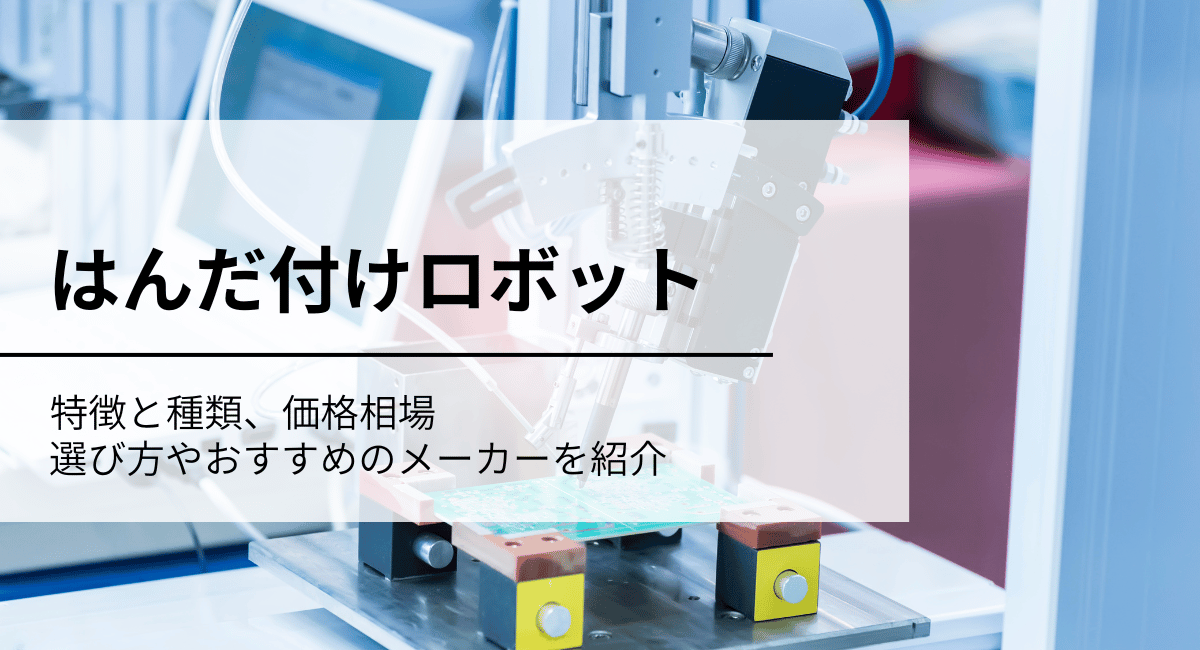
また、JET-Globalでは実際に、超音波はんだ付けロボットの導入支援も行っております。
超音波はんだ付けロボットの専門家による製品の選定から補助金の活用、ロボット研修による社内人材の育成まで、超音波はんだ付けロボット導入をあらゆる面からサポートいたします。
「一度ロボットを触ってみたい」や「こんな自動化ができるか知りたい」などの軽い相談も可能です。
相談は無料ですので、関心のある方は以下のサービス詳細をご覧ください。
目次
超音波はんだ付けロボットとは? 特徴や活用例などを解説
超音波はんだ付けロボットは、はんだ付けプロセスに超音波振動を利用する自動化装置です。
通常のはんだ付けでは、金属表面の酸化膜を除去し、はんだの濡れ性を向上させるために「フラックス」と呼ばれる化学薬品を使用します。
フラックスは確かにはんだ付けに有効ですが、それに伴うリスクも無視できません。はんだ付け工程後にフラックス成分が基板などに残留した場合、これが湿気と反応するなどして金属部分の腐食や絶縁性の低下を誘発し、時には回路ショートといった深刻な不具合につながる恐れがあります。
しかし、超音波はんだ付けにおいては、はんだごてやはんだ槽からの超音波振動によって溶融はんだ内にキャビテーションが発生します。この現象(微細な気泡の発生と消滅)が物理的な作用を及ぼし、接合面の酸化膜や汚れを効果的に破壊・除去するのです。
これにより、フラックスを使用せずとも、清浄な金属表面を露出し、はんだを直接接合させることが可能になります。この「フラックスが不要」な点が、超音波はんだ付けの最大の特徴です。
また、フラックスが不要になることで、以下のようなメリットが生まれます。
これらの特徴から、超音波はんだ付けロボットは、電子部品、自動車部品、太陽電池、医療機器、センサー、光学部品など、高い接合信頼性や特殊な材料への接合が求められる分野で活用されています。
一方で、超音波はんだ付けロボットにはデメリットや注意点も存在します。
超音波はんだ付けロボットは、そのユニークな特性により、従来のはんだ付け技術では対応できなかった課題を解決する可能性を秘めています。しかし、導入にあたっては、そのメリットとデメリットを十分に理解し、自社の製品や生産プロセスに適しているかを慎重に検討することが重要です。
ここまで、超音波はんだ付けロボットの特徴とメリット・デメリットを解説しました。
さて、超音波はんだ付けの特徴のひとつが、難接合材へのはんだ付けが可能になる点でした。次に、具体的にどのような材料に対応でき、どのような原理でそれが可能になるのかを確認しましょう。
超音波はんだ付けロボットの難接合材(ガラス、セラミック)への対応を解説
超音波はんだ付けロボットが注目される理由のひとつは、従来のはんだ付け技術では接合が困難だった、いわゆる「難接合材」への対応能力です。ここでは、その原理と具体的な対応材料について解説します。
フラックスレスはんだ付けの原理と難接合材
通常のはんだ付けでは、金属表面に自然に形成される酸化膜が、はんだの濡れ広がりを阻害します。そのため、※フラックスを用いて酸化膜を除去する必要がありました。
※フラックスとは何か気になった方は以下をクリックしてご確認ください。
接合後に残ったフラックスが、腐食や絶縁不良(イオンマイグレーションなど)を引き起こす可能性があるため、多くの場合、洗浄が必要となりこれが製造上のコスト増や手間の要因ともなっています。
しかし、ガラスやセラミックス、アルミニウムなどの材料は、表面に強固な酸化膜や不動態皮膜を形成していたり、そもそも金属ではないため、フラックスの効果が限定的で、はんだ付けが困難でした。
超音波はんだ付けは、この問題を物理的な方法で解決します。溶融したはんだに超音波振動を与えることで、はんだ中に微細な気泡を発生させ、それが激しく生成・消滅を繰り返す「キャビテーション効果」を利用します。このキャビテーションによる衝撃波が、接合対象物の表面にある酸化膜や汚れを物理的に破壊・除去するのです。
これにより、フラックスを使わずに清浄な表面を露出し、活性化された状態を作り出すことができます。この活性化された表面にはんだが直接接触することで、良好な接合が可能となります。
対応可能な難接合材の種類
超音波はんだ付けロボットによって接合可能となる代表的な難接合材には、以下のようなものがあります。
-
ガラス
各種ガラス基板、石英ガラス、光学レンズなど -
セラミックス
アルミナ、ジルコニア、窒化ケイ素、窒化アルミニウムなど -
金属
アルミニウム、ステンレス、チタン、モリブデン、タングステン、ニッケル基合金など -
その他
シリコンウェハー
これらの材料へのはんだ付けは、センサーの電極取り出し、パワー半導体の放熱基板への実装、光学部品の固定、電池タブの接合など、様々な用途で必要とされています。超音波はんだ付け技術は、これらの分野における製品開発や製造プロセスに新たな可能性をもたらします。
ただし、すべての難接合材に対して万能というわけではありません。材料の種類や表面状態、使用するはんだの種類(専用はんだが必要な場合が多い)によって、接合性や最適な条件は異なります。そのため、導入前には十分な接合テストと条件出しが必要です。
難接合材へのはんだ付けにおける注意点
難接合材へ超音波はんだ付けを行う際には、以下の点に注意が必要です。
適切な超音波パラメータの設定
まず、適切な超音波パラメータ(周波数、出力、時間)の設定が重要です。パラメータが不適切だと、接合不良だけでなく、材料自体にクラックなどのダメージを与えてしまう可能性があります。特に、ガラスやセラミックスなどの脆性材料に対しては、過剰な超音波出力は禁物です。
専用はんだの選定
次に、専用はんだの選定です。多くの難接合材に対しては、その材料との濡れ性や反応性を考慮した特殊な組成のはんだ(例えば、亜鉛/チタン系、スズ-亜鉛系、あるいは活性元素を含むものなど)が用いられます。メーカー推奨のはんだや、事前の評価に基づいたはんだを使用することが推奨されます。
最適な接合部設計
さらに、接合部の設計も信頼性を左右する重要な要素です。超音波エネルギーが効率的に伝達され、かつ応力集中が起こらないような接合部の形状や構造を考慮することが、信頼性の高い接合を得るために重要です。
超音波はんだ付けは、従来は接合が困難だったガラスやセラミックス、アルミニウムといった難接合材へのはんだ付けを実現可能にする技術ですが、その能力を最大限に引き出すためには、材料特性とプロセスへの深い理解が必要です。
次に、具体的にどのような種類の超音波はんだ付けロボットが存在するのか、その種類ごとの特性を見ていきましょう。
種類ごとに超音波はんだ付けロボットを解説
超音波はんだ付けロボットは、その構造や用途によっていくつかの種類に分類されます。ここでは代表的な3つのタイプについて、それぞれの特徴、メリット、デメリットを解説します。
直交座標型ロボット
直交座標型ロボットは、3つの直線的な軸(X軸、Y軸、Z軸)が直交することで構成されたロボットです。各軸が独立して動作することで、ロボットの先端はプログラムされた3次元空間内の任意の位置へ正確に移動できます。シンプルな構造でありながら、高い精度と剛性を持ち合わせていることが特徴です。
部品の組み立て、搬送、検査、塗布など、幅広い産業用途で活用されています。
インライン型ロボット
インライン型ロボットは、生産ラインに組み込んで使用することを前提とした超音波はんだ付けロボットです。コンベアなどで搬送されてくるワークに対し、連続的に自動ではんだ付けを行います。
大量生産を行う工場での導入に適しており、高い生産性が求められる場合に選択されます。
多関節ロボット搭載型
多関節ロボット搭載型は、人間の腕のような多関節構造を持つロボットアームの先端に、超音波はんだごてを取り付けたタイプです。複雑な動作が可能で、立体的なワークや狭小部へのはんだ付けに適しています。
自動車部品や筐体内部の部品など、アクセスが難しい箇所へのはんだ付けが求められる場合に有効です。
このように、超音波はんだ付けロボットにはいくつかの種類があり、それぞれに得意な用途やメリット・デメリットが存在します。導入を検討する際には、生産量、ワークの形状、設置スペース、予算などを考慮して、最適なタイプを選ぶことが重要です。
ここまで、超音波はんだ付けロボットの特徴や、種類を確認しましたが、実際に導入する際にはどのようなプロセスを経て、何に注意すべきなのでしょうか。次の章では、導入プロセスと注意点について解説します。
超音波はんだ付けロボットの導入プロセス・注意点を解説
超音波はんだ付けロボットの導入は、生産効率の向上や品質改善に貢献する可能性がありますが、導入を成功させるためには計画的なプロセスといくつかの注意点を理解しておくことが重要です。ここでは、導入の一般的な流れと、特に注意すべきポイントについて解説します。
導入検討から稼働までの流れ
超音波はんだ付けロボットの導入は、一般的に以下のステップで進められます。
まず、導入目的(生産性向上、品質向上、難材対応など)、対象ワーク(材質、形状、サイズ、生産量)、必要な自動化レベル、予算などを明確にします。また、現行工程の作業内容や課題を分析し、ロボット導入による工程の再設計や改善点も事前に検討します。
事業計画書の作各メーカーやシステムインテグレータ(SIer)の製品情報(ロボットの種類、仕様、実績、安全対策、周辺設備との連携など)を収集し、自社の要件に合った候補を比較検討します。導入する設備の詳細や業務効率化の効果を明確に記載します。
候補メーカーに実際のワークと材料を提供し、接合テストを依頼します。超音波はんだ付けでは、難接合材料やフラックスレス、特殊はんだも対象とします。接合強度や外観、作業時間を評価し、量産条件下での再現性や安定性も確認します。
テスト結果に基づき、ロボットの具体的な仕様(軸構成、超音波発振器の性能、必要なオプション機能、安全対策など)を、システムインテグレータやメーカーと協議しながら決定します。その上で、正式な見積もりを取得します。
仕様、価格、納期、保証、サポート体制などを確認し、契約・発注を行います。
メーカーにて装置が製作されます。完成後、メーカーの工場または自社で、仕様通りに動作するか、要求品質や安全性を満たしているかを確認する受け入れ検査を、現場作業者の立ち会いのもとで実施します。
自社工場に装置を搬入・設置し、メーカーのエンジニアと共に試運転と調整を行います。
担当者向けに、ロボットの操作方法、プログラミング、メンテナンスに関するトレーニングを受けます。あわせて、定期的な消耗部品の交換や清掃など、メンテナンス計画についても指導を受けます。
十分なテストと調整を経て、実際の生産ラインでの稼働を開始します。
超音波はんだ付けロボットの導入成功には、メーカー/SIerとの密接なコミュニケーションが重要です。超音波はんだ付けやロボットシステムは専門性が高く、要件定義から稼働後まで各段階での認識合わせや課題共有が欠かせません。
疑問点を伝え、提案に耳を傾ける双方向の連携が、トラブルを防ぎ期待通りの効果を得る鍵となります。
設置環境に関する注意点
超音波はんだ付けロボットを設置する際には、その性能を最大限に発揮させ、安全に運用するために、環境に対する配慮が必要です。
まず、安定した電源と、必要であれば適切な排気設備が必要であり、特に、はんだ付け時に発生するヒューム(煙)を適切に処理することは、作業者の健康と安全のために重要です。
また、ロボットの動作精度を維持するためには、過度な振動や温度変化の少ない環境が望まれます。特に精密な位置決めが求められる場合は、設置場所の床の強度や水平度にも注意が必要です。
インライン型や多関節ロボット搭載型の場合は、ロボットの可動範囲を考慮した十分なスペースと、安全柵やライトカーテンなどの安全対策設備の設置が法規で定められている場合もあります。
操作トレーニングとメンテナンス
超音波はんだ付けロボットは自動化装置ですが、その能力を引き出すためには、適切な操作とメンテナンスが重要です。
導入時には、メーカーが提供する操作トレーニングを必ず受講し、担当者が基本的な操作、ティーチング(動作プログラムの作成)、パラメータ設定、日常点検、簡単なトラブルシューティングを行えるようにする必要があります。特に、超音波のパラメータ設定は接合品質に直結するため、その意味と調整方法を理解することが重要です。
また、長期的に安定した性能を維持するためには、定期的なメンテナンスが欠かせません。はんだごてチップの清掃や交換、超音波ホーンの状態確認、ロボット駆動部の点検などを、メーカーの指示に従って実施する必要があります。消耗品の適切な管理も重要です。
安全性に関する注意点
ロボットを使用する上で、安全確保は最優先事項です。
超音波はんだごては高温になりますので、火傷に注意が必要です。また、ロボットの動作範囲内への立ち入りは、原則として禁止し、必要な場合は安全柵やセンサーで保護する必要があります。非常停止ボタンの位置と操作方法を作業者全員が把握しておくことも重要です。
超音波自体は、通常の使用レベルでは人体に直接的な害は少ないとされていますが、装置の仕様や作業環境によっては、聴覚保護具の使用が推奨される場合もあります。メーカーの安全指示に従い、適切な保護具を着用してください。
導入プロセスと注意点を理解し、計画的に準備を進めることで、超音波はんだ付けロボットは強力な生産ツールとなり得ます。
ここまで、超音波はんだ付けロボットの基本情報について詳しく見てきました。これらの知識を基に、次に重要となるのが「自社に最適なロボットをどう選ぶか」という点です。次の章では、具体的な選び方のポイントを解説していきます。
最適な機種の選定のために! 超音波はんだ付けロボットの選び方3つのポイント
超音波はんだ付けロボットの導入効果を最大化するためには、自社の用途や生産条件に最適な機種を選定することが極めて重要です。ここでは、選定時に特に注目すべき3つのポイントを解説します。
超音波周波数・出力の調整機能で接合品質を確保する
超音波はんだ付けロボットを選定する上で重要なポイントのひとつは、接合対象(使用する金属や基板の材質、接合面積など)に応じて、超音波の周波数や出力を適切に調整できる機能を確認することです。
その理由は、母材の特性(硬さ、熱伝導率など)や接合部の大きさによって、最適な超音波の振動条件が異なるからです。もし周波数や出力の設定が不適切だと、はんだの濡れ不足といった接合不良や、逆に過剰なエネルギーによる基板・部品へのダメージ(クラック等)といったリスクが生じます。
特に、ガラスやセラミックスのような脆性材料、あるいは微細な電子部品を扱う場合には、精密な調整機能が不可欠となります。また、多品種のワークに対応する必要がある場合にも、幅広い調整能力が求められます。
適切な周波数・出力調整機能を持つロボットを選ぶことで、様々な材質の組み合わせに対しても安定した高品質な接合を実現でき、結果として歩留まりや生産性の向上に繋がる、最適なはんだ付けプロセスの構築が可能になります。
チップ形状とロボット軸構成で複雑なワークに対応する
超音波はんだ付けロボットを選定する際には、接合したい部位のサイズや形状に対応できる最適な超音波チップ(こて先)の形状と、それを正確にアプローチさせるためのロボットの軸構成(自由度)を選定することが重要です。
これは、超音波チップの先端形状やロボットの可動範囲が、複雑な三次元形状を持つワークや、密集した微細部品への正確なはんだ付け品質に直接影響を与えるためです。
不適切なチップ形状を使用すると、特定の箇所に過度な圧力や熱が集中してしまったり、はんだが必要な箇所に均一に供給されなかったりするリスクが生じます。また、ロボットの自由度が足りないと、ワークの隅や奥まった箇所へチップを到達させられない可能性もあります。
特に、電子基板上の狭いスペースへの部品実装や、自動車部品のような曲面部へのはんだ付けが多い製品を取り扱うときには、チップ形状とロボットの動作自由度の最適化が不可欠となります。
接合部の形状に合わせた多様なチップ形状を選択でき、かつワークに対して適切な角度や位置でアプローチできるロボットを選ぶことで、微細な部分やアクセスしにくい箇所でも均一で信頼性の高い接合が可能となり、これまで自動化が難しかった特殊なワークへの対応も容易になります。
リアルタイム制御機能で安定性と安全性を両立する
超音波はんだ付けロボットを選ぶ際の重要な検討事項として、はんだ付け中の温度や超音波振動の状態をリアルタイムに監視し、制御できるフィードバック機能の有無を確認することが挙げられます。
その理由は、はんだ付けのプロセス中には、こて先の温度変化、はんだ材の状態、ワークへの熱の伝わり方など、接合条件が刻々と変化するため、それに応じて超音波エネルギーを適正にコントロールする必要があるからです。
もし、このようなリアルタイム制御が不十分だと、母材に対して過剰な振動負荷を与えてダメージを生じさせたり、溶融はんだが飛散するスパッタ現象が発生しやすくなったりして、製品の歩留まり低下や作業環境の安全性低下を招く可能性があります。
特に、要求される品質レベルが高い製品や、生産する品種が頻繁に変わる多品種少量生産ラインにおいては、様々な条件変化に迅速に対応し、常に安定した接合を実現する能力が必須となります。
温度や振動を動的に調整できる高度なフィードバック制御機能を備えたロボットを導入することで、接合強度や品質を高めながら、同時にワークへのダメージやスパッタの発生を最小限に抑えることが可能になるでしょう。
これらの選び方のポイントを踏まえ、自社のニーズに合致したロボットを選定することが、導入成功への鍵となります。単にスペックだけでなく、メーカーのサポート体制や実績も考慮に入れると良いでしょう。
では、具体的にどのようなメーカーが超音波はんだ付けロボットを提供しているのでしょうか。次の章では、おすすめのメーカーとその製品の特徴をご紹介します。
超音波はんだ付けロボットのおすすめメーカー
JET-Globalでは、超音波はんだ付けロボットを活用した超音波はんだ付け工程の自動化支援も行っております。
ロボットの導入成功まで専門家がサポートいたします。相談は無料ですので、ぜひ以下よりサービス詳細をご覧ください。
超音波はんだ付けロボットは、専門性の高い技術力が求められるため、信頼できるメーカー選びが重要です。ここでは、国内外で実績のある代表的なメーカーをピックアップし、それぞれの特徴や強みを紹介します。
※クリックで各メーカーの詳細に飛べます。
ジャパンユニックス / JAPAN UNIX
会社名 | ジャパンユニックス / JAPAN UNIX |
設立年 | 1974年 |
本社 | 東京都港区赤坂2-21-25 |
概要 | はんだ付けロボットおよび周辺機器の設計・製造・販売を行うメーカー |
ジャパンユニックスは、お客様のはんだ付けに関する課題に一緒に取り組み、安定した量産体制の構築を目指す、はんだ付け総合ソリューションメーカーです。多様な業界・用途に対応する豊富な製品ラインナップと、顧客の個別ニーズに合わせたカスタマイズ対応力が強みです。
同社の超音波はんだ付け関連製品としては「UNISONIK」シリーズなどが挙げられます。長年にわたる自動はんだ付け技術の蓄積に裏打ちされた高い再現性と品質安定性が、ジャパンユニックスの超音波はんだ付けロボットの強みです。トレーサビリティへの対応など、生産現場で求められる信頼性にも配慮されています。
その高い技術力と信頼性から、自動車・車載部品、医療機器、産業機器、電子部品、EMS(電子機器受託生産)、さらには航空・宇宙分野といった、要求品質の厳しい国内外の多様な業界で豊富な導入実績を誇ります。
コムラテック / KOMURA-TECH
会社名 | コムラテック / KOMURA-TECH |
設立年 | 1980年 |
本社 | 大阪府東大阪市中石切町6-2-67 |
概要 | 超音波はんだ付け装置の開発・設計・製造・販売を行う |
コムラテックは、Cerasolza(セラソルザ)/ SUNBONDER(サンボンダ)に代表される超音波はんだ付け技術・材料・装置をワンストップで提供するメーカーです。
同社の超音波はんだ付け関連製品としては「SUNBONDER(サンボンダ)」などが挙げられます。ガラスやセラミックス等、従来困難だった材質へのフラックスレス接合に対応しています。さらに、ロングスパンの自動はんだ直接線引き装置など自動化設備も自社設計可能です。
薄膜太陽電池・有機EL・調光ガラス領域での量産運用実績が明示されています。
超音波はんだ付けロボットのカタログ
超音波はんだ付けロボット関連記事
超音波はんだ付けロボット関連記事はまだありません。