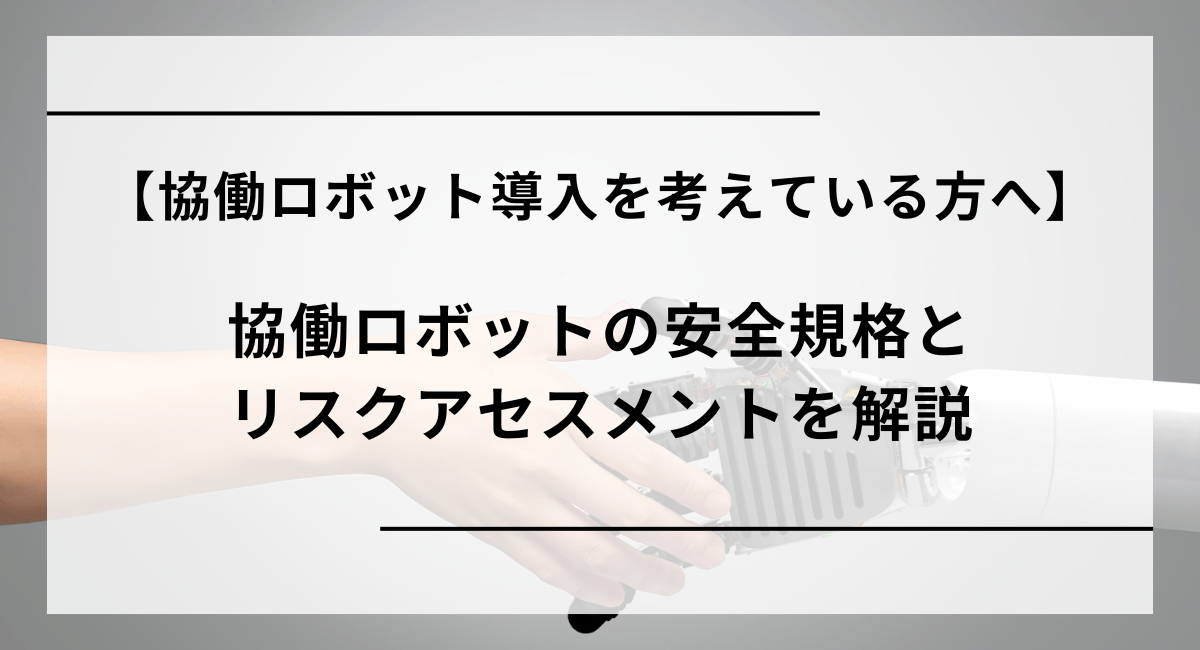
協働ロボットの安全規格とリスクアセスメントを解説!
近年、人手不足の解消や生産性の向上、変種変量生産への柔軟な対応などを目的に、製造現場をはじめとする様々な分野で「協働ロボット」の導入が進んでいます。従来の産業用ロボットと異なり、人の近くで作業できることが大きな特徴ですが、その利便性の裏には、確実な安全確保が必要です。安全規格に基づく、リスクアセスメントなしに協働ロボットを導入・運用すると、人とロボットの接触・衝突による重大な人身事故や、関連法規違反による罰則・操業停止などのリスクが生じます。
本記事では、協働ロボットを安全に導入・運用するために知っておくべき「安全規格」と、多くの国や業界で義務化または強く推奨されている「リスクアセスメント」の基本情報や方法、事例を分かりやすく解説します。
協働ロボットの導入を検討しており、安全規格に不安を感じている方へ。本記事が、その不安を解消する助けになる可能性がありますので、ぜひご一読ください。 また、JET-Globalでは実際に、協働ロボットの導入支援も行っております。
協働ロボットの導入を考えているが、安全規格やリスクアセスメントについて不安がある方はこちらからお気軽にご相談ください。
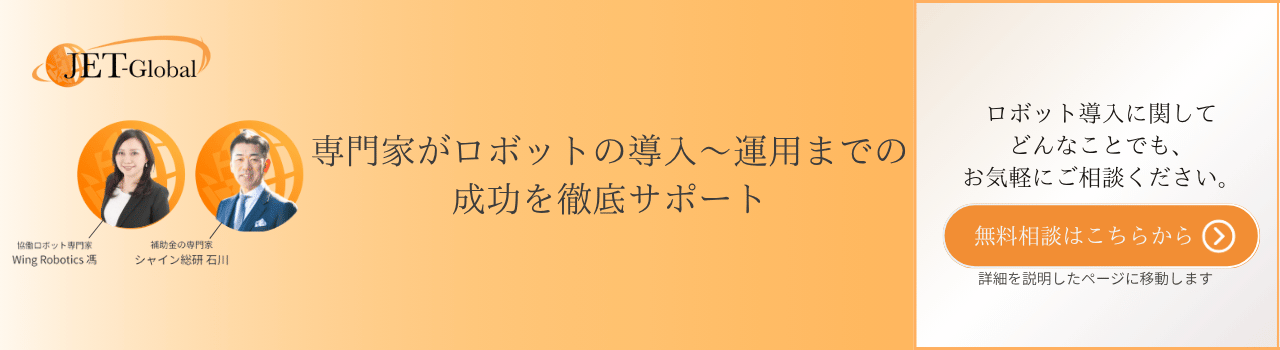
協働ロボットの安全規格とは?
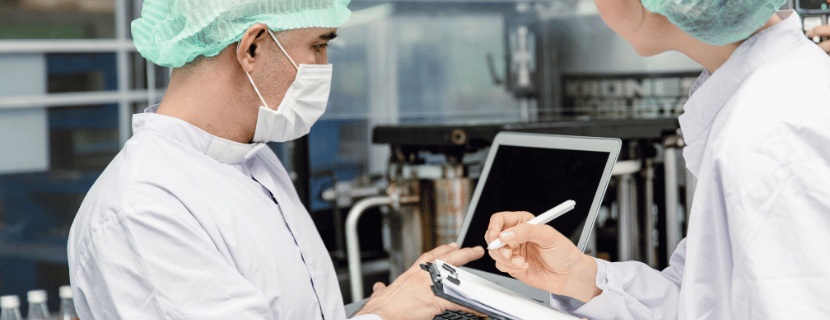
協働ロボットの安全規格とは、協働ロボットを安全に使用するための基本的なルールブックと言えます。
協働ロボットの安全性を確保するためには、国際的に定められた安全規格への準拠が基本となり、これは、設計・製造からシステム構築、運用に至るまで、安全に関する要求事項を定めたものです。
そもそも、協働ロボットがどのようなロボットを指しているのか、疑問に思う方は以下の記事をご参考ください。
関連記事
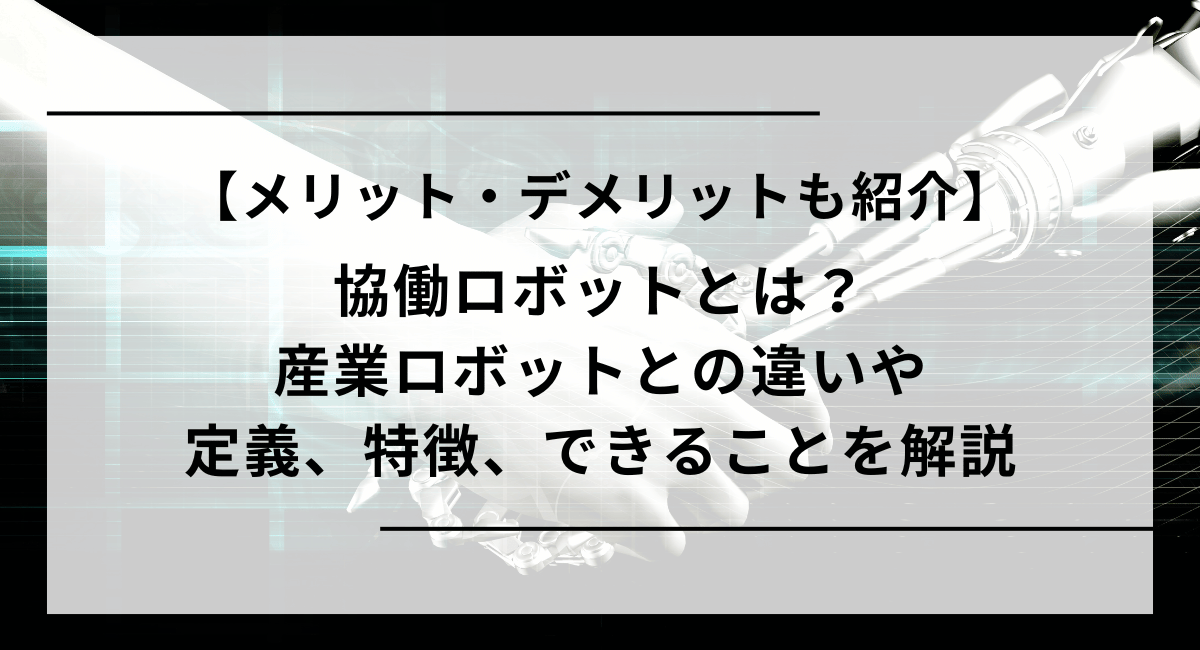
協働ロボットとは?産業ロボットとの違いや定義、特徴、できることを解説
それでは、以下から協働ロボットに関わる安全規格を確認しましょう。
ISO 10218-1:ロボット本体の安全要求事項
ISO 10218-1は、ロボットメーカーが、協働ロボットを含むすべての産業用ロボットの単体(マニピュレータとコントローラ)を安全に設計・製造するための基本的な安全要求事項を規定した国際規格です。この規格には、非常停止機能、動作範囲の制限、安全な制御システムの設計といった基本的な安全要求に加え、後の協働運転を実現するためにロボット自体が備えるべき基本的な安全機能(例:安全な停止状態を監視する機能、動力・力を制限する機能の基礎要件など)も含まれています。
ISO 10218-2:ロボットシステムの統合に関する安全要求事項
ISO 10218-2は、ロボットを使う側(工場など)が、そのロボットを使って安全なシステム(安全柵、センサー、他の機械との連携などを含む)を構築し、運用するためのルールです。ロボットシステム(ロボット、エンドエフェクタ、周辺機器等)のインテグレーション、設置、保護措置、情報、運用に関する安全要求事項を規定しています。
協働ロボットのシステム構築においても、この規格が基本となります。この規格の中で、協働運転の4つの形態(安全適合監視停止、ハンドガイディング、速度・間隔監視、電力・力制限)が定義されています。
ISO/TS 15066:協働ロボット固有の技術仕様
ISO/TS 15066は、上記のISO 10218を補完する技術仕様書(Technical Specification)であり、特に人とロボットが作業空間を共有する「協働運転」に関する安全要求事項を詳細に規定しています。ISO/TS 15066が定義する4つの協働運転モード
ISO/TS 15066は、人とロボットが安全に同じ空間で作業を行う「協働運転」を、適切な速度や力の管理を通じて実現するために、リスクアセスメントの結果とアプリケーションの要求に応じて選択・適用できる、主に以下の4つのモードを定義しています。-
安全適合監視停止
人がロボットの作業スペース(協働スペース)に進入すると、ロボットは動作を停止し、その停止状態が安全に監視されます。人がスペースから退出すると、ロボットは(設定された速度で)自動的に作業を再開できます。人とロボットが「同時」には作業しないが、作業スペースを共有するような状況に適しています。 -
ハンドガイド
作業者が必要な時だけ、ロボットのアームやツールに取り付けられたガイド装置を直接持って、ロボットを目的の位置へ誘導したり、動作を教示したりするモードです。操作中は、ロボットは安全に制御された速度(通常は非常に低速)と力で動作します。 -
速度と分離の監視(SSM)
安全センサー(レーザースキャナーやビジョンセンサーなど)を用いて、人とロボットの位置と距離を常に監視します。人とロボットの距離が縮まると、ロボットの速度を(予め設定された速度プロファイルに従い)段階的に落とし、設定された安全距離を下回る前に停止させることで、物理的な接触を回避します。速度の制御が鍵となるモードです。 -
電力及び力の制限(PFL)
ロボットの設計(丸みを帯びた形状、衝撃吸収材など)や制御(接触時の力を抑えるための適切な速度制限やトルク制限)によって、万が一、ロボットが人に接触した場合でも、その接触力や圧力が(速度などの要因も考慮して)人体に危害を与えない安全なレベルに制限されるようにするモードです。人とロボットが近接して作業する必要があり、低速での運用が基本となります。
これらのモードは、それぞれ独立して使用されることもありますが、作業のフェーズや状況に応じて組み合わせたり、切り替えたりすることも可能です。どのモード(またはモードの組み合わせ)を選択し、どのように設定するか(適切な速度設定を含む)は、後述するリスクアセスメントに基づいて慎重に決定される必要があります。
ISO 12100:リスクアセスメントの基本原則
協働ロボット固有の安全要求は上記のISO 10218やISO/TS 15066に定められています。これらの規格を適用し、安全なシステムを構築するための「リスクアセスメントの具体的な進め方」や「リスク低減策の考え方の基本」を提供しているのがISO 12100です。
特に人と近接して作業する協働ロボットでは、ISO 12100に基づいた網羅的かつ体系的なリスクアセスメントと、適切なリスク低減策(協働ロボット特有の技術を含む)の選択・実施が、安全確保のために不可欠となります。
日本では、労働安全衛生法第150条の4に基づき、協働ロボット導入時のリスクアセスメントが「努力義務」とされており、法的義務ではありませんが、ISO 10218やJIS B 8433(国内整合規格)に準拠した安全措置が強く推奨されます。
また、ISO/TS 15066は技術仕様書(TS)であり、国際規格(IS)ではないため、日本では業界ガイドラインとして扱われますが、電力・力制限(PFL)の閾値設計など実務上必須です。
本章では、協働ロボットに関する「安全規格」にはどのような種類があるのかを解説しました。次の章では、協働ロボット導入時に、これらの「安全規格」をもとに行う必要があるリスクアセスメントを解説します。
協働ロボット導入時のリスクアセスメントとは?
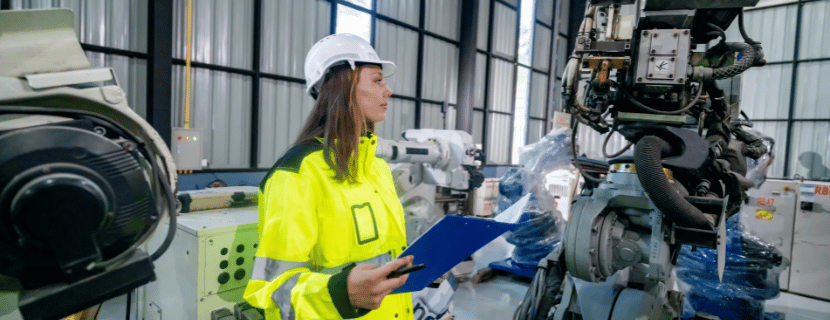
リスクアセスメントとは、簡単に言えば「どこに」「どのような危険が」「どのくらいの確率と重大さで」存在するのかを明らかにし、「その危険をなくしたり、小さくしたりするためにはどうすればよいか」を考え、実行していく活動です。
安全規格は汎用的な要求事項を定めたものですが、実際の作業環境や用途は千差万別です。 そのため、個々の協働ロボットシステムに対して、潜在的な危険源を特定し、それによって生じうるリスクの大きさを評価し、許容可能なレベルまでリスクを低減するための一連の手順、すなわち「リスクアセスメント」を実施することが不可欠であり、法律(※労働安全衛生法第28条の2)でも努力義務とされています。
※参照 : 厚生労働省 : リスクアセスメントの基本
なぜリスクアセスメントが必要か?
個別の状況に対応するため
ロボットの種類、作業内容、周辺環境、作業者の動きなどは導入先ごとに異なります。安全規格だけではカバーしきれない、その現場特有の危険性を洗い出す必要があります。安全対策の根拠を明確にするため
どのような危険があり、それに対してどのような安全対策を講じたのかを文書化することで、安全性の根拠を客観的に示すことができます。事故を未然に防ぐため
最も重要な目的は、協働ロボットに関連する労働災害を未然に防止することです。協働ロボットは「本質的に安全」なのではなく、「安全規格に適合し、かつ、リスクアセスメントに基づいた適切な措置が講じられて初めて安全に運用できる」という認識が重要です。
リスクアセスメントと安全対策の関係
協働ロボットの導入を検討する上で、「リスクアセスメント」と「安全対策」は、重要な関係にあります。まず理解すべきなのは、リスクアセスメントはそれ自体が目的ではなく、適切な安全対策を導き出すための体系的な「手段」であるということです。リスクアセスメントを行うことで、協働ロボットシステムとその作業環境に、どのような危険(リスク)が、どの程度のレベル(発生可能性と危害の大きさ)で潜んでいるのかを客観的に特定し、評価することができます。
つまり、リスクアセスメントを行うことで、「この作業には、こんな危険がこれくらいある」という事実が明らかになります。この事実に基づいて初めて、「だから、こういう安全対策が必要だ」「このレベルまで安全にする必要がある」と、具体的な安全対策とその目標レベルを、誰にでも説明できる根拠をもって決定できるようになります。経験や勘に頼った曖昧な対策ではなく、リスクに基づいた合理的な安全対策を実施するための、重要なステップがリスクアセスメントなのです。
このように、リスクアセスメントは効果的な安全対策を計画・実施するための基準となるものであり、両者を正しく連動させることによってはじめて、協働ロボットを安全規格に適合させ、法的要求事項を満たし、作業者の安全を確実に守ることができるのです。
次の章では、この重要なリスクアセスメントを具体的にどのように進めていくのか、その方法を解説します。
リスクアセスメントの方法
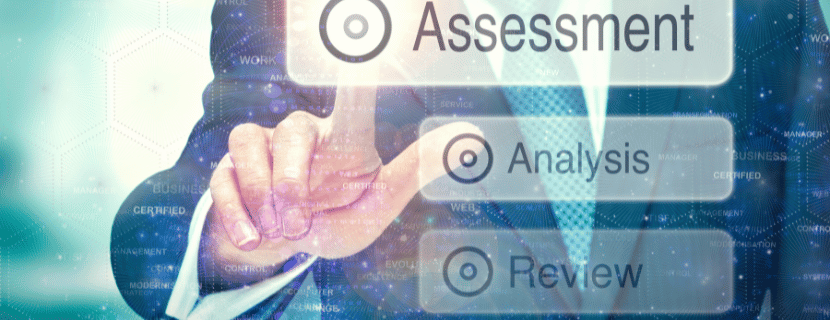
リスクアセスメントは、機械や作業の安全を確保するために、危険を特定・評価し、リスクを許容可能なレベルまで低減する体系的なプロセスです。国際規格ISO 12100に基づき、以下のステップで進められます。
参照 : 日本品質保証機構 : ISO 12100に基づくリスクアセスメントの手法を解説
機械の仕様の明確化
協働ロボットの場合、特に人とロボットがどのように相互作用するのか(接触の可能性の有無、共有する作業空間の範囲、想定される協働作業の内容、ハンドの種類とワーク)を具体的に定義することが重要です。設置場所は、周囲の作業者や設備との位置関係、人の動線なども明確にします。
危険源の特定
機械や作業に潜むあらゆる種類の危険(ハザード)を洗い出します。以下の表1は協働ロボットを使用する際の危険源の一例です。表1 : 危険源の例
カテゴリ | 具体的な危険源の例 | ||||||
機械的危険源 | 挟まれ、巻き込まれ、切断、衝突、突き刺し | ||||||
電気的危険源 | 感電(直接/間接接触)、静電気、短絡(ショート)、過負荷 | ||||||
熱的危険源 | 高温または低温の表面・液体・気体への接触による火傷・凍傷 | ||||||
騒音による危険源 | 聴力損失、作業阻害、警告信号の聞き逃し | ||||||
振動による危険源 | 全身振動または手腕振動による障害 | ||||||
放射線による危険源 | レーザー光、紫外線、赤外線、電離放射線など | ||||||
物質による危険源 | 有害または危険な物質への接触・吸入・誤飲 | ||||||
人間工学的危険源 | 不自然な姿勢、反復動作、過度の力、ヒューマンエラー誘発設計 | ||||||
環境に関連する危険源 | 滑りやすい床、不十分な照明、落下物 |
リスクの見積り:発生確率と危害のひどさ
特定した危険源ごとに、危害が発生した場合の「ひどさ(重篤度)」と、「危害が発生する確率」を組み合わせてリスクの大きさを見積もります。特に協働ロボットでは、人とロボットの接触が想定される場合、その接触が人体に及ぼす影響(力、圧力など)を考慮して『ひどさ』を評価することが重要です。技術仕様書ISO/TS 15066などでは、人体部位ごとの接触に関する許容値(準静的接触、過渡的接触)が示されており、リスク見積りの参考にすることができます。
一般的に以下の表2のような、リスクマトリクスという手法がよく用いられます。(※これは一例であり、レベル区分や表現、評価基準は組織や適用する規格により異なります。自社や関連規格に基づいた基準を設定してください。)
表2:リスクマトリクスの例 (※これは一例であり、レベル区分や表現は組織や規格により異なります)
危害のひどさ(Severity) \ 発生確率(Probability) | ①極めて低い | ②低い | ③中 | ④高い | |||||||
---|---|---|---|---|---|---|---|---|---|---|---|
A. 致命的(死亡・身体機能の永久喪失) | 中 | 高 | 高 | 最高 | |||||||
B. 重篤(不可逆的傷害・長期欠勤) | 低 | 中 | 高 | 高 | |||||||
C. 中程度(可逆的傷害・短期欠勤) | 低 | 低 | 中 | 高 | |||||||
D. 軽微(応急処置のみで回復可能) | 無視可能 | 低 | 低 | 中 |
リスクの評価:許容可能なリスクレベルか?
見積もったリスクレベルが、事前に定めた「許容可能なリスクレベル」の基準を満たしているかを判断します。 この基準は、関連する安全規格(例:ISO 10218-1, ISO 10218-2, ISO/TS 15066)や法規制、企業の安全方針に基づいて設定する必要があり、基準を満たさない(許容できない)リスクに対しては、リスク低減措置が必要となります。リスク低減:3ステップメソッドに基づく安全対策の実施
許容できないリスクに対し、以下の表3、リスク低減の3ステップメソッドなどに従って、優先度の高い順に安全対策を検討・実施します。表3:リスク低減の3ステップメソッド
ステップ | 内容 | 具体例 | ||||
---|---|---|---|---|---|---|
1.本質的安全設計方策 | 設計や仕組み自体で危険源を除去・低減する | 動作速度や力の制限(ISO 10218-1で定義されるPFL) | ||||
2.安全防護及び付加保護方策 | ガードや安全装置で人と危険源を隔離・保護する | 安全柵、扉インターロック、ライトカーテン、両手操作装置、非常停止ボタン | ||||
3.使用上の情報 | 残留リスクに関する情報提供、警告、教育 | 警告ラベル貼付、取扱説明書への記載、警告灯、安全標識の設置、安全教育の実施 |
反復プロセスと文書化
リスク低減策を実施した後、その安全対策が有効か、新たな危険源が発生していないかを再度評価します。そしてリスクが許容レベルになるまでこれを反復します。さらに、実施したリスクアセスメントの全プロセス(機械の仕様、特定した危険源、リスク評価結果、実施した対策、残留リスクなど)を文書化し、記録として保管することが重要です。
特に協働ロボットの場合は、設定された安全機能(例:速度・力制限値、安全監視領域の設定)、その妥当性検証の結果、関連する計算やシミュレーション、テスト記録なども含めて文書化します。
事例を通じてリスクアセスメントを確認
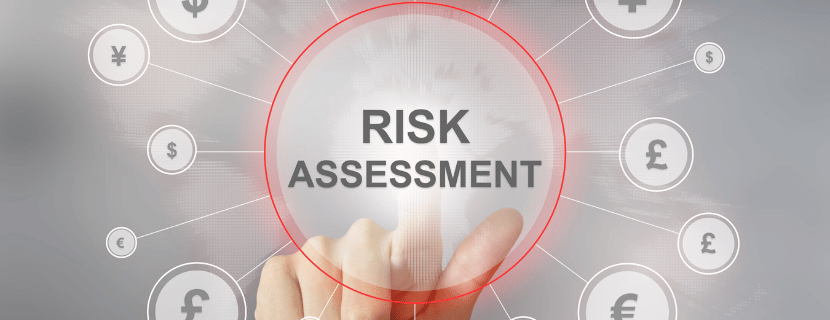
ここでは、リスクアセスメントが実際の現場でどのように進められるのか、簡略化した例を用いて、危険源の特定からリスク低減までの流れを説明します。
部品の手渡し作業(電力・力制限モードを利用)
【状況】協働ロボットが部品を持ち上げ、作業エリアにいるオペレーターがそれを受け取る作業です。このロボットは、人に接触した際の力や圧力を安全なレベルに抑える「電力・力制限(PFL)」モードで動作しています。
【特定された危険源】
オペレーターが部品を受け取る際や、その前後に、意図せずロボットアームと接触・衝突してしまう可能性があります。
【リスク評価(対策前)】
ロボットの力・圧力パラメータは、国際規格ISO/TS 15066に定められた生体組織への許容圧力値を下回るように設定されており、仮に接触・衝突が発生した場合でも、ISO/TS 15066の許容値を下回る設定であれば、重篤な傷害リスクは低減されるが、個人差や状況によっては軽微な傷害が発生する可能性も考えられます。
ただし、作業手順や教育が不十分な場合、発生可能性は「中」となり得るため、リスクは(例:重篤度「軽微」× 発生可能性「中」)となります。さらなる安全対策が必要です。
【リスク低減策】
以下の対策を実施し、リスクを許容可能なレベルまで下げることを目指します。
-
力・圧力の制限と検証
国際規格(ISO/TS 15066)のガイドラインに基づき、ロボットが発生する力や圧力が許容値以下になるようパラメータを設定します。最大速度・最大負荷状態で三次元力センサーを用いて実測し、最悪条件下でも許容値を下回ることを検証します。 -
接触部の配慮
ロボットハンドやアーム表面に鋭利な部分や突起物がないか確認し、必要であればクッション性のあるカバー等で保護します。これにより、接触時の衝撃を和らげるとともに、オペレーターの安全性を高めます。 -
作業手順の明確化
オペレーターがどの位置で、どのタイミングで部品を受け取るのが最も安全かを明確にし、作業手順書に定めます。これにより、不必要な接近や接触の機会を減らします。 -
安全教育の実施
定められた作業手順や、ロボットの動作特性、安全な関わり方をオペレーターに教育し、理解を促します。 -
定期的な検証・点検
6ヶ月ごとにロボットの力・圧力の再測定や、保護カバーの摩耗検査を実施し、継続的な安全性を確保します。 -
緊急時対応の明文化
接触発生時の応急処置手順や、インシデント報告フローを明文化し、万が一の際にも迅速に対応できる体制を整えます。 -
人間工学的配慮
ISO 10218-2に基づき、作業姿勢の評価や反復作業の負荷分析も実施します。
【残留リスク評価(対策後)】
上記の対策を講じた結果、万が一接触が発生しても、ロボットの力・圧力はISO/TS 15066の許容範囲内に収まるため、危害は軽微であり、残留リスクは許容可能なレベルに低減されるが、完全にゼロにはできない。
作業頻度や個人差によっては軽微な傷害が発生する可能性があるため、継続的なモニタリングと教育が必要と評価できます。接触の可能性自体はゼロにはなりませんが、許容範囲内で管理されているため、作業の安全性は十分に確保されています。
ここでは、部品の手渡し作業の際に想定されるリスクアセスメントを確認しました。次に、ねじ締め作業の補佐の際のリスクアセスメントの例を紹介します。
ねじ締め作業の補助(ハンドガイディングモードを利用)
【状況】オペレーターがロボットアームに取り付けられたグリップを持ち、手で直接ロボットを誘導して、ねじ締めを行う位置まで移動させる作業です。「ハンドガイディング」モードが使用されています。
【特定された危険源】
オペレーターがロボットを誘導している最中に、意図しない方向にロボットが動いてしまったり、オペレーター自身がロボットと壁や他の設備との間に挟まれたりする可能性があります。
【リスク評価(対策前)】
挟まれ事故が発生した場合、重い傷害につながる可能性があります。発生する可能性は低いと考えられますが、リスクレベルは「中程度のリスク」(例:重篤度「重い」× 発生可能性「低」)と評価され、対策が必要と判断されました。
【リスク低減策】
以下の対策を実施し、リスクを許容可能なレベルまで下げることを目指します。
-
速度制限
ハンドガイディング中のロボットの動作速度を、安全であると確認された速度(非常にゆっくりとした速度)に制限します。これにより、万が一の衝突時のエネルギーを低く抑えます。 -
有効化スイッチの確保
オペレーターがグリップを握っている間だけロボットが動作し、離すと停止するような有効化スイッチ(イネーブルスイッチ)が、確実に機能するようにします。これにより、危険を感じた瞬間に動作を停止できます。 -
可動範囲の制限
ロボットが動作できる範囲を、作業に必要な最小限のエリアにソフトウェアで制限します。これにより、意図せず危険なエリアへ進入することを防ぎます。 -
安全距離の確保
周辺の壁や設備との間に、挟まれが発生しないように十分な安全距離(スペース)を確保します。
これらの対策の結果、挟まれ事故のリスクは低減されたと判断され、「許容可能なリスクレベル」(例:重篤度「中程度」× 発生可能性「無視できる」)と評価されました。
このように、具体的な作業内容や協働ロボットの運転モードに合わせて危険源を特定し、リスクレベルに応じた適切な対策を講じることが、安全確保の鍵となります。
なお、この章で記載した2つの例はあくまでも協働ロボットの代表的な利用シーンを基にした一例となっております。
これから協働ロボットの導入を考えているが、リスクアセスメントに関して不安や疑問を感じている方は、以下のサービスをご参照ください。
協働ロボットの導入~運用、アフターサービスまで専門家が徹底的にサポートします。また、協働ロボット導入に関しての相談は無料で行っております。
気になる方は以下より、お気軽にご相談ください。
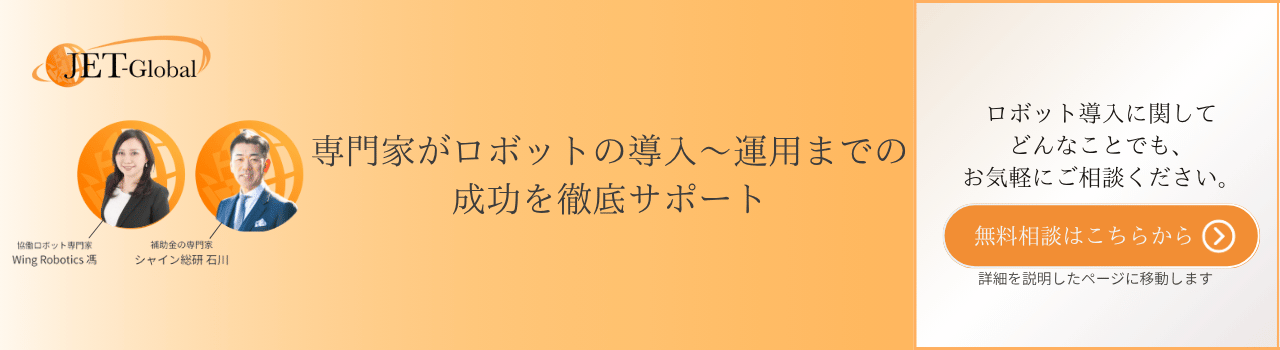
まとめ 安全な協働ロボット活用のために
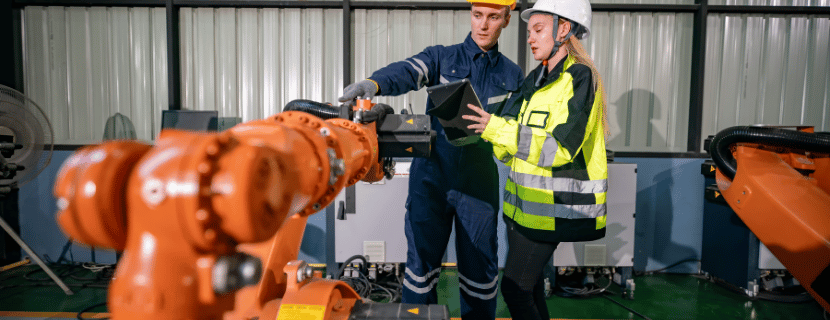
協働ロボットは、生産現場の自動化や効率化に大きな可能性をもたらしますが、その能力を最大限に引き出すためには、安全な運用が大前提であり、安全規格をもとにしたリスクアセスメントが必須です。
本記事の内容をまとめると、以下の3点が重要になります。
安全規格の理解
まず、協働ロボットに関する基本的なルールであるリスクアセスメントの実施
規格に適合しているだけでは不十分なので、個々のロボットシステムや作業環境に合わせて、「何が危険か(危険源特定)」「どのくらい危険か(リスク見積り)」「許容できるか(リスク評価)」「どう対策するか(リスク低減)」を体系的に検討するリスクアセスメントの実施が不可欠です。適切なリスク低減による安全対策
リスクアセスメントの結果に基づき、特定されたリスクに対して適切な安全対策(本質的安全設計、安全防護、使用上の情報)を優先順位に従って確実に実施することが求められます。協働ロボットの導入を検討する際には、これらの安全規格をよく理解し、専門家(ロボットメーカー、システムインテグレーター、安全コンサルタントなど)のアドバイスも積極的に活用しましょう。
そして、導入前に時間をかけて入念なリスクアセスメントを実施し、必要な安全対策を講じることで、初めて人とロボットが安心して共に働ける環境が実現します。
※本記事は協働ロボットの安全規格とリスクアセスメントに関する一般的な情報提供を目的としており、個別の案件に対する安全性を保証するものではありません。実際の導入にあたっては、最新の公式な規格文書や関連法規を確認し、専門家にご相談ください。