溶接ロボット
溶接ロボットは、生産性向上や品質の均一化、労働環境の改善を可能にする製造現場の強力なパートナーです。世界の自動化の潮流も相まって、溶接ロボットはますます現場へ導入されています。
この記事では、スポット溶接やアーク溶接など6種類の溶接ロボットの特徴と適用場面を詳しく解説します。さらに、溶接ロボット選びに欠かせない比較ポイントやおすすめメーカーについても取り上げます。
溶接の自動化に最適な溶接ロボットを選ぶための実践的な情報を提供しますので、ぜひご一読ください。
また、JET-Globalでは実際に、溶接ロボットの導入支援も行っております。
ロボットの専門家による製品の選定から補助金の活用、ロボット研修による社内人材の育成まで、溶接ロボット導入をあらゆる面からサポートいたします。
「一度ロボットを触ってみたい」や「こんな自動化ができるか知りたい」などの軽い相談も可能です。
相談は無料ですので、関心のある方は以下のサービス詳細をご覧ください。
溶接ロボットとは? 種類とそれぞれの特徴
溶接ロボットは、自動化された溶接作業を実行するための産業用ロボットです。このロボットを導入することで、工場における溶接作業の生産性の向上、品質の安定化、作業環境の改善を効果として期待できます。
溶接ロボットには、以下の3種類が基本的な分類として挙げられます。
- アーク溶接ロボット
- スポット溶接ロボット
- レーザー溶接ロボット
- シーム溶接ロボット
※クリックすると該当箇所まで飛びます
アーク溶接ロボット
アーク溶接ロボットは、高電圧を電極棒にかけて発生するアーク放電の熱を利用して金属を溶接するロボットです。アーク放電にはガスの利用が必要となり、ガスの種類によって、TIG溶接ロボット、MIG溶接ロボット、MAG溶接ロボット、プラズマアーク溶接ロボットなどに分けることもできます。建設機械や鉄骨フレームなどの溶接に広く使われており、小型ながらも溶接部分を水平に保つための周辺設備が必要な場合があります。
このロボットの強みには、以下の点が挙げられます。
- 省スペースでありながら剛性が高く、高速動作が連続しても手振れがなく、位置決めが正確
- 可搬重量は10~20キログラム程度と軽めで、手首部分が中空構造になっていることが多く、ワイヤーやガスの供給チューブの取り回しが容易
- アームの長さは可搬重量の割に長めで、中小~大企業まで幅広く使用
- 軌跡精度が重要視されるため、連続的に線で溶接を行う際に優れた性能を発揮
アーク溶接ロボットは、高温での作業が可能で、金属のヒュームを発生させる作業に適しています。そのため、品質が安定し、溶接スピードが速いというメリットがあります。ほかの溶接方法と比較して、アーク溶接は金属同士の接続に用いられ、接着面を広くすることができるため、大型機械にも活用されることが多いです。
TIG、MIG、MAGなど、アーク溶接ロボットについては、次の記事で詳しく解説しています。アーク溶接ロボットの導入を検討される場合はぜひご一読ください。
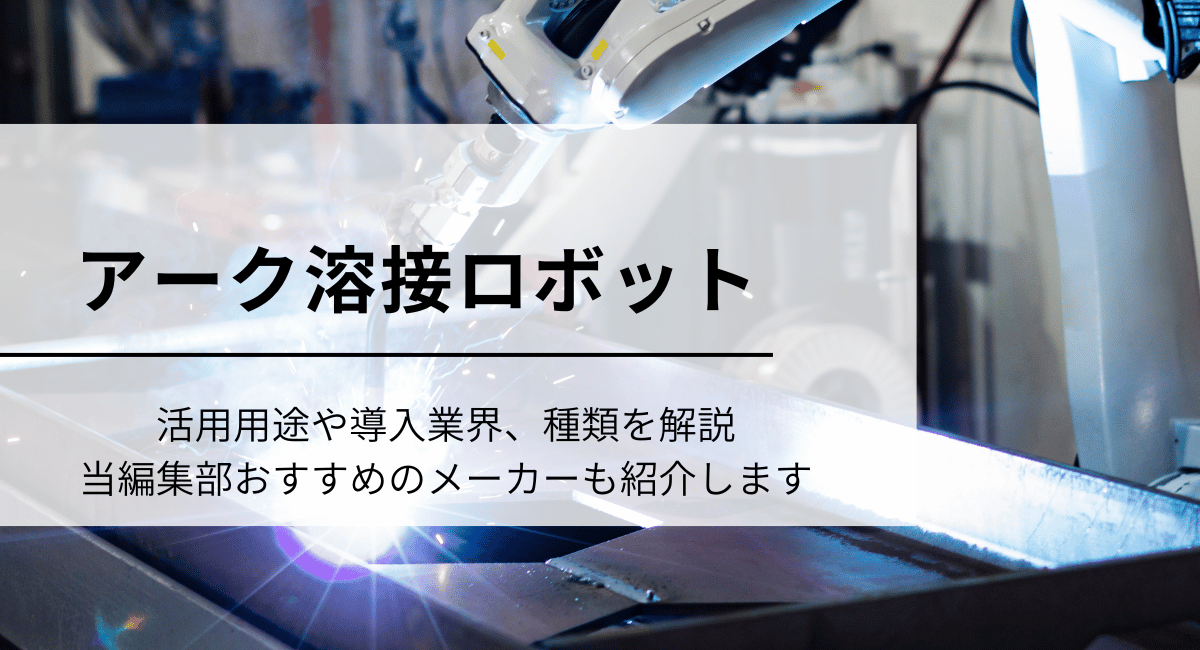
スポット溶接ロボット
スポット溶接ロボットは、主に自動車産業で使用されるロボットで、複数の金属シートを点で溶接できます。高出力・高性能モーターの採用や最新の防振制御により、サイクルタイムを短縮し、生産ラインの効率化を実現しています。
このロボットの強みには、以下の点が挙げられます。
- 軽量化と高性能モータの採用により、迅速な作業が可能
- コンパクトな設計により、生産ラインを短縮化できる
- プログラム通りの動きをするため、溶接の品質を一定に保てる
スポット溶接は速度が速く、時間短縮が可能です。また、スポット溶接ロボットは可搬重量が大きく、重い溶接ガンに対応しています。
スポット溶接ロボットには、ACタイプやDCタイプなど、いくつか種類も存在しています。詳しくは、以下の記事をご覧ください。
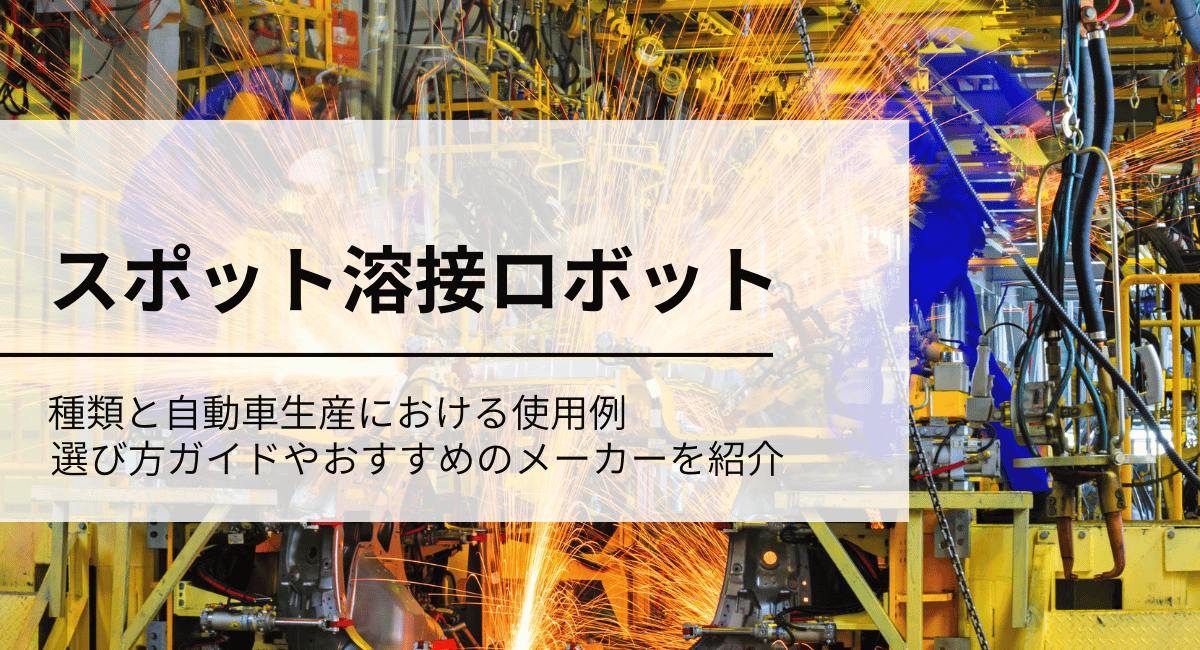
レーザー溶接ロボット
レーザー溶接ロボットは、高精度なレーザー光線を利用して金属などの材料を溶接するロボットです。これらは特に、複雑な形状や繊細な溶接が必要な場合に有効で、自動化された精密作業を可能にします。このロボットの強みには、以下の点が挙げられます。
- 複雑な形状や小さな部品の溶接に適している
- 手動溶接よりも速く、生産性を大幅に向上させることができる
- ロボットによる自動化は、人的ミスを減らし、一貫した品質を提供できる
- 危険な溶接作業をロボットが行うことで、作業員の安全が確保できる
レーザー溶接ロボットは、特に精密な溶接が求められる場合や、高速での生産が必要な場合に選ばれます。YAGレーザーやCO2レーザーなど、レーザー溶接ロボットにはいくつか種類があります。関心のある方は、詳しくは次の記事をご参照ください。
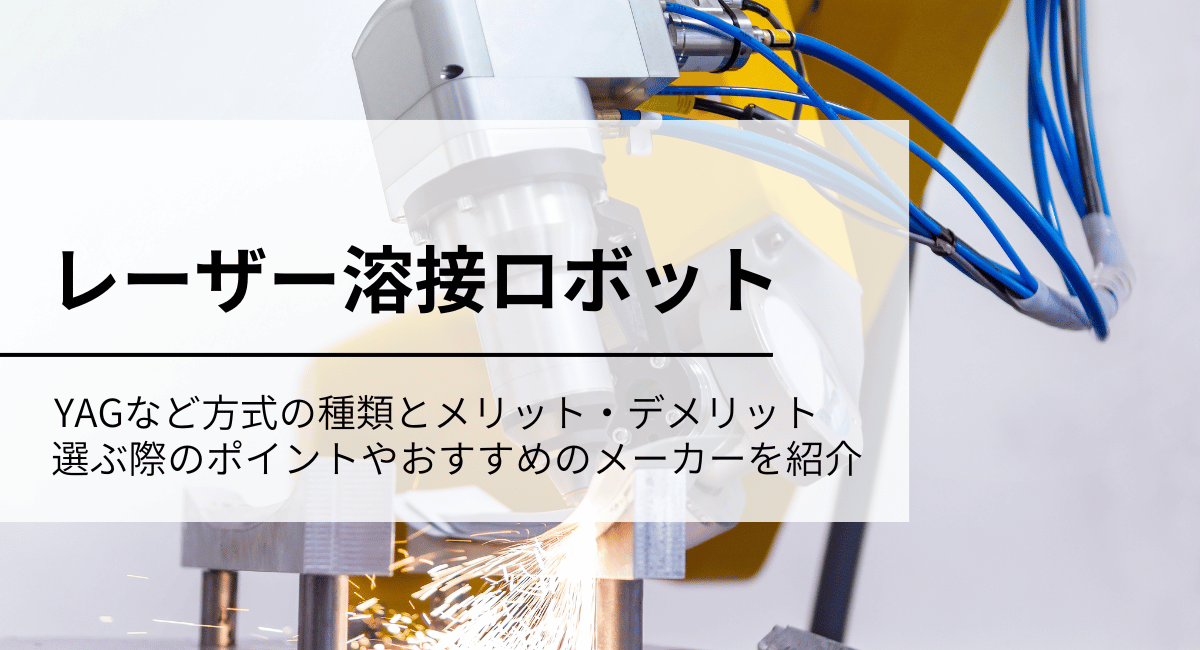
シーム溶接ロボット
シーム溶接ロボットは、母材の境界を連続してたどりながら、抵抗熱を利用して自動的に溶接ビードを形成する産業用ロボットのひとつです。手作業の連続溶接では品質の均一化が難しい一方、ロボット化されたシーム溶接は速度と押圧を一定に保つことで、高い精度と安定した接合強度を長時間維持できる点が大きな強みです。
以下に、シーム溶接ロボット導入時の利点をまとめます。
- 長いワークにも途切れのない高精度溶接が行える
- 工程ごとの品質ムラを抑え、安定した仕上がりを実現
- 既存ラインへの組み込みが比較的容易で、量産体制に適合
シーム溶接ロボットについて、さらにくわしく知りたい方はぜひ次の記事をご一読ください。
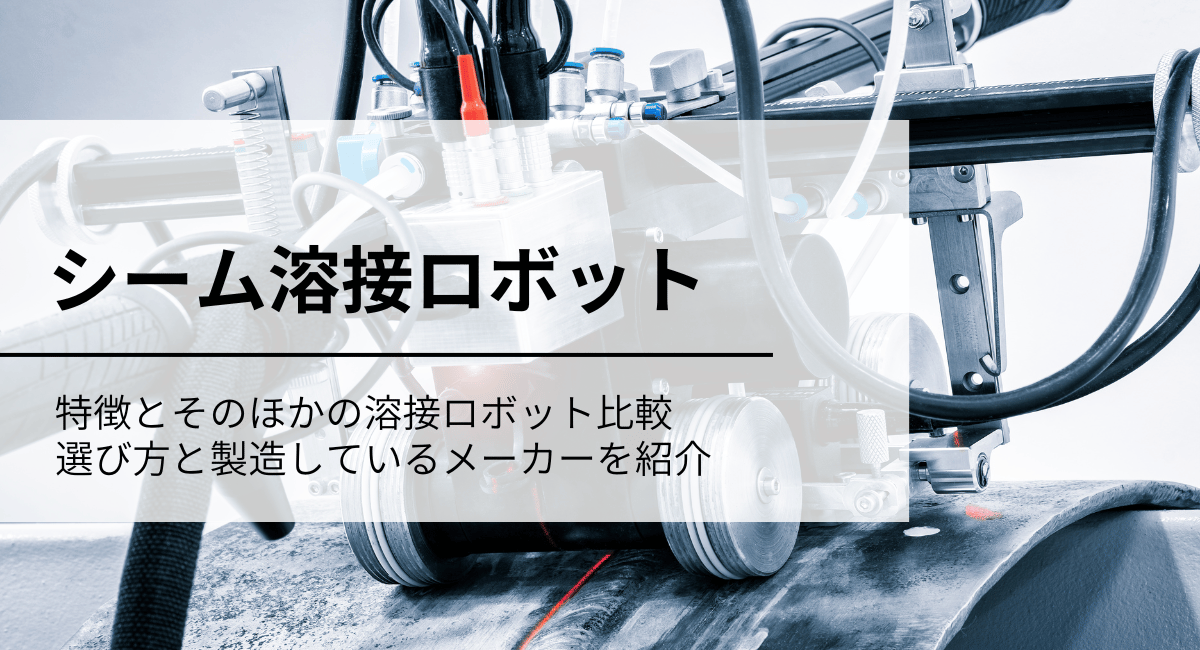
溶接ロボットを活用するメリット・デメリット
溶接ロボットを導入する際は、メリットだけではなくデメリットも考慮して検討する必要があります。このセクションでは、メリットとデメリットをそれぞれご紹介します。
メリット
溶接ロボットには、主に以下のようなメリットが挙げられます。
生産性の向上
溶接ロボットを導入することで、生産性の向上が大きなメリットとして挙げられます。これは、溶接ロボットが人間の溶接作業と比較して、一定の品質で高速に溶接作業を行うことができるためです。また、24時間の連続稼働が可能であり、人手不足の解消や作業者の労働負荷軽減にも寄与します。
このため、溶接ロボットは以下のような場面で活用されることが多いです。
- 自動車製造業
- 重工業
車体や部品の溶接で、複雑な箇所の溶接でも一貫して高品質かつ高速な溶接を実現
造船や鉄道車両の製造など、連続稼働が求められる大規模な溶接作業を効率的に進められる
品質の均一性
溶接ロボットを活用することにより、品質の均一性が大きなメリットとして挙げられます。これは、溶接ロボットがプログラムされた通りに正確に作業を行うため、すべての溶接箇所において一定の品質を維持できるからです。人間の手による作業ではどうしても個人差や疲労による品質のばらつきが発生しますが、溶接ロボットはこれを克服し、製品の品質を一定に保つことができます。
このため、溶接ロボットは以下のような場面で活用されることが多いです。
- 航空宇宙産業
- 医療機器製造業
航空機の部品や構造物の製造において、品質の均一性が非常に重要
医療機器の製造においても、品質の均一性は極めて重要
労働環境の改善
溶接ロボットを活用することにより、労働環境の改善が大きなメリットとして挙げられます。溶接作業は高温や有害な煙、紫外線など、労働者にとって過酷な環境下で行われることが多く、健康リスクが高いです。溶接ロボットを導入することで、こうした有害環境での作業を人間に代わって行い、作業者の安全性と健康を守ることができます。
また、重労働からの解放により、作業者の負担軽減や職場の快適性向上にも寄与します。このため、溶接ロボットは以下のような場面で活用されることが多いです。
- 建設業
- 金属加工業
有害環境での作業を人間に代わって行い、作業者の安全性と健康を守る
一貫して高精度な溶接を行うことができるため、製品品質の向上と同時に作業者のストレスも軽減
デメリット
一方で、溶接ロボットには以下の弱みや課題もあるため、それぞれの解消法を含めて確認、検討する必要があります。
- 初期投資の大きさ
- プログラミングの必要性
- メンテナンスの手間がかかる
※クリックすると該当箇所まで飛びます
初期投資の大きさ
溶接ロボットの導入には高額な初期投資が必要となります。これにはロボット本体の価格、周辺機器、設置費用、プログラミングや調整のための費用が含まれます。また、技術者の教育やメンテナンスのコストも発生します。これらの初期投資が大きなハードルとなり、中小企業や予算に制約がある企業にとっては導入をためらう要因となります。
コストを抑えて溶接ロボットを導入するには、溶接ロボットの購入ではなく、リースやレンタルの選択肢を活用することで、初期投資の負担を軽減することがおすすめです。これらの場合、毎月の支払いが固定されるため、キャッシュフローの管理が容易になります。また、リース期間終了後には最新のロボットに更新することも可能で、常に最新の技術を利用できる利点もあります。
また、政府や自治体が提供する補助金や助成金を活用することも、初期投資の負担軽減に有効です。
これらの制度を利用することで、溶接ロボット導入の際のコストを一部補助してもらうことができ、初期投資の負担を大幅に軽減することができます。事前に情報収集を行い、適切な制度を活用することで、導入コストを抑えることが可能です。
プログラミングの必要性
溶接ロボットの導入には、適切なプログラミングが必要です。これには、ロボットの動作を正確に設定し、各製品や作業内容に合わせたプログラムを作成する作業が含まれます。プログラミングは高度な技術を必要とし、専門知識を持った技術者の確保や教育が不可欠です。このため、プログラミングの難易度やコストが溶接ロボットの導入の障害となることがあります。
プログラミングの負担を軽減するには、より直感的なプログラミングインタフェースをもつロボットを選ぶことが有効です。
例えば、タブレットやスマートフォンを使った簡単なドラッグアンドドロップ操作や、ビジュアルプログラミングを採用することで、プログラミングのハードルを下げることができます。これにより、専門知識がなくても基本的なプログラミングが可能となり、初期導入時の負担が軽減されます。
また、オフラインプログラミングソフトを使用することで、ロボットを稼働させながらプログラムの開発や調整が可能になります。
これにより、現場での稼働時間を削減しつつ、効率的にプログラミング作業を行うことができます。オフラインプログラミングソフトは、シミュレーション機能を備えていることが多く、実際の動作を事前に確認し、エラーを最小限に抑えることができます。これにより、現場での調整時間が短縮され、生産性の向上が期待できます。
メンテナンスの手間がかかる
溶接ロボットを活用する上で、定期的なメンテナンスが必要です。メンテナンスには、ロボットの各部品の点検・交換、ソフトウェアのアップデート、溶接機器の調整などが含まれます。これにより、メンテナンスの手間とコストがかかり、ダウンタイムが発生する可能性があります。メンテナンスが不十分な場合、ロボットの故障や製品品質の低下につながるリスクもあります。
このデメリットを軽減するには、予防保全プログラムを導入が有効です。
定期的かつ計画的なメンテナンスを行い、予期せぬ故障を未然に防ぐことができます。これには、メーカーが提供するメンテナンススケジュールに従い、必要な部品交換や点検を行うことが含まれます。また、定期的な診断やモニタリングを行い、異常を早期に検知することで、重大な故障を防ぐことができます。予防保全プログラムにより、メンテナンスの計画性が向上し、ダウンタイムの最小化と長期的なコスト削減が期待できます。
4つの比較ポイント|溶接ロボットの選び方
溶接ロボットを選ぶ際は、以下の4つの基準を確認することがおすすめです。
動作速度
動作速度が変わると、母材への入熱量と溶着金属量が変動し、溶接スピードと品質が変化します。速度が速いと入熱量が減少し、遅いと入熱量が増加するため、溶接品質に直接影響を与える可能性がある。
動作速度が速い場合のメリットには、以下のポイントが挙げられます。
- サイクルタイムが短縮され、より多くの部品を短時間で溶接可能
- 入熱量が減少するため、熱影響ゾーンが小さくなり、材料の熱変形が減る
一方で、動作速度が遅いと、以下のようなメリットがあります。
- 溶接品質が安定する
- 溶接ビードの形成が良好になることが多い
- 複雑な形状や狭い箇所でも精密な溶接が可能
可動範囲
可動範囲は、ロボットがどれだけの範囲で動作できるかを示す重要な指標です。この範囲が変動すると、ロボットの適用可能な作業やその柔軟性に大きな影響を与えます。
可動範囲が広い場合のメリットには、以下のポイントが挙げられます。
- 多様な作業に対応できるため、ひとつのロボットで複数のタスクをこなすことが可能
- 複雑な形状のワークにも対応でき、より高度な溶接作業を実行可能
- 設置スペースの制約が少なく、省スペースでの運用が可能
一方で、可動範囲が狭い場合のメリットには、以下のようなものがあります。
- コンパクトな設計が可能になり、コスト削減につながる
- シンプルな構造であるため、メンテナンスが容易
溶接精度
溶接精度が変動すると、溶接位置の正確性が変わります。これは、製品の強度や寸法精度に直接関わるため、最終製品の品質に大きく影響します。精度が高ければ、より信頼性の高い製品を作ることができます。
溶接精度が高い場合のメリットには、以下のポイントが挙げられます。
- 溶接位置が正確になり、製品の品質が向上
- 再作業や修正が少なくなり、生産性が向上
- 溶接による熱歪みや変形を検出し、正しい位置に補正する自動制御が可能
一方で、溶接精度が低い場合のメリットには、以下のようなものがあります。
- 設備投資やメンテナンスコストが抑えられる
- 複雑なセンサーや制御システムが不要になるため、運用がシンプル
溶接電流
溶接ロボットにおける溶接電流の変動は、溶接の品質と効率に大きな影響を与えます。電流が増加すると溶接の浸透深さが深くなり、逆に電流が減少すると浸透深さが浅くなります。電流の増減によってビードの幅や高さが変化し、溶接の外観に影響します。電流が高いと熱入力が多くなり、材料の熱影響区域が広がります。
溶接電流が高い場合のメリットには、以下のポイントが挙げられます。
- 溶接速度を上げることができ、生産性が向上
- 厚い材料の溶接に適している
一方で、溶接電流が低いと、以下のようなメリットがあります。
- 熱入力が少なくなり、薄い材料の溶接に適している
- 熱影響区域が小さくなるため、材料の歪みを抑えることができる
溶接ロボットを製造するメーカー・代理店
溶接ロボットのメーカー
溶接ロボットを製造する主なメーカーには、以下の5社が挙げられます。
JET-Globalでは、溶接ロボットを活用した溶接工程の自動化支援も行っております。
ロボットの導入成功まで専門家がサポートいたします。相談は無料ですので、ぜひ以下よりサービス詳細をご覧ください。
川崎重工業/Kawasaki Heavy Industries
会社名 | 川崎重工業/Kawasaki Heavy Industries |
設立年 | 1896年 |
本拠地 | 東京都港区 |
概要 | 船舶からロボットまで、多岐にわたる事業を展開する |
川崎重工業は、アーク溶接ロボットを中心に、広範な業界で薄板から厚板までの多くの実績を持つメーカーです。ロボットと溶接機をケーブル1本で接続できるシンプルな設計が特徴で、アーク溶接の品質向上をサポートするオプションを豊富に取り揃えています。
同社は、アーク溶接ロボットを主に製造しています。
神戸製鋼所/Kobe Steel
会社名 | 神戸製鋼所/Kobe Steel |
設立年 | 1905年 |
本拠地 | 兵庫県神戸市中央区 |
概要 | 素材や機械、エンジニアリングなど、多角的な事業を展開する |
神戸製鋼所は、素材、機械、電力事業を展開している総合メーカーで、溶接ロボットも手掛けています。長年にわたる溶接施工とシステム構築のノウハウを基に、最新システムを駆使して顧客の溶接ソリューションを実現しています。
同社は、スポット溶接ロボットとアーク溶接ロボットを主に製造しています。
パナソニックコネクト/Panasonic Connect
会社名 | パナソニックコネクト/Panasonic Connect |
設立年 | 2022年 |
本拠地 | 東京都中央区 |
概要 | 映像機器システムから音響機器、溶接ロボットまで、多種多様な製品を製造する |
パナソニックコネクトは、ビジネス現場を有機的につなぎあわせる総合メーカーで、溶接ロボットを含む多様な熱加工プロセスを提供しています。特に、近赤外ダイレクトダイオードレーザ(DDL)を搭載したリモートレーザ溶接/切断ロボットがあり、高いレベルで「波長選択」「高出力化」「高ビーム品質」を実現しています。
同社は、アーク溶接ロボットとレーザー溶接ロボットを主に製造しています。
ファナック/FANUC
会社名 | ファナック/FANUC |
設立年 | 1972年 |
本拠地 | 山梨県南都留郡 |
概要 | FA機器やロボット事業を展開する |
ファナックは、産業用ロボットのメーカーであり、自動化促進に欠かせないシステムインテグレータの紹介も行っています。特に、溶接ロボットの分野で高い技術力を持ち、多様なニーズに応える製品を提供しています。
同社は、アーク溶接ロボットとスポット溶接ロボットを主に製造しています。
不二越/NACHI-FUJIKOSHI
会社名 | 不二越/NACHI-FUJIKOSHI |
設立年 | 1928年 |
本拠地 | 富山県富山市 |
概要 | 油圧機器や産業用ロボットなどを製造・販売する |
不二越は、スポット溶接やシーム溶接など、多様な溶接ロボットを製造している企業です。高速で精密な作業が可能なロボットを提供し、ものづくりの世界の発展に貢献しています。
同社は、スポット溶接ロボット、レーザー溶接ロボットを主に製造しています。
溶接ロボットの代理店
冨士山/Fujiyama
会社名 | 冨士山/Fujiyama |
設立年 | 1961年 |
本拠地 | 神奈川県相模原市 |
概要 | 高圧ガスの供給および溶接機・溶接材料の販売を行う |
冨士山は、1961年に設立された高圧ガス供給が主な事業の会社です。高圧ガスのほかに、溶接機、産業用機械などの代理店事業も行っています。
ガス供給会社が溶接ロボットの代理店もしているのは不思議に思えるかもしれませんが、溶接ロボットを動かすにはガスが必要です。
それゆえ、溶接ロボットの購入だけでなく、実際に動かすまでをまとめてお任せできるところが冨士山の特徴です。
溶接ロボット関連記事
溶接ロボット関連記事はまだありません。